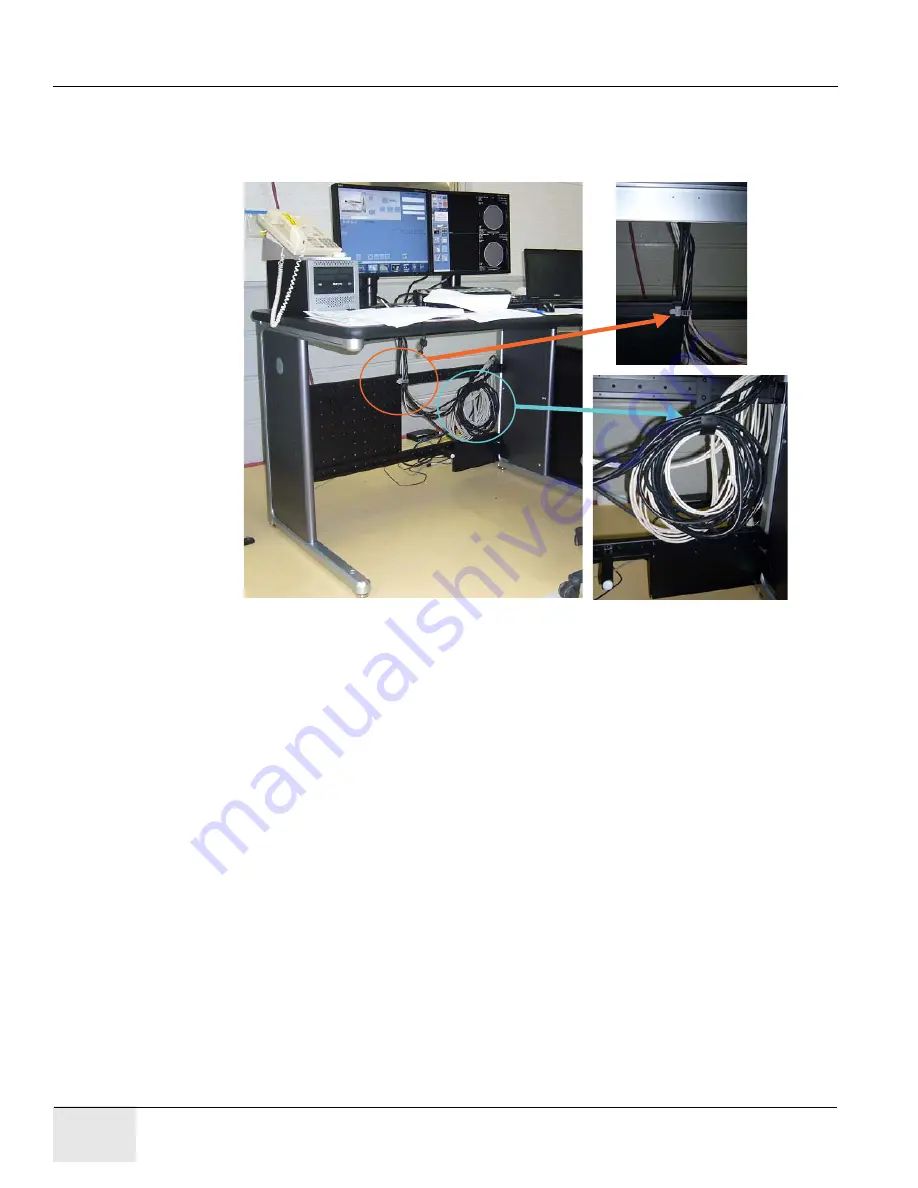
GE C
OMPANY
D
IRECTION
5472001-1EN, R
EVISION
6
O
PTIMA
CT680 S
ERIES
AND
O
PTIMA
CT670 I
NSTALLATION
M
ANUAL
Page 114
Section 3.0 - Console Connections
3.7
Cable Arrangement
Arrange the cables appropriately by using the cable clamps equipped on the console tables.
Figure 2-17 Example: Cable Arrangement
Summary of Contents for Optima CT670
Page 205: ...CT ...
Page 206: ...206 www gehealthcare com ...