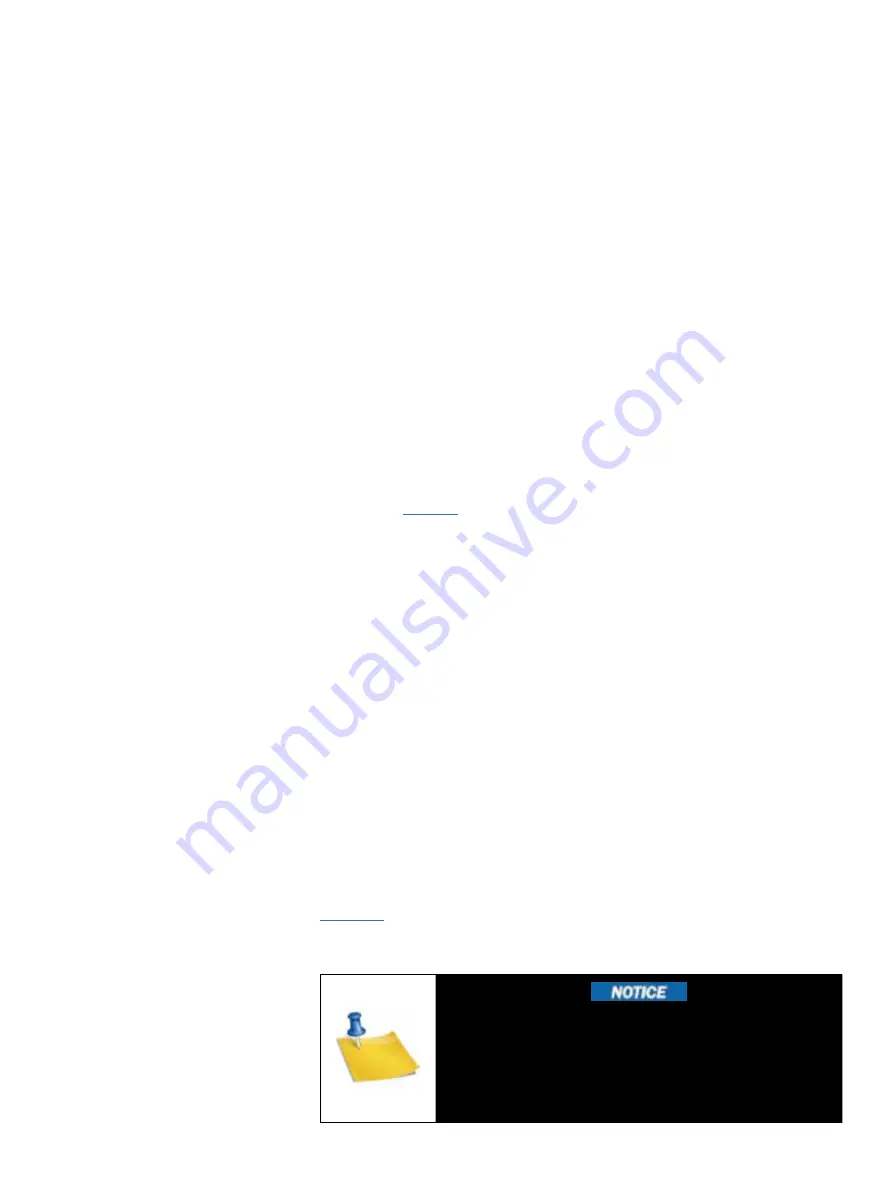
46 | Chapter 4: Installation
3. Check the crankshaft end thrust using a dial indicator with resolution
increments of 0.001" (.0254 mm).
4. Rotate the compressor crankshaft to position a counterweight near the top of
the crankcase.
5. Mount the indicator base on the top cover gasket surface of the crankcase.
6. Position the dial indicator contact point on the counterweight face enabling
the dial to register axial crankshaft movement.
7. Use a pry bar to move the crankshaft towards the drive end solidly against the
thrust bearing washer.
8. Zero the dial indicator with the crankshaft at its extreme drive end position.
9. Use the pry bar to move the crankshaft towards the non-drive end solidly
against the thrust bearing washer.
10. Observe the dial indicator reading.
11.
Pry the crankshaft back and forth several times to confirm accuracy and
repeatability of the readings.
12.
Compare the measured end thrust clearance with the end thrust specification
found in
. Confirm that the driver’s end thrust clearance and confirm
that the result is within the driver manufacturer’s specifications.
Skid Hold-Down Bolting
Proper hold down bolting selection, installation, and torque are required to transfer
and resist normal inherent reciprocating compressor shaking forces and couples
into its skid. Failure to install and maintain the compressor’s mounting fasteners
can result in equipment vibration, drive train misalignment, and compressor main
bearing bore misalignment (soft foot).
Reciprocating compressors develop unbalanced forces and couples due to the
tolerances in the reciprocating weights and the offset of the opposing compressor
throws. The unbalance results in the presence of horizontal and vertical forces and
couples. To offset these unbalanced forces and couples:
1. Design the compressor skid and foundation to dampen and transfer these
shaking forces originating from the compressor into the skid and foundation.
2. Secure the compressor frame mounting and crosshead guide to the skid to
minimize the vibrations associated with these forces.
Recommended bolt Size/Torque
lists the hold down bolting sizes and minimum torque requirements
recommended for HSR compressors. To secure the compressor frame feet to the
compressor skid use high strength studs and bolts.
Bolt lengths extending only through the compressor
mounting foot and I-beam may not be sufficient to prevent
loosening. Verify the hold down bolts have proper torque as
directed in the quarterly maintenance schedule.
Complies with ANSI Z535, ISO 3864, OSHA 1910.145 (f) (9)
Summary of Contents for H301 Series
Page 1: ...High speed reciprocating compressors H301 and 302 series operating manual GE Oil Gas ...
Page 10: ......
Page 17: ...H301 302 HSR Compressors Rev 2 2 7 ...
Page 18: ......
Page 30: ......
Page 48: ......
Page 61: ...H301 302 HSR Compressors Rev 2 2 51 ...
Page 62: ......
Page 76: ......
Page 98: ......
Page 103: ...H301 302 HSR Compressors Rev 2 2 93 ...
Page 104: ......
Page 114: ...104 Chapter 8 Maintenance Figure 21 Effective rod extension amount pocket is open ...
Page 120: ......
Page 129: ......
Page 130: ......
Page 135: ...H301 302 HSR Compressors Rev 2 2 5 ...
Page 137: ......