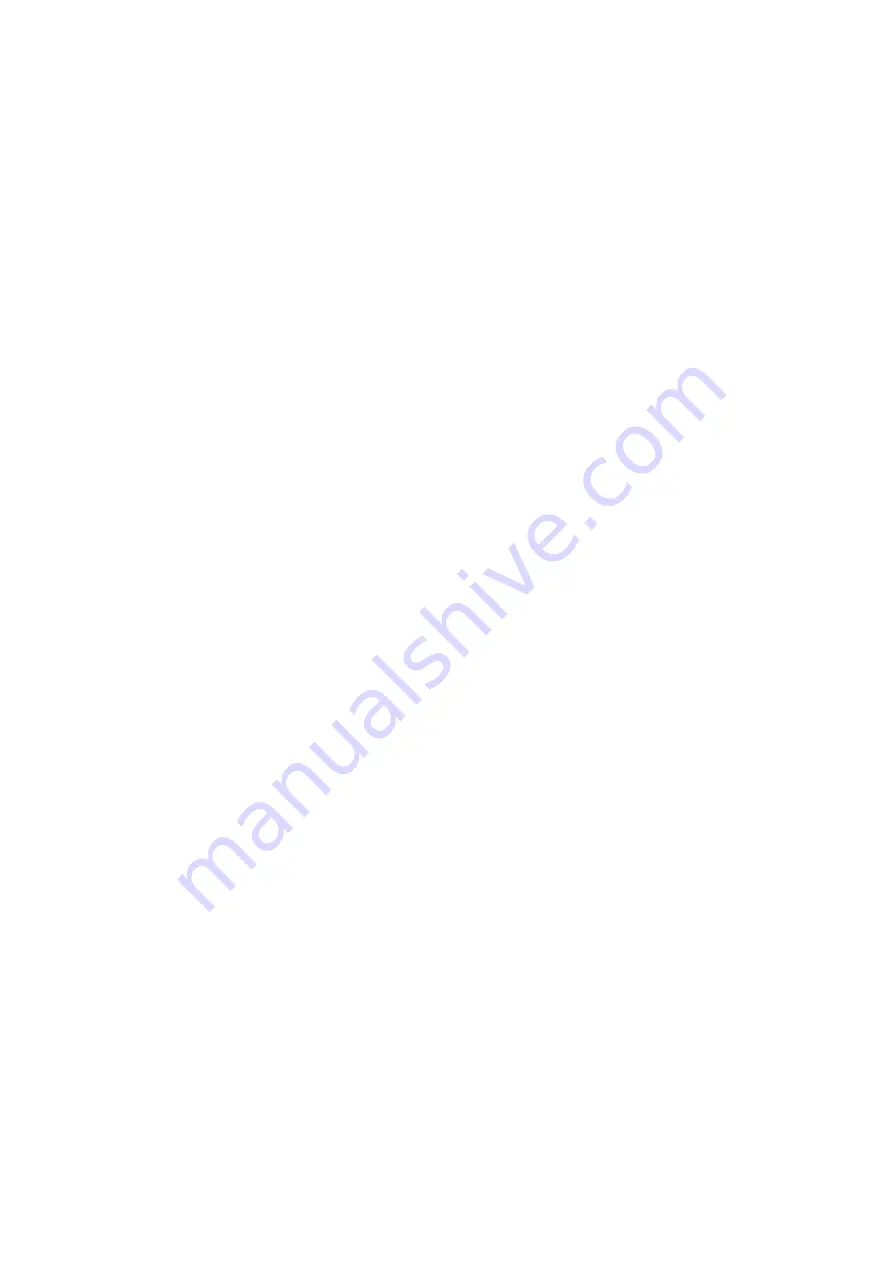
11. Press T to adjust the 20mA output by measuring the mV across TP8 and TP9. Press H or L to adjust and then press
SPACE to set and exit.
12. Before using span gas, ensure that an autozero is not about to take place. This is indicated by the MPU LED
flashing at 1 Hz. The MPU LED on the PCB will flash normally at 1 Hz but when there is less than 30 seconds to an
autozero flash rate will increase to 2Hz i.e faster flash.
13. Apply a test gas to the sensor (typical - 100ppm Isobutylene) for 1 minute at a flow rate of 1 litre/min. Use the
UP and DOWN buttons on the PCB to give correct 4-20mA level. (ie. 5.6mA for 100ppm). Remove gas and wait
5 minutes. If a maximum range gas is available, apply for 1 minute and note the value of A. This can then be
entered via Hyperterminal using the M command giving better accuracy across the range. Remove gas and wait 2
minutes.
14. Connect the sensor to a Combi alarm panel and ensure that it reports in correctly.
Note:
Fit the end of line (EOL) link J1 if the sensor is to be installed at the end of the sensor cable.
15. If a display board is fitted via connector J5 and U12 adjust VR1 for LCD contrast.
16. Remove J9 test link for normal operation.
17. Ensure J29 address link is removed (this is only used when changing address from a panel)
Manual calibration (without PC or LCD)
18. Zero - with no gas applied, measure between Ag and Sig (Y) and adjust VR2 to give 50mv.
With J9 test link inserted, check the 4-20mA output to be 4mA as measured at TP8 to TP9 = 4mV
19. Span - apply test gas (typical 50% of range) and use UP and DOWN buttons on the PCB to give correct 4-20mA
output. (50% gas = 12mA).
20. Remove gas and ensure the output returns to the 4mA level and then remove the J9 test link
Setup using magnets - LCD
WIN versions of the sensor have an LCD display which shows the Gas and range together with the sensor address and
a display of the number of seconds until an autozero will occur.
Also incorporated are 3 reed switches which can be activated using external magnets through the glass window of the
flameproof XDIwin enclosure. These magnets do not act instantly and have to be in close proximity to L, M and R on the
front display for a few seconds to activate a software setup function.
The right magnet allows the CAN address of the sensor to be changed. When the address menu is displayed with a
prompt to remove the magnet, and then the display shows the address and that the right magnet will decreases it whilst
the left magnet will increase it. This is then stored in internal non-volatile memory and the display will automatically
revert to normal operation.
The centre magnet is used to inhibit the sensor. As with the left and right magnet functions the display requests that you
remove the magnet and then the state of inhibit appears on the LCD.
The left magnet then puts the sensor into inhibit whilst the right magnet removes it. The amber LED on the front panel
under the LCD flashes when the sensor is inhibited. When all magnets are removed, the display will revert to normal
operation. The direction of the alarms is displayed as ^ for rising and v for falling but these can be changed using left
and right magnets together.
The left and right magnets together allow the calibration menu to be used. Removing both magnets as instructed on
the LCD presents the first part of this multi menu which is ZERO. With no gas present the display shows the PPM value
but also typically [0.02] This number between the square brackets shows how close the autozero has achieved. [0.00] is
definite zero and the PCB led D1 will be flickering orange.
A 15 second timer is displayed and is reset back each time a magnet is near. Waiting till timeout is acceptable but this
timeout can be speeded up by placing a magnet near to the centre position.
SPAN is the next part of the menu and gas should be applied to the sensor at this time (recommended - 100ppm
Isobutylene - see GDS application notes C645). A 2 minute counter is displayed before the next part of menu is
activated. The left magnet now increases the PPM reading and the right magnet reduces.