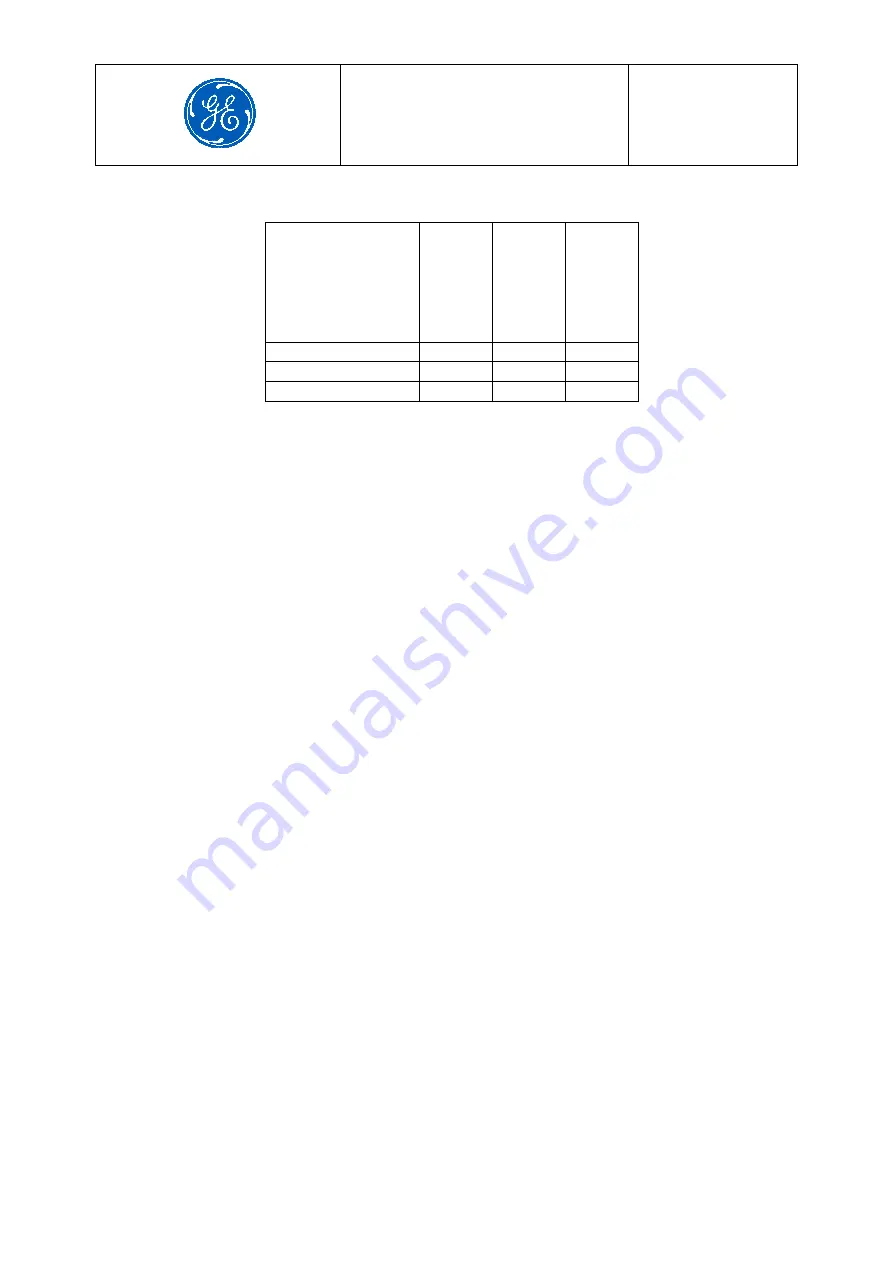
Nuova Via di Piano Comprensorio Vulcano
Sesto San Giovanni, MI 20099 Italy
Tel. 02-24105.001
IS 2653 GB
Page
15
of
18
Time base
V
is
u
a
l
in
s
p
e
c
ti
o
n
U
V
c
a
m
e
ra
a
n
d
in
fr
a
re
d
e
x
a
m
in
a
ti
o
n
W
e
tt
a
b
il
it
y
6 Months
X
1 Year
X
X
When plant is off
X
X
Table 2 – Composite insulator maintenance plan
Visual inspection:
Carefully check that the composite insulators sheds do not show any mechanical damages and significant
tracking or erosion due to electrical stress.
Visually evaluate also the pollution status and identify the areas of concentrated contamination.
Take note of the position of the areas of evidences, to be carefully analysed and taken under control during
future inspections. In case of evidence of incipient erosion / tracking, plan an immediate washing action.
UV camera and infrared examination:
Scan all the surface of the composite insulators with an UV camera to identify possible areas of intense UV
emissions on the sheds, on the toroids and the incoming line cables. To perform this test, the camera must be
properly set in order to avoid false signals and background noise.
In addition, an infrared scan on the line terminal and the incoming cables can reveal incipient hot spots
phenomenon that can evolve into a serious damage on the electrical connection and then of the bushing itself.
In case of significant variation of the UV and IR emission, plan the following actions:
UV emission: Immediate washing action on the interested part, in the meanwhile control all electrical
connections.
IR emission:
Immediate control of all electrical connections.
Wettability:
The hydrophobicity of the composite insulator can be checked by following the methodology described in IEC
TS 62073 – 2003 Guidance on the measurement of wettability on insulator surfaces.
The simplest way to assess the wettability is the Method C - Spray method.
Wettability level up to WC4 is acceptable for normal operation. In case of further degradation of wettability level
(WC5 and WC6) proceed with an accurate washing and drying and then repeat the test.
If wettability remains low but there are no evidences of tracking or erosion keep the bushing in operation but
follows the intensive maintenance plan of
Table 3
.