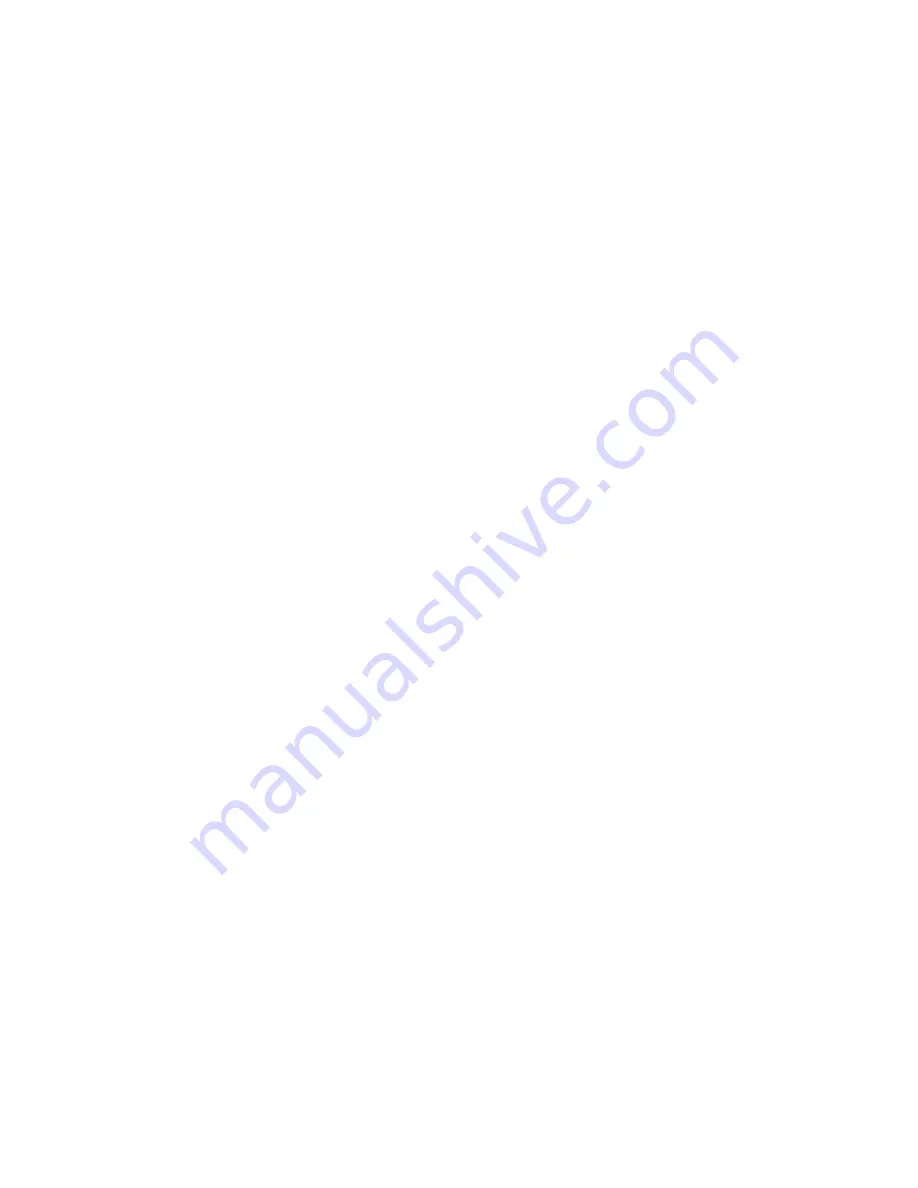
21
TROUBLESHOOTING
Service Error Codes
The electronic controls of the dryer have self diagnos-
tics codes built in that cover most product failures.
When a failure occurs, the dryer stops or pauses.
The control will beep and flash the STATUS lights
to tell the customer that a failure has occurred. To
stop the flashing and beeping, touch the Pause
Cancel button. The error code remains stored in
the control.
To view the error codes:
1. Rotate the cycle select knob to the 3 o’clock posi-
tion.
2. Press and hold the Select and Pause Cancel
buttons simultaneously for (6) seconds.
3. Immediately after, press and hold the START
and Pause Cancel buttons simultaneously for
(4) seconds.
4. Rotate the cycle select knob to the 2 o’clock posi-
tion.
The four indicator lights of Drying, Cool Down, Extra
Care and Clean Lint Filter will flash the number of times
for the first digit of the code after the E, and the START
indicator light will flash the number of times for the second
digit after the E. The code is obtained by counting the
number of times the lights flash. Example E24: the four
indicator lights would flash twice indicating the 2 and the
START indicator light will flash four times indicating the
4. The four indicator lights and the START indicator light
will start flashing at the same time. The control will then
pause for 2 seconds, then repeat the code.
Troubleshoot the problem by using the chart on the next
page.
The error codes remain in memory until cleared from the
control.
To move to the next code, press the OPTIONS
button.
To clear code, press the Select button.
To exit this mode, simultaneously press and hold the
Select and Pause Cancel buttons for (6) seconds.
Note: A letter appearing in the code stands for a
number higher than nine.
A = 10
B = 11
C = 12
D = 13
E = 14
F = 15
Example Code E4A: the first digit would be 4 and the
second digit would be 10. If this code would appear on
a washer, the four indicator lights would blink four
times and the START indicator light would blink ten
times.
Summary of Contents for DSXH47EG
Page 9: ...9 WIRING DIAGRAM FOR ELECTRIC MODELS ...
Page 10: ...10 WIRING DIAGRAM FOR GAS MODELS ...
Page 47: ...47 ...