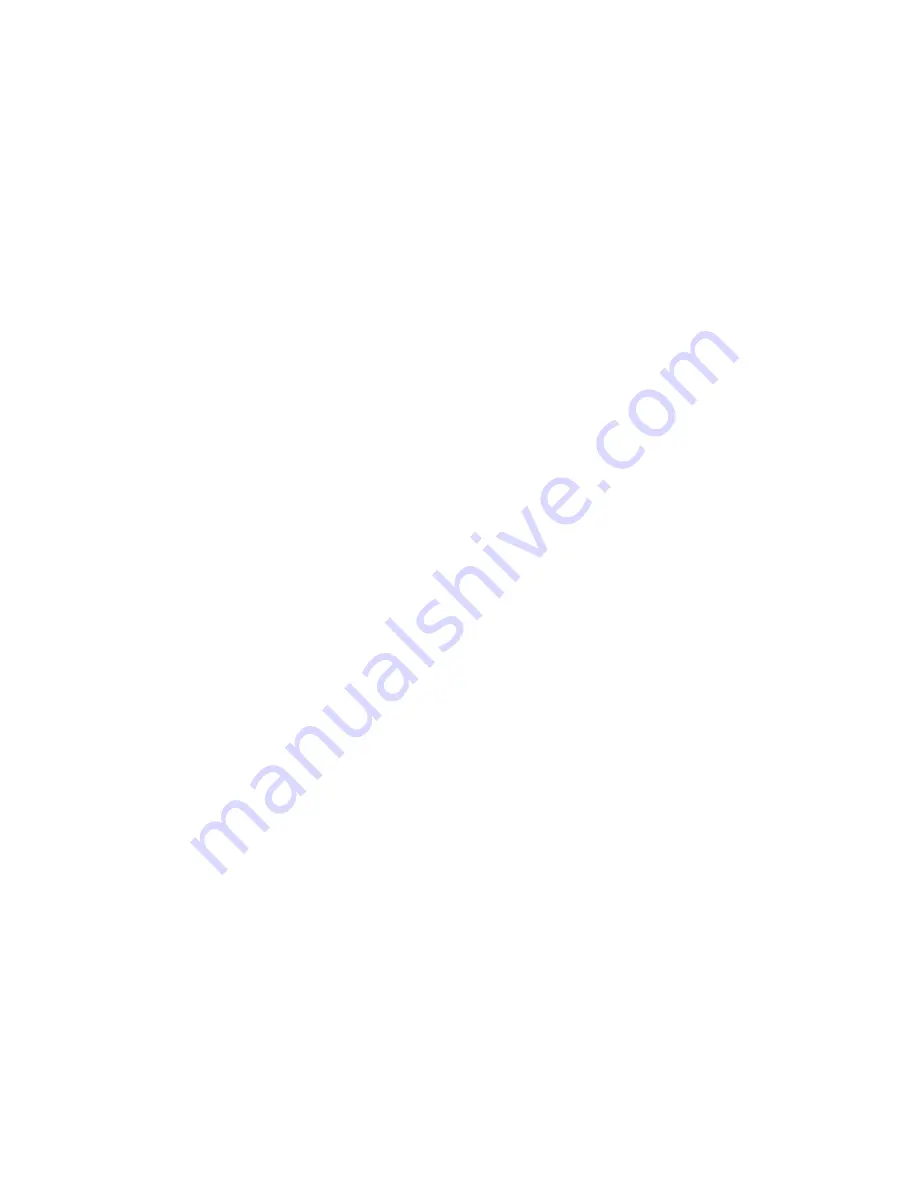
CHAPTER 1: INTRODUCTION
SPECIFICATIONS
350 FEEDER PROTECTION SYSTEM – INSTRUCTION MANUAL
1–21
Communications
SERIAL
RS485 port: ............................................................Opto-coupled
Baud rates:.............................................................up to 115 kbps
Response time:.....................................................1 ms typical
Parity: .......................................................................None, Odd, Even
Protocol: ..................................................................Modbus RTU, DNP 3.0, IEC 60870-5-103
Maximum distance: ...........................................1200 m (4000 feet)
Isolation:..................................................................2 kV
ETHERNET (COPPER)
Modes:......................................................................10/100 MB (auto-detect)
Connector:..............................................................RJ-45
Protocol: ..................................................................Modbus TCP, DNP3.0, IEC 60870-5-104, IEC 61850 GOOSE,
IEC 61850, OPC-UA
ETHERNET (FIBER)
Fiber type: ..............................................................100 MB Multi-mode
Wavelength: ..........................................................1300 nm
Connector:..............................................................MTRJ
Protocol: ..................................................................Modbus TCP, DNP3.0, IEC 60870-5-104, IEC 61850 GOOSE,
IEC 61850, OPC-UA, PRP, HSR
Transmit power:...................................................-20 dBm
Receiver sensitivity: ...........................................-31 dBm
Power budget: ......................................................9 dB
Maximum input power:....................................-11.8 dBm
Typical distance:..................................................2 km (1.25 miles)
Duplex: .....................................................................half/full
Maximum number of TCP/IP sessions: .....3
Product type: ........................................................Class 1 Laser product
USB
Standard specification: ....................................Compliant with USB 2.0
Data transfer rate:..............................................115 kbps
OPC-UA (OLE FOR PROCESS CONTROL - UNIFIED ARCHITECTURE)
DA Server:...............................................................Transmission of real-time data to Clients
A&E Server: ............................................................Transmission of Event information to Clients. Acknowledge
and confirmation permitted from Client side