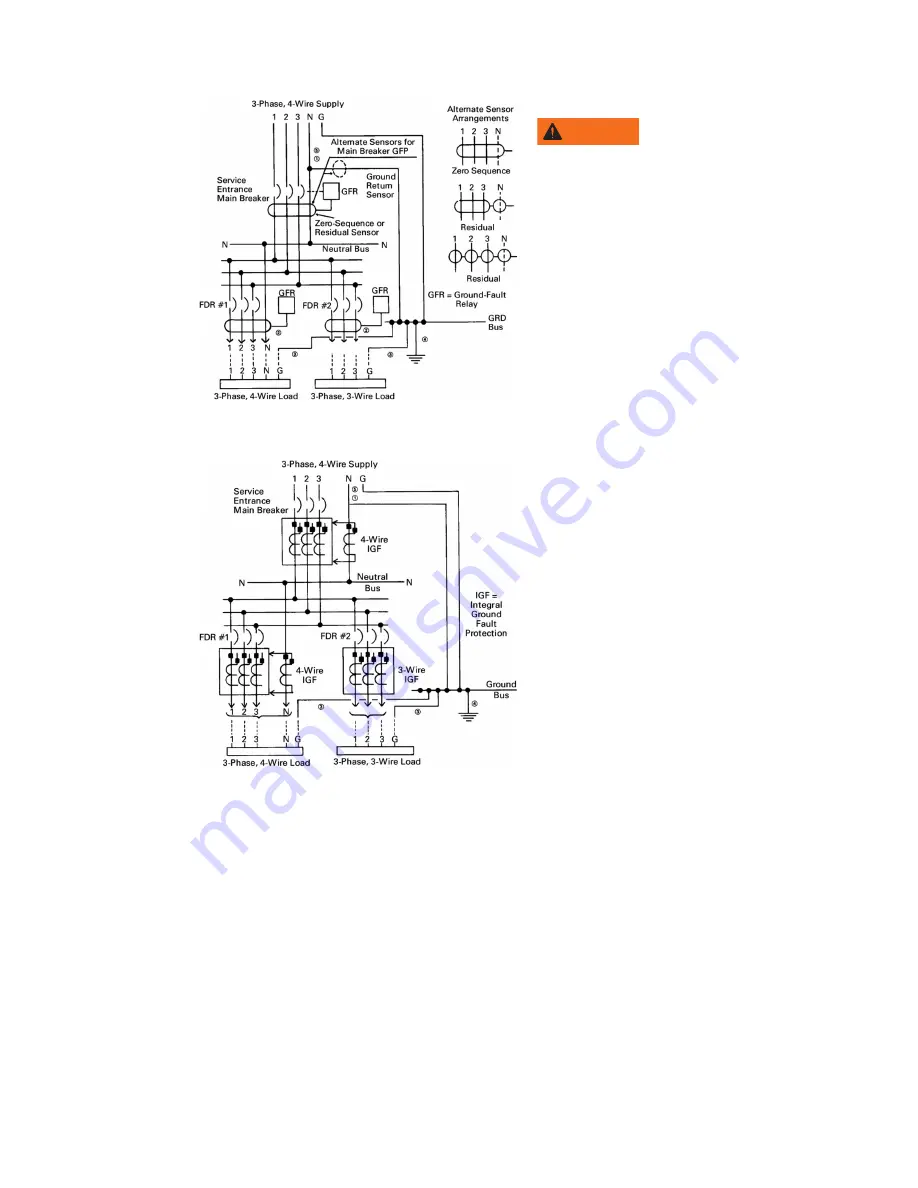
24
R E LI AG E A R® S B
S W I TC H B OA R DS
—
44
—
45
Testing and inspection
DANGER
WARNING
CAUTION
NOTICE
SAFETY
INSTRUCTIONS
Warning:
Keep equipment de-energized during
cleaning and inspection. Failure to do so may
result in serious injury or death.
After the equipment has been installed and
all connections made, test and inspect the
switchboard before energizing. Although the
equipment and devices have been inspected at the
factory, perform a final field test to be certain that
the equipment has been properly installed and that
all connections are correct and have not loosened
during transportation. Check all terminals,
connections, and hardware for correct torque
values. Check all Kirk key interlocking schemes
to ensure desired performance. Make sure the
incoming line is de-energized while all tests are
in progress.
In addition to these mechanical checks, use a
megohmmeter to test the switchboard. Open all
switchoard devices, remove all instrumentation
and control fuses, and isolate the neutral from
ground. All scraps of wire, plaster, dust, and other
foreign material must be removed. Vacuuming is
recommended. Use a megohmmeter developing
500 volts. Conduct electrical insulation resistance
tests from phase to phase, phase to ground, phase
to neutral, and neutral to ground. If any
switchboard tested under the above conditions
shows resistance values less than 1 megohm,
inspect it for possible tracking on insulation or
insulation breakdown. For additional details
consult* ANSI/NEMA PB 2.1.
—
45
Typical single-source
ground-fault protection
using integral
ground-fault trips.
—
44
Typical single-source
ground-fault protection
using ground-fault relays
Summary of Contents for ABB ReliaGear SB
Page 1: ...INSTALLATION OPER ATIONS AND MAINTENANCE MANUAL ReliaGear SB Switchboards ...
Page 2: ......
Page 30: ...30 RELIAGEAR SB SWITCHBOARDS ...
Page 31: ......