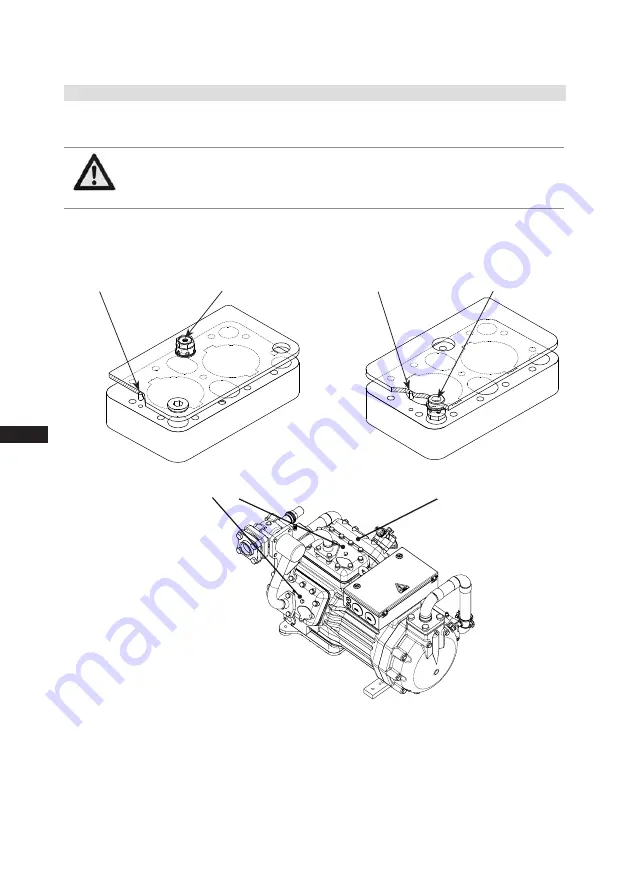
34
D
GB
F
E
09726-06.2018-DGbF
8
|
Maintenance
Safety valve
Safety bolt
Installation of the valve plates:
Valve plate LP stage
Valve plate HP stage
Safety valve
Safety bolt
8.4 Replacing the valve plates
The compressors are divided into an LP and an HP compressor stage. Different valve plate designs
are required because of the different ducts in the individual compressor stages.
Fig. 34
WARNING
The valve plates have been fitted with safety bolts to prevent any confusion.
The safety bolts engage in the corresponding bores on the cylinder
heads,
the safety bolts must not be removed!
Ventilplatte LP-Stufe
Ventilplatte HP-Stufe