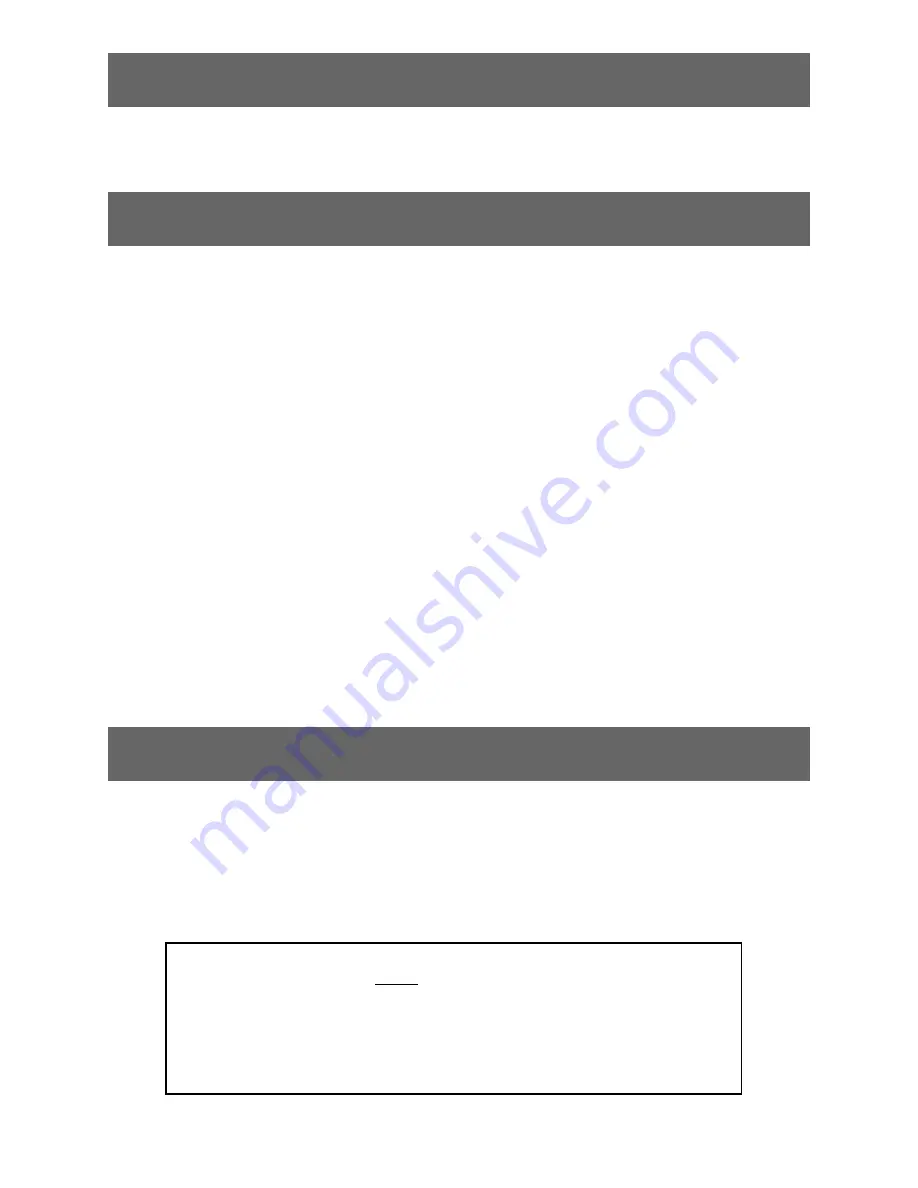
Page
Introduction
. . . . . . . . . . . . . . . . . . . . . . . . . . . . . .
1
2
Safety
. . . . . . . . . . . . . . . . . . . . . . . . . . . . . . . . . . .
1
3
Equipment Inspection and Storage . . . . . . . .
1
3
Final Equipment Inspection . . . . . . . . . . . . . .
1
3
Installation
. . . . . . . . . . . . . . . . . . . . . . . . . . . . . . .
1
4
Engine Start Control Connections . . . . . . . . .
1
4
Initial Energization . . . . . . . . . . . . . . . . . . .
1
4-5
Control Connections . . . . . . . . . . . . . . . . . . . .6
MX150 Microprocessor Controller
. . . . . . . . . . . .
1
7
Overview . . . . . . . . . . . . . . . . . . . . . . . . . . . . .
1
7
LCD & Keypad . . . . . . . . . . . . . . . . . . . . . . . .
1
8
User Setting for Voltage & Frequency . . . . . .
1
9
Standard Features, MSTDG Option Pkg. . . .9-10
Standard Features, MEXEG Option Pkg. . . . .11
Optional Accessories . . . . . . . . . . . . . . . . . . . .12
How to Set the System Clock . . . . . . . . . . . . .13
CDT One Event Timer Exerciser . . . . . . . .13-14
CDP Clock Exerciser . . . . . . . . . . . . . . . . . . . .15
User Setup - CFG Menu . . . . . . . . . . . . . . . . .16
User Setup - SET Menu . . . . . . . . . . . . . . . . . .17
User Setup - System Info . . . . . . . . . . . . . . . . .18
Page
Testing
. . . . . . . . . . . . . . . . . . . . . . . . . . . . . . . . .
1
19
Standard Transition . . . . . . . . . . . . . . . . . . . .
1
19
Delayed Transition . . . . . . . . . . . . . . . . . . . . .19
Sequence of Operation
. . . . . . . . . . . . . . . . . . . . .20
Standard Transition . . . . . . . . . . . . . . . . . . . .
1
20
Delayed Transition . . . . . . . . . . . . . . . . . . . . .20
Relay/Transformer (R/T Box)
. . . . . . . . . . . . . . .21
Standard . . . . . . . . . . . . . . . . . . . . . . . . . . . .
1
21
Delay . . . . . . . . . . . . . . . . . . . . . . . . . . . . . . .
1
22
Schematics . . . . . . . . . . . . . . . . . . . . . . . . . . .
1
23
Troubleshooting & Diagnostics
. . . . . . . . . . . . . . .24
Maintenance and Testing
. . . . . . . . . . . . . . . . . . . .25
Inspection and Cleaning . . . . . . . . . . . . . . . . .25
Servicing . . . . . . . . . . . . . . . . . . . . . . . . . . . .
1
25
Testing . . . . . . . . . . . . . . . . . . . . . . . . . . . . . .
1
25
Table of Contents
Introduction
Authorized Service
For GE parts and service, call: (773) 299-6600
GE Zenith Transfer Switches are used to provide a continuous source of power for lighting and other critical loads by
automatically transferring from source 1 power to source 2 power in the event that source 1 voltage falls below preset limits.
Voltage sensing and system control is performed via a state-of-the-art microcontroller located on the cabinet door.
It is designed to give highly accurate control of the transfer switch system.
All GE Zenith transfer switches are designed for use on emergency or standby systems, and are rated for total system or
motor loads. Transfer switches are UL Listed under Standard 1008 and CSA Certified under Standard C22.2 No. 178 and
IEC Listed under Standard 947.
NOTE
S: A protective device such as a molded case circuit breaker or fused
disconnect switch MUST be installed on both sources of incoming
power for circuit protection and as a disconnection device.
All references made within this manual about the term “S1” or
“Source 1” relate to a Normal Power Source. All references made
about the term “S2” or “Source 2” relate to an Emergency
or Alternative Power Source.