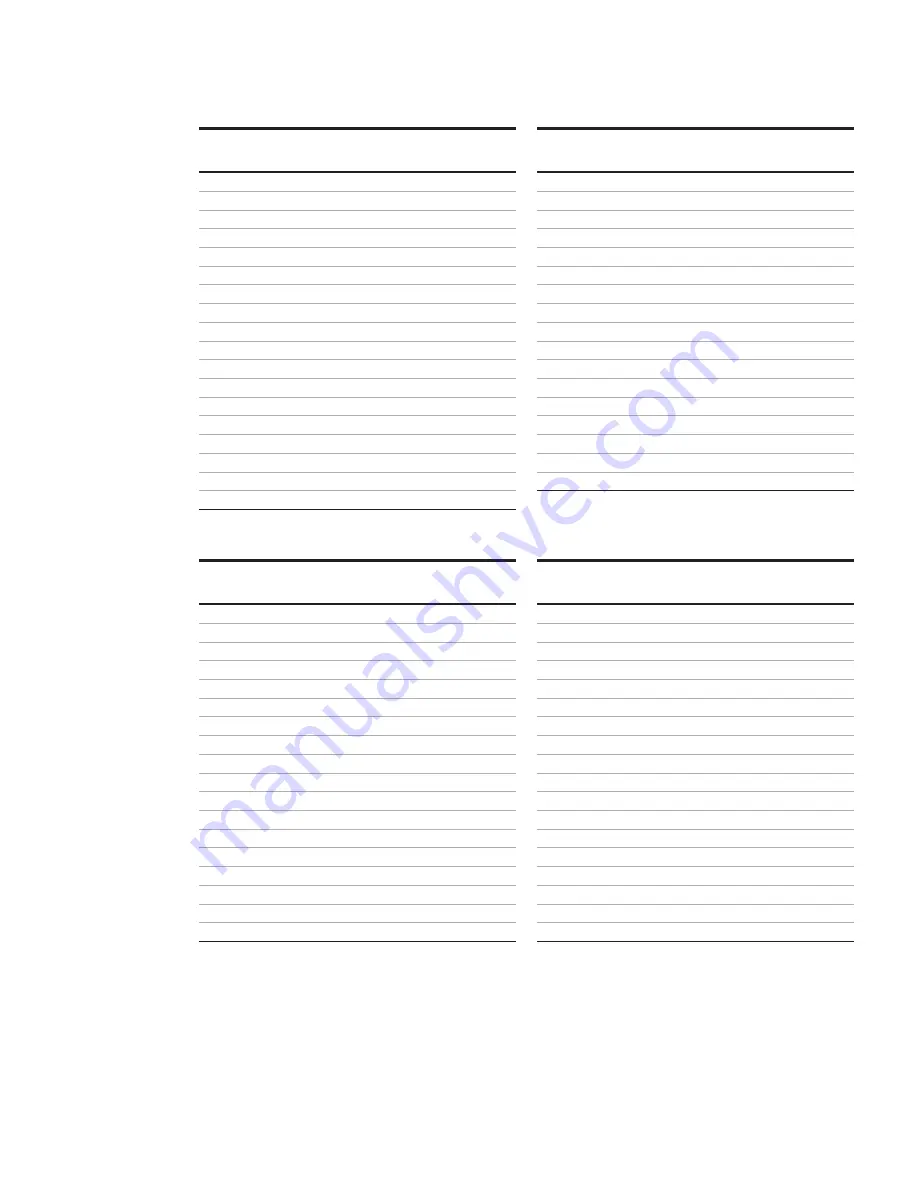
46
E VOLUTI ON S E R I E S E9 0 0 0
M OTO R CO N T R O L C EN T ER
Size 3 (Standard)
Size 1 (Standard and Ambient Comp.)
Size 3 (Ambient Comp.)
Size 3 (Ambient Comp.)
Motor Full-
Load Amps
3-Ph, 3 Heater
Heater
Number
CR123
Maximum
Fuse
Rating
19.0-19.3
F233B
70
19.4-22.1
F243B
80
22.2-23.4
F270B
80
23.5-27.0
F300B
90
27.1-29.1
F327B
100
29.2-31.8
F357B
110¹
31.9-33.9
F395B
125¹
34.0-37.6
F430B
125¹
37.7-41.9
F487B
150¹
42.0-47.7
F567B
175¹
47.8-52.1
F614B
175¹
52.2-55.8
F658B
200¹
55.9-59.7
F719B
200¹
59.8-68.1
F772B
200¹
68.2-71.5
F848B
200¹
71.6-78.2
F914B
200¹
78.3-87.5
F104C
200¹
87.6-90.0
F114C
200¹
Motor Full-
Load Amps
3-Ph, 3 Heater
Heater
Number
CR123
Maximum
Fuse
Rating
27.1-32.2
F357B
110
32.3-34.0
F395B
125
34.1-36.8
F430B
125
36.9-44.6
F487B
150
44.7-48.4
F567B
175
48.5-53.9
F614B
175
54.0-57.4
F658B
200
57.5-60.0
F719B
225¹
60.1-69.5
F772B
225¹
69.6-71.7
F848B
250¹
71.8-79.9
F914B
275¹
80.0-92.3
F104C
300¹
92.4-97.0
F114C
350¹
97.1-108
F118C
400¹
109-118
F133C
400¹
119-131
F149C
400¹
132-135
F161C
400¹
Motor Full-
Load Amps
3-Ph, 3 Heater
Heater
Number
CR123
Maximum
Fuse
Rating
28.8-32.0
F357B
110
32.1-34.2
F395B
125
34.3-36.7
F430B
125
36.8-43.9
F487B
150
44.0-46.6
F567B
175
46.7-52.6
F614B
175
52.7-55.6
F658B
200
55.7-58.7
F719B
225¹
58.8-67.1
F772B
225¹
67.2-70.6
F848B
250¹
70.7-76.3
F914B
275¹
76.4-88.7
F104C
300¹
88.8-93.4
F114C
350¹
93.5-105
F118C
350¹
106-114
F133C
400¹
115-128
F149C
400¹
129-131
F161C
400¹
132-135
F174C
400¹
Motor Full-
Load Amps
3-Ph, 3 Heater
Heater
Number
CR123
Maximum
Fuse
Rating
17.8-18.4
F233B
70
18.5-21.1
F243B
80
21.2-22.1
F270B
80
22.2-26.1
F300B
90
26.2-28.0
F327B
100
28.1-31.3
F357B
110¹
31.4-33.3
F395B
125¹
33.4-34.3
F430B
125¹
34.4-40.9
F487B
150¹
41.0-44.7
F567B
150¹
44.8-51.0
F614B
175¹
51.1-52.0
F658B
200¹
52.1-55.4
F719B
200¹
55.5-63.3
F772B
200¹
63.4-66.1
F848B
200¹
66.2-73.5
F914B
200¹
73.6-82.2
F104C
200¹
82.3-90.0
F114C
200¹