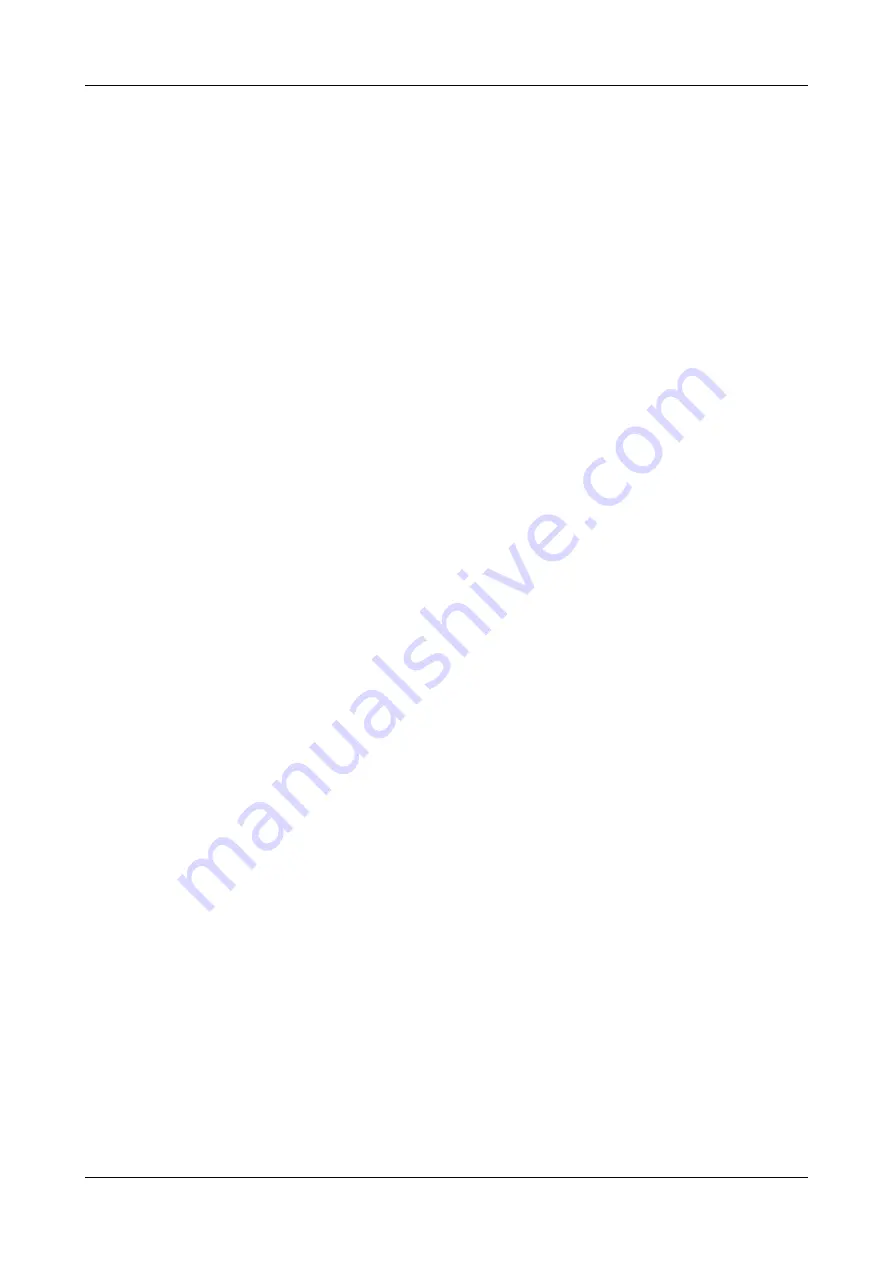
•
Disconnect all power and utility lines.
•
Markings, e.g. on lines, must not be removed.
•
Do not climb on the component. Use suitable access aids and working
platforms.
•
Mark the lines (if unmarked) prior to disassembly to ensure they are not
confused when re-assembling.
•
Protect open line ends with blind plugs against ingress of dirt.
•
Pack sensitive parts separately.
•
For longer periods of standstill, observe the storage conditions, see
Section 4.1, Page 20.
10.2
Inspections
Between the maintenance periods, the valves must be checked for leakage and
proper function.
10.2.1 Bellows
Carry out the following steps:
1.
Check the leakage cavity for soiling and continuous leakage of fluids.
®
The bellows has been checked.
10.2.2 Pneumatic connections
Carry out the following steps:
1.
Check the operating pressure at the pressure reducing and filter station.
2.
Clean the air filter at regular intervals.
3.
Check that the air hoses sit firmly in the air connections.
4.
Check the lines for kinks and leaks.
®
The pneumatic connection has been checked.
10.2.3 Electrical connections
Carry out the following steps:
1.
Check that the proximity switches are positioned correctly and the
connections are clean.
®
The electrical connection has been checked.
10.3
Maintenance intervals
To ensure the highest operational reliability of the valve, all wearing parts should
be replaced at longer intervals. Keep an adequate supply of all wearing parts
(internal assemblies and seals) in your spare parts stock.
In practice, the actual maintenance intervals can only be determined by the user
since they depend on the operating conditions.
Maintenance
Inspections
430BAL013317EN_1
11.03.2019
31
Summary of Contents for Aseptomag AMV
Page 60: ......