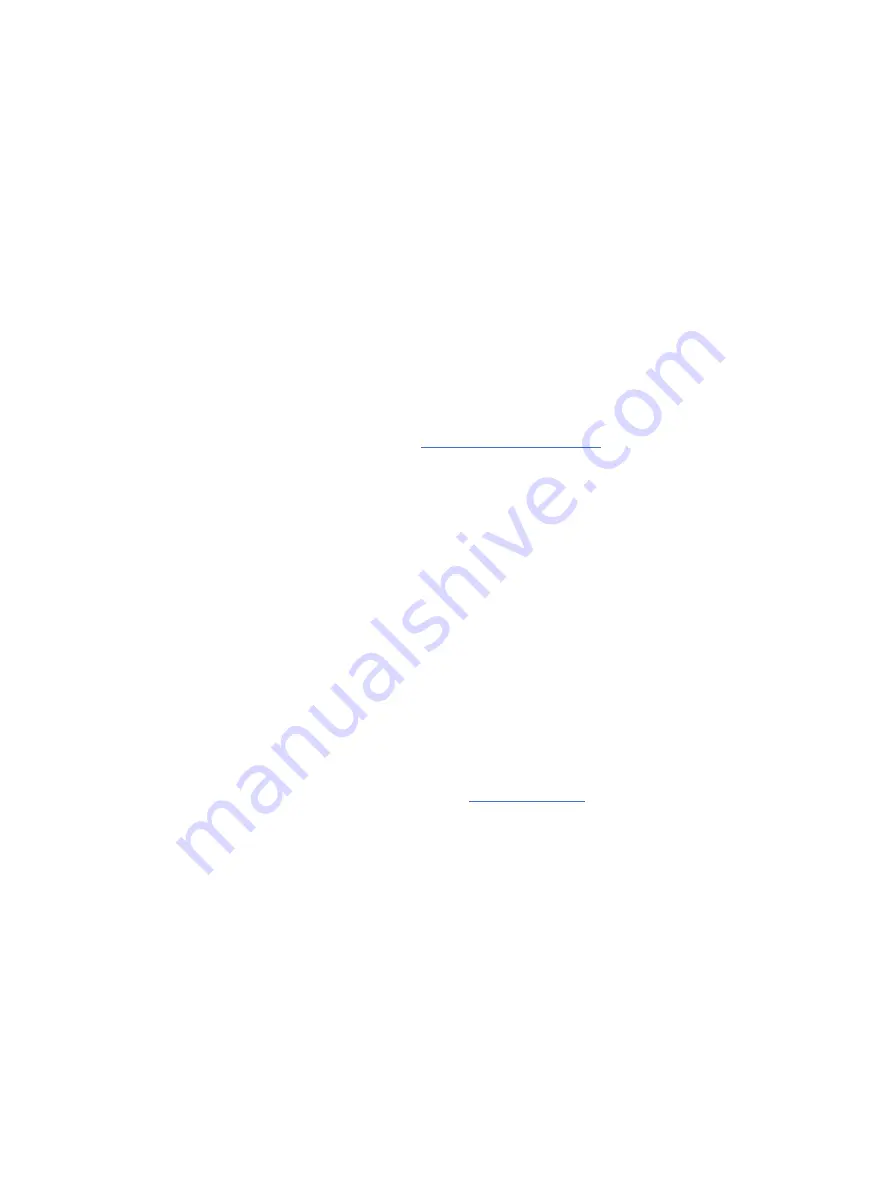
90 | Chapter 7: Vibration
Mechanical
Possible causes of excessive mechanical vibration include:
•
Loose hold-down bolting
•
Loose distance piece to cylinder or frame bolting
•
Loose cylinder support
•
Possible frame distortion
•
Improper distance piece support
•
Improper discharge bottle support
•
Drive coupling misalignment
•
Process gas pipe binding or misalignment
Check each area individually to determine if there is a problem and correct the
cause, (Refer to
).
Inertia Unbalance
Unacceptable vibration amplitudes, due to unbalanced reciprocating weights,
may cause excessive shaking forces and couples. Unbalanced couples cannot be
eliminated, but are minimized by balancing the opposing throws.
Determine the weight of each throw by weighing these reciprocating components:
•
Crosshead and associated balance weights
•
Piston rod assembly with piston rings and crosshead jam nut
Select and add balance weight(s) equal to the difference between the reciprocating
weight of the opposing throws to the piston rod assembly having the lowest
weight. For applications having a blank throw, add balance weight(s) to the blank
throw crosshead.
The maximum out-of-balance weight between the opposing throws is
4 ounces
(0.25 lb., 0.113 kg)
. See
for balancing procedures.
Unbalanced couples due to rotating weights can cause vertical and horizontal
movement at the crankshaft’s speed frequency.
Unbalanced forces due to reciprocating weights can cause axial and horizontal
movement at the crankshaft rotation frequency or multiples thereof.
For example, primary vibration is at crankshaft speed,
1800 RPM = 1800 CPM = 30 Hertz (Hz).
Secondary vibration is at two times crankshaft speed,
3600 RPM = 3600 CPM = 60 Hz.
The compressor skid and foundation must absorb these inertia forces and couples.
Measure the vibration, caused by inertia unbalance, with handheld vibrometers or
electronic analyzers.
Summary of Contents for H301 Series
Page 1: ...High speed reciprocating compressors H301 and 302 series operating manual GE Oil Gas ...
Page 10: ......
Page 17: ...H301 302 HSR Compressors Rev 2 2 7 ...
Page 18: ......
Page 30: ......
Page 48: ......
Page 61: ...H301 302 HSR Compressors Rev 2 2 51 ...
Page 62: ......
Page 76: ......
Page 98: ......
Page 103: ...H301 302 HSR Compressors Rev 2 2 93 ...
Page 104: ......
Page 114: ...104 Chapter 8 Maintenance Figure 21 Effective rod extension amount pocket is open ...
Page 120: ......
Page 129: ......
Page 130: ......
Page 135: ...H301 302 HSR Compressors Rev 2 2 5 ...
Page 137: ......