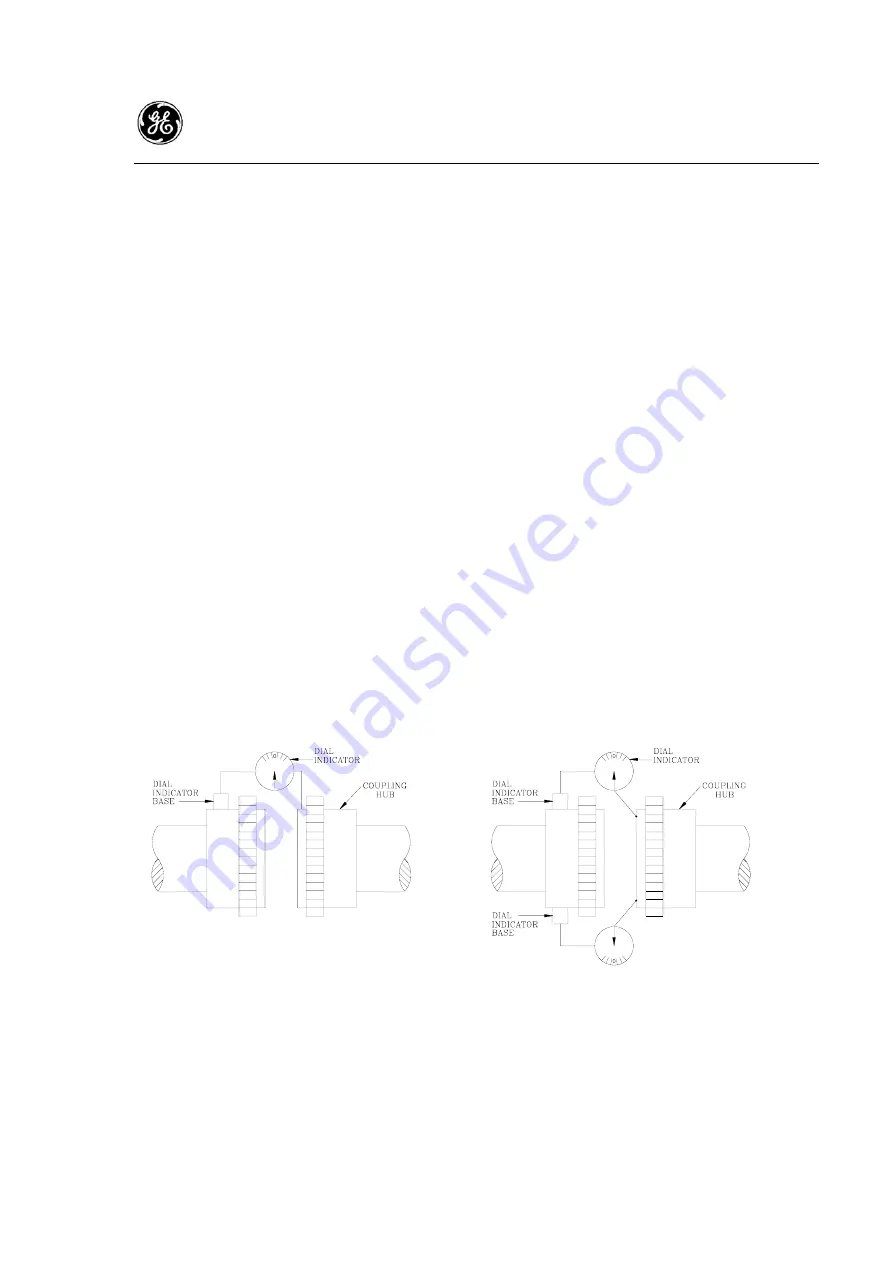
GE Energy Motors GEEP-427-I Copyright 2009, The General Electric Company, USA
11
GEEP-427-I Pegasus, Horizontal Induction Motor
TEWAC, Sleeve Bearing
Fig. 2. Arrangement of indicator for parallel alignment
Fig. 3. Arrangement of indicators for angular alignment
Flexible couplings should not be used to
compensate for inadequate initial alignment of the two
coupling halves. Refer to the instructions supplied by the
flexible coupling manufacturer. Coupling parts, such as
pins, links, buffers, and spacers should be removed
(depending on the type of coupling) and the sleeves
should be axially moved over the shaft to expose the
active hub portions of the coupling halves. The spacing
between coupling hubs should be that recommended by
the coupling manufacturer.
The parallel and angular alignment of the two
coupling halves may be accomplished using the
procedures outlined below, provided the procedures do
not conflict with requirements supplied by the coupling
manufacturer. If a machined, vertical surface is not
accessible on one or both coupling halves, feeler or block
gauges may be substituted for the two dial indicators in
performing the angular alignment check. The two
coupling halves should be aligned to within 0.001-inch
parallel and 0.0015-inch angular misalignment. After the
flexible coupling halves are aligned, the coupling should
be lubricated and assembled in accordance with the
coupling manufacturer’s instructions.
Parallel Alignment for Flexible
Couplings
Position the motor or generator on the foundation
with the plane of its feet horizontal as discussed
previously under Mounting. Then, axially position the
rotor in its magnetic center using the pick punch marks
on the drive end. Axially position the motor with respect
to the machine as discussed in the section entitled
“GENERAL” in the publication. Attach a dial indicator
on one coupling hub with the indicating button on the
machined, circumferential surface of the other coupling
hub. See Fig. 2.
Set the dial indicator zero. Mark the location of
the indicating button with a visible mark. Rotate each of
the two shafts in 90 degree increments, and successively
read and record the dial indications when the indicator is
at 3:00, 6:00, 9:00 and 12:00 o’clock angular positions.
The indicating button must be positioned on the mark for
each reading.
Adjust the shaft position such that the difference
between the two side readings (3:00 and 9:00 o’clock)
and between the top and bottom readings (12:00 and 6:00
o’clock) is less that 0.001-inch. This may require several
iterations. Lateral (3:00 and 9:00 o’clock) differences are
corrected by lateral movement of the unit. Vertical
(12:00 and 6:00 o’clock) differences are corrected by
appropriately adding or removing mounting shims. The
proper shim location is shown on the outline drawing.
Note that the total number of shims in a given shim pack
under any one foot should not exceed five, because too
many shims may provide a “soft” mount on that foot.
This condition could cause dynamic problems.
Drilled and tapped holes are provide in the motor
or generator feet for jacking screws as a convenience in
alignment. Note that jacking screws must not be used for
permanent support.
Angular Alignment for Flexible
Couplings
Axially separate the coupling halves to their
maximum end float. Attach a dial indicator on one
coupling hub with the indicating button positioned
against vertical, machined surface on the other coupling
hub. Attach a second indicator hub 180 degrees apart.
See Fig. 3. Mark the locations of the indicating button
with a visible mark.
Summary of Contents for Pegasus MHV EP-427-I
Page 46: ...GE Energy Motors 46 ...