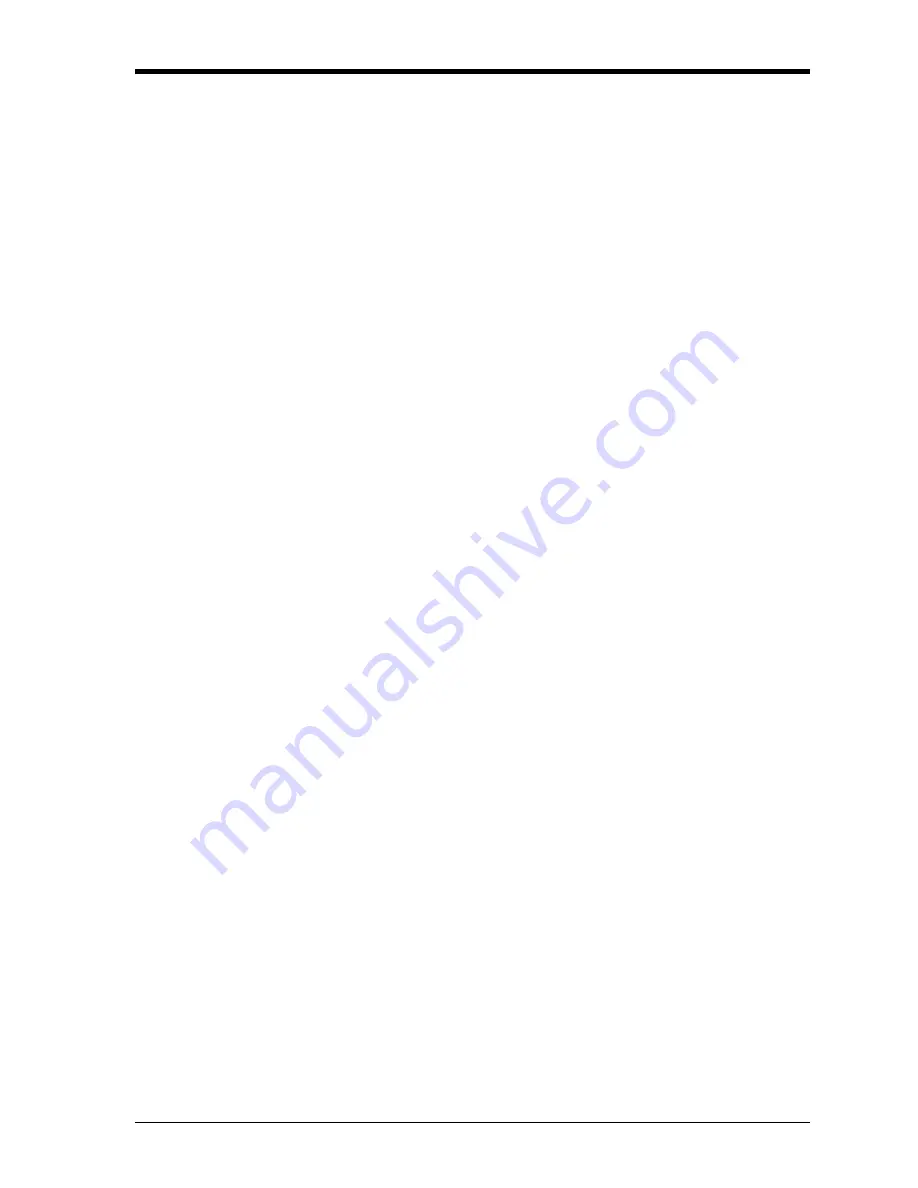
Technical Specifications
6-1
November 2005
MMY30 Specifications
Sensing Element
Planar sensor, aluminum oxide capacitance principle
Measurement Range
- 90°C to +10°C (-130°F to +50°F) dew point temperature.
0 to 10, 0 to 100, 0 to 1000 ppm
v
(fully adjustable with integral
display)
Recommended
Recalibration Cycle
12 months, depending on the application
Calibration Accuracy
±2°C (±3.6°F) dew point at 25°C (77°F)
Maximum Sensor Relative
Humidity
50% at dewpoint temperatures >0°C (32 °F)
Operating and Storage
Temperature
-40°C to +50°C (-40°F to +122°F)
Air Bleed Off at 7 bar (100
psig)
Approximately 28 sl/h (1 SCFH)
Maximum Operating
Pressure
31 bar, 3.1 MPa (450 psig)
Helium Leak-Rate
<10
-6
mbar l/s
Output
4 to 20 mA; 16 µA resolution
Flow Block
316 stainless steel with G ½ thread (DIN ISO 228) or ½” (12.7 mm)
MNPT thread
Wrench Width for Flow
Block
42 mm (1 5/8”)
Electronics
Microcontroller operated
Moisture Unit
Dew point temperature in °C or °F, ppm
v
Power Supply
24 VDC nominal, 12 to 28 VDC range
Protection
Type 4X (IP 67)
Weight
1.5 kg (3.2 lbs)
European Compliance
Complies with EMC Directive 89/336/EEC and PED 97/23/EC for
DN<25
Summary of Contents for DewPro MMY30
Page 1: ...GE Sensing DewPro MMY30 General Eastern Trace Moisture Transmitter User s Manual ...
Page 6: ...Chapter 1 ...
Page 13: ...Chapter 2 ...
Page 19: ...Chapter 3 ...
Page 24: ...Chapter 4 ...
Page 34: ...Chapter 5 ...
Page 35: ...Troubleshooting Problems and Recommended Solutions 5 1 Removing the Filter 5 1 ...
Page 37: ...Chapter 6 ...
Page 41: ...Appendix A ...
Page 42: ...User Interface Matrix Input ...