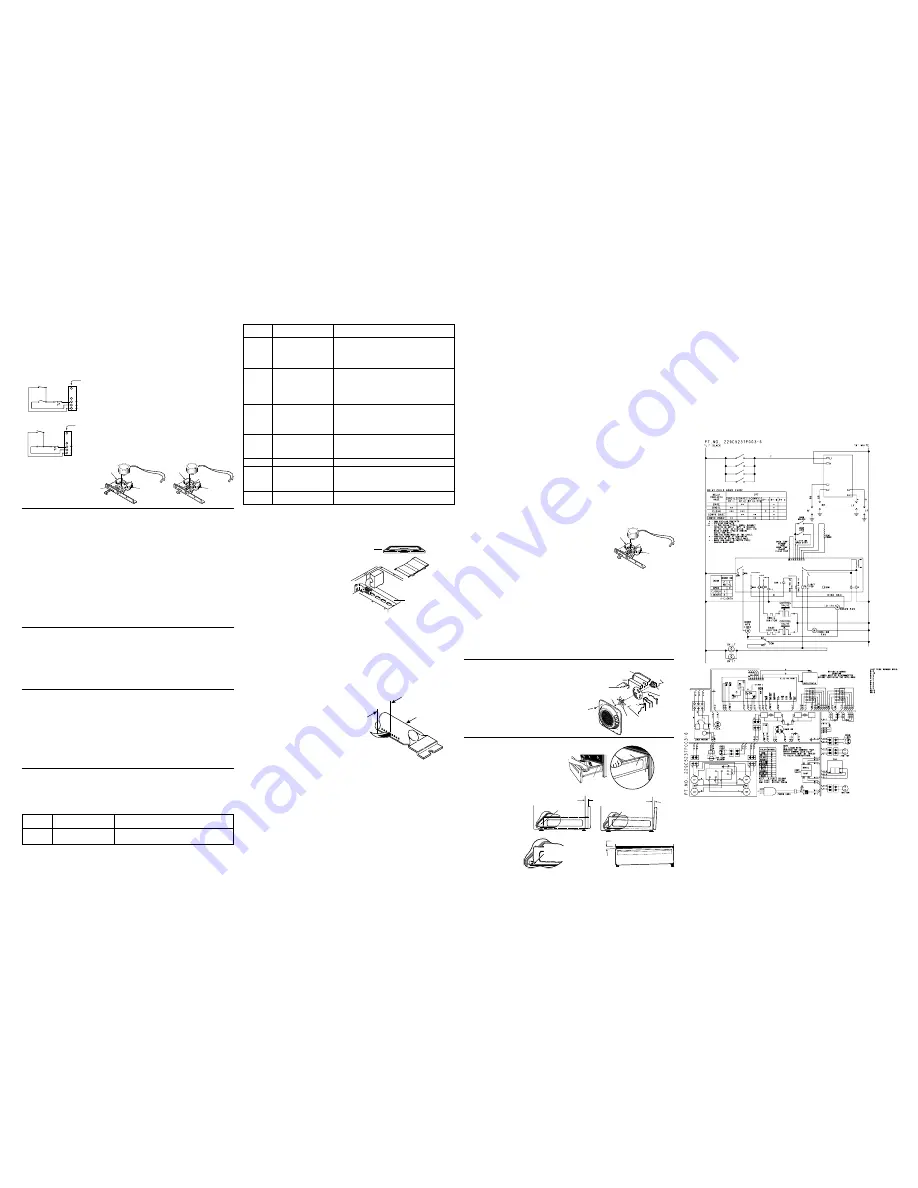
COLD START ODOR ADJUSTMENTS
NOTE: A small amount of odor is normal and will be present when the range is first turned on.
Also, adjustments require disassembly of the burner section. To prevent handling hot parts,
oven should be cool.
STEP 1: Remove oven door, oven bottom,
flame spreader (burner baffle), orifice
cover and oven burner. See below.
STEP 2: Closely Examine the Angle of
the Orifice. The orifice must point straight
into the burner. Check the angle by
looking at the orifice from above and from
the front. A socket Head Nut Driver may
be placed over the maintop orifice to help
determine any out of alignment condition.
The angle can be corrected by using a
small adjustment wrench clamped loosely
over the orifice to bend the orifice and its
mounting assembly as needed. See below.
STEP 3: Inspect the Primary Air Opening. The opening must be clear and free of insulation
all the way down to the metal shield below (0.314 inch opening). See above.
STEP 4: Using a drill bit as a gauge, adjust the air shutter opening.
COLD START ODOR ADJUSTMENTS
STEP 5: Examine the orifice cover. The cover must be as air-tight as possible. Bend the cover
to close off gaps between the sides and the top of the cover.
STEP 6: Install the oven door and observe the burner flame. Before installing the flame spreader
and oven bottom, close the oven door, set the control for BAKE and observe the burner flame.
Note: The door should remain closed during this test.
NOTE: When door is either
being locked or unlocked,
both lock switches will be in
the open position.
OVEN SENSOR AND DOOR LOCK SWITCH
MOTORIZED DOOR LOCK
The motorized door lock assembly is located above the oven. The assembly consists of a lock motor
cam and switch assembly, lock hook and mounting plate.
MOTORIZED DOOR LOCK OPERATION
The lock motor is energized when the control is set for Clean and Clean Time is selected. The K4
Relay contacts will close and complete the circuit that supplies the voltage to the lock motor.
HTI
HTI
Tech & Ind
HTSYG048B002FL45
-0001
Date:
Made in China
LOCK SW.
N.O. CONTACT
CLOSED
UNLOCK SW.
N.O. CONTACT
OPEN
CAM IN
LOCK POSITION
LOCKED
HTI
HTI
Tech & Ind
HTSYG048B002FL45
-0001
Date:
Made in China
LOCK SW.
N.O. CONTACT
OPEN
UNLOCK SW.
N.O. CONTACT
CLOSED
CAM IN
UNLOCK POSITION
UNLOCKED
5
4
3
6
8
DOOR UNLATCHED INPUT PIN
DOOR LATCHED INPUT PIN
SENSOR AND LOCK
SWITCH CONNECTORS
LOCK SW. #1
LOCK
SW. #2
LOCK SW. CIRCUIT
UNLOCKED
THERMAL SWITCH
DOOR LATCH OUTPUT PIN 5, -25V DC
5
4
3
6
8
DOOR LATCH OUTPUT PIN 5, -25V DC
DOOR UNLATCHED INPUT PIN
DOOR LATCHED INPUT PIN
SENSOR AND LOCK
SWITCH CONNECTORS
LOCK SW. #2
LOCK
SW. #1
LOCK SW. CIRCUIT
LOCKED
THERMAL SWITCH
NOTE: Control display will flash “LOCK DOOR”
if the door switch is in the “C” to “NC” position
(door open).
•
The words “LOCK DOOR” will flash on and off
in the display while the lock motor is in motion.
When the door is locked, the words “LOCKED
DOOR” remain illuminated in the display.
•
CAM – The cam on the motor performs two
functions:
1. Positions the lock hook in the door to
prevent opening during clean operation.
2. Operates the lock switches which tell the
control if the door is unlocked or locked
and ready for Clean operation.
SPECIAL FUNCTIONS
The control has a section that can be entered to change how the control will work. To enter this section:
Press and hold BAKE and BROIL pads for 2 (two) seconds and “SF” appears in the display. Select
the area to change. When the change has been made, press START to return to Time of Day.
•
End-of-Cycle Tone – Press TIMER pad. Display shows “Con Beep” when control is set for
continuous End-of-Cycle Tone or “Beep” when set for noncontinuous.
•
°
F or
°
C – Press BROIL pad. Display will show either “F
°
” or “C
°
.” Press BROIL pad again to
change.
•
12-Hour, 24-Hour or blank out Time-of-Day Clock – Press CLOCK pad. Display will show
“12 hr,” “24 hr,” “OFF” for blank clock. Press again to change.
•
12-Hour Shutdown comes set to shut down after 12 hours of continuous operation; this can be
eliminated—press DELAY START pad. Display will show “No Shdn.” To turn back on, press
DELAY START pad again and display will show “12 Shdn.”
•
Sales Mode (special feature for sales floor demonstration) – Press CLOCK and TIMER pads
at the same time. Display will start to cycle through the different modes of operation.
•
Sabbath Mode – This feature disables all but Bake and Timed Bake, overrides 12-Hour
Shutdown, disables beeps and puts symbols in the display during Bake. Access by pressing
DELAY START pad until display shows “SabbAtH.” Exit by pressing DELAY START until
“No Shdn” or “12 Shdn” shows.
THERMAL SWITCH
The thermal switch is located on the floor of the component compartment in front of the fan
motor. The thermal switch is wired in series with the lock motor switches. The limit switch
opens at 275
°
F and closes when temperatures cool below 205
°
F. If the thermal switch opens during:
1. Oven Temperature Below 600
°
F, program is cancelled when thermal switch opens. Lock motor
will run and the words “LOCK” and “DOOR” will be flashing in the display.
2. Oven Temperature Above 600
°
F, any mode of operation control will go to -F2- failure code. When
this condition exists, check the fan operation (look for obstructions), inspect oven installation
(make sure grille areas are not blocked), oven insulation and lock circuit.
FAILURE
CODE
MEANING
CORRECTION
Over temperature
1. Inside oven cavity as
measured by sensor
over 650
°
F unlatched
or 915
°
F latched
•
Welded relay contacts
•
Cooling fan stalled or blocked
•
Airflow to rear of unit
•
High resistance in oven sensor leads/connectors
(especially at sensor in rear)
-F3-
Open oven sensor (under
950 ohms)
•
Disconnect power. Disconnect sensor harness from
control. Measure sensor resistance (white leads) to
be ~1080 ohms at room temperature with 2 ohms
per degree change.
•
Look for damaged harness terminals if not a bad
sensor.
Shorted oven sensor
(over 2900 ohms)
•
Disconnect power. Disconnect sensor harness from
control. Measure sensor resistance (white leads) to
be ~1080 ohms at room temperature with 2 ohms
per degree change.
•
Separate sensor from harness to determine fault.
Shorted matrix or START
key
Determine if problem is with key panel or control by
disconnecting ribbon cable and measuring flat cable
using pinout chart. Allow up to 1000 ohms when
pressing a key.
-F2-
-F4-
-F7-
EEPROM data shift failure
If repeated, replace control.
Cooling fan or airflow to control area.
Cooling fan stalls while
above 650
°
F; open
thermal switch in yellow
leads
-F8-
-F9-
Loss of latch motor safety
circuit
Replace control.
-FC-
FLAME
SPREADER
ORIFICE COVER
SELF-CLEAN & MOTORIZED DOOR LOCK
OPERATION LOCK CIRCUITS
There are two circuits controlling the locking and unlocking of the door. These are the lock motor
circuit and the lock switch circuit.
The lock motor circuit applies voltage (120 VAC) to the lock motor. This circuit is from L, through
the door switch, lock relay, lock motor to neutral. For this circuit to be complete, the lock relay must
be energized by the (HP) control and the door must be closed. An open oven door results in “LOCK
DOOR” flashing in the display after the control has been programmed for clean and “START” has
been depressed.
The lock switch circuit “tells” the control if the lock motor is in the unlocked or locked position or
somewhere in between. There are two lock switches mounted to and operated by the lock motor.
The lock switch circuit is from the (HP) control, through one of the lock switches (switch 2 for
unlocked or switch 1 for locked) back to the (HP) control. If neither switch is closed, and the oven
temperature is below 600 degrees, the (HP) control will energize the lock motor circuit until the
correct switch closes to complete the circuit. (If circuit to the correct switch is open, lock motor will
run continuously with the oven below 600 degrees.)
CLEAN CYCLE AND LOCK SEQUENCE
1. Program the Clean Cycle:
•
Press “SELF-CLEAN” pad. 4 hours (4:00)‚ appears on the time display. (Cleaning time can
be changed from the 4-hour starting point by pressing the “SELF-CLEAN” pad a second time.
•
After “START” has been pressed, the word “ON” illuminates in red to indicate the cycle
has begun.
2. Locking the Door:
•
After programming the clean cycle and pressing START pad, the control energizes the lock
relay. Voltage (120 VAC) is applied to the lock motor circuit. Oven door must be closed before
lock motor can run. “LOCK DOOR” will flash and control will beep until the door is closed.
•
The lock motor begins to revolve and turns a cam mounted to the motor shaft.
•
The words “LOCKED DOOR” will flash on and off on the display while the lock motor
is in motion.
•
As the cam revolves about 1/2 revolution (approximately 12 seconds), it has moved the
lock “hook” into a corresponding slot in the oven door which secures the door.
•
The movement of the cam has also closed lock switch 1 which
“tells” the control the door is locked. The control then removes
power from the lock motor circuit by de-energizing the lock
relay.
•
The lock motor stops and lock switch 1 is held closed by the
cam through the clean cycle.
•
The words “LOCKED DOOR” stop flashing and remain
illuminated in the display.
•
The word “ON” illuminates in the display.
3. During the Clean Cycle:
•
The BROIL relay closes (audible “click”) and the broil burner begins to heat. The broil burner only
will operate during the first 30 minutes of the clean cycle followed by the bake burner only during
the remaining time.
•
As the clean cycle progresses and the temperature of the oven control area rises, the cooling fan
is activated.
•
A normally closed thermal switch is mounted on a bracket in front of the cooling fan. This switch
is in the lock switch circuit and will open the lock switch circuit in the event of an over-temperature
condition in the control area (caused by a stalled fan, fan switch failure or similar condition).
An -F2- (over-temperature) failure code will appear on the control if this switch opens while the
oven is above 600 degrees. With the oven between 400 to 600 degrees, the clean cycle will be
cancelled by the opening of the switch and the control will revert back to the time-of-day mode.
Below 400 degrees, the lock motor will revolve continuously and the words “LOCKED DOOR”
will flash on the control until the circuit is reestablished.
•
The oven will cycle to maintain an average clean temperature of 830
°
F.
HTI
HTI T
ech
&
Ind
HTSYG048B002FL45
-0001
Date:
Made in China
LOCK SW.
N.O. CONTACT
CLOSED
UNLOCK SW.
N.O. CONTACT
OPEN
CAM IN
LOCK POSITION
LOCKED
TO REPLACE:
1. Place the drawer rail on
the guides.
2. Push the drawer in until
it stops.
3. Lift the front of the
drawer and push in until
the stops clear the
guides.
4. Lower the front of the
drawer and push in until
it closes.
——— If Drawer is Crooked ———
——— If Drawer Won’t Close ———
TO REMOVE:
1. Pull the drawer out until it stops.
2. Lift the front of the drawer until the stops
clear the guides.
3. Remove the drawer.
STOP
STOP
GUIDE
RAIL
Drawer does not close completely
Power cord may be
obstructing drawer
in this area
Drawer front panel tipped
away from body side
Rear drawer support
is resting on top of
guide rail
Drawer front panel tipped to one side
Rear drawer support
on top of guide rail
on the high side
STORAGE DRAWER REMOVAL
REMOVABLE OVEN DOOR
COMPONENT COMPARTMENT AIRFLOW
The oven uses a fan for cooling the components. Air is pulled in by the fan blades and circulated in
the component compartment. The air is exhausted through louvers below the control panel and out
the slots above the door.
DOOR ASSEMBLIES:
The doors can be separated into two assemblies: (1) Outer assembly which consists of handle, vent
trim, outer glass, bottom trim and frame; (2) Inner assembly which consists of inner panel, gasket,
glass panels and insulation. The assemblies are held together by 2 screws on each side, along with
4 screws across the bottom.
CAUTION: Care must be taken when mounting door handle not to overtighten handle screws.
Overtightening screws can damage handle. Hand-tighten screws (do not use electric driver).
Make sure handle fits snuggly to door panel.
SELF-CLEAN DOOR GASKET: The door gasket is attached to the inner door panel by a chain of
spring clips.
1. Locate spring clip at center of gasket and insert in hole on inner door panel near top.
2. Install gasket by bending at 90
°
beside clip and rocking into hole.
3. Tuck loose ends into slot at the bottom of inner panel.
Pub No. 31-14450
06-06 JR
IMPORT
ANT
SER
VICE
INFORMA
TION
DO NOT
DISCARD
JGS968
MODEL NUMBER
FAN
BLADE
OVEN
LINER
OVEN
INSULATION
OUTER
BACK
PANEL
CONV.
FAN
(3)
SCREWS
(4)
SUPPORT
OVEN
CAVITY
MOUNTING
SCREWS
(3)
CONV.
FAN
MTG.
SCREWS
FAN
BLADE NUT
TO SERVICE FAN:
Fan blade can be replaced from inside
oven. Oven must be removed from
installation to access convection fan motor.
CONVECTION FAN ASSEMBLY
The convection fan assembly is located on the back
wall of the oven liner behind the panel with the screen
in the center.
•
Remove 4 screws mounting panel
(2 on each side) and pull forward.
229C4059P613
OVEN BOTTOM
Observe the flames for a period of at least 2
minutes. The flame should not “lift or blow off” the
burner during any period of operation. It should be
blue with approximately a 1/2" to 3/4" inner cone.
LP Gas Installations: If flames lift off the burner
and appear unstable, reduce the air shutter
openings an additional 1/32", cool range and repeat
Step 6 from a cold start. If flames are too large but
appear stable, check to be sure the range was
properly converted.
Natural Gas Installations: If flames are too large
but appear stable, tighten the orifice hood to reduce
the gas flow to the burner.
1/2" To 3/4"
Inner Cone of Flame
Oven Broiler
Burner
STEP 7: Examine Flame Spreader for signs of warpage. If warped, spreader will have to be
replaced.
STEP 8: Install Flame Spreader and Oven Bottom. With customer present, test range from a cold
start to be sure odor problem has been corrected.
BURNER
OVEN CALIBRATION
Testing has shown that this oven has the best cooking performance at a control setting of 350
°
F
when the AVERAGE center oven temperature is between 350
°
F and 390
°
F. Customers may change
the average center oven temperature by
±
35
°
F to satisfy their own cooking needs.
To change:
•
Press and hold BAKE and BROIL pads until “SF” appears in display.
•
Press BAKE pad to enter oven calibration mode. “00” appears if oven calibration has not
been changed previously. If oven calibration has been changed previously, a temperature
between
±
35
°
F will be displayed.
•
Use number pads to change average oven temperature. (Use BAKE to switch b or -
settings.)
•
Press START pad to return to Time of Day.
ERC FAILURE CODES
The oven may stop operating but not give an F code on the display immediately. F codes are stored
in nonvolatile eeprom memory until the same fault occurs twice consecutively. F codes can be
recalled by pressing together TIMER, CLOCK and 9. While F codes are displayed, pressing 8 and 6
together will clear them. A fault must exist continuously for 5 minutes before an F code is recorded
(F2 and F8 are sooner).
FAILURE
CODE
MEANING
CORRECTION
Shorted OFF key
(Membrane) or GT Error
-F0-
Perform glass touch board key panel test.
NOTE: RY references on control may be different than shown.