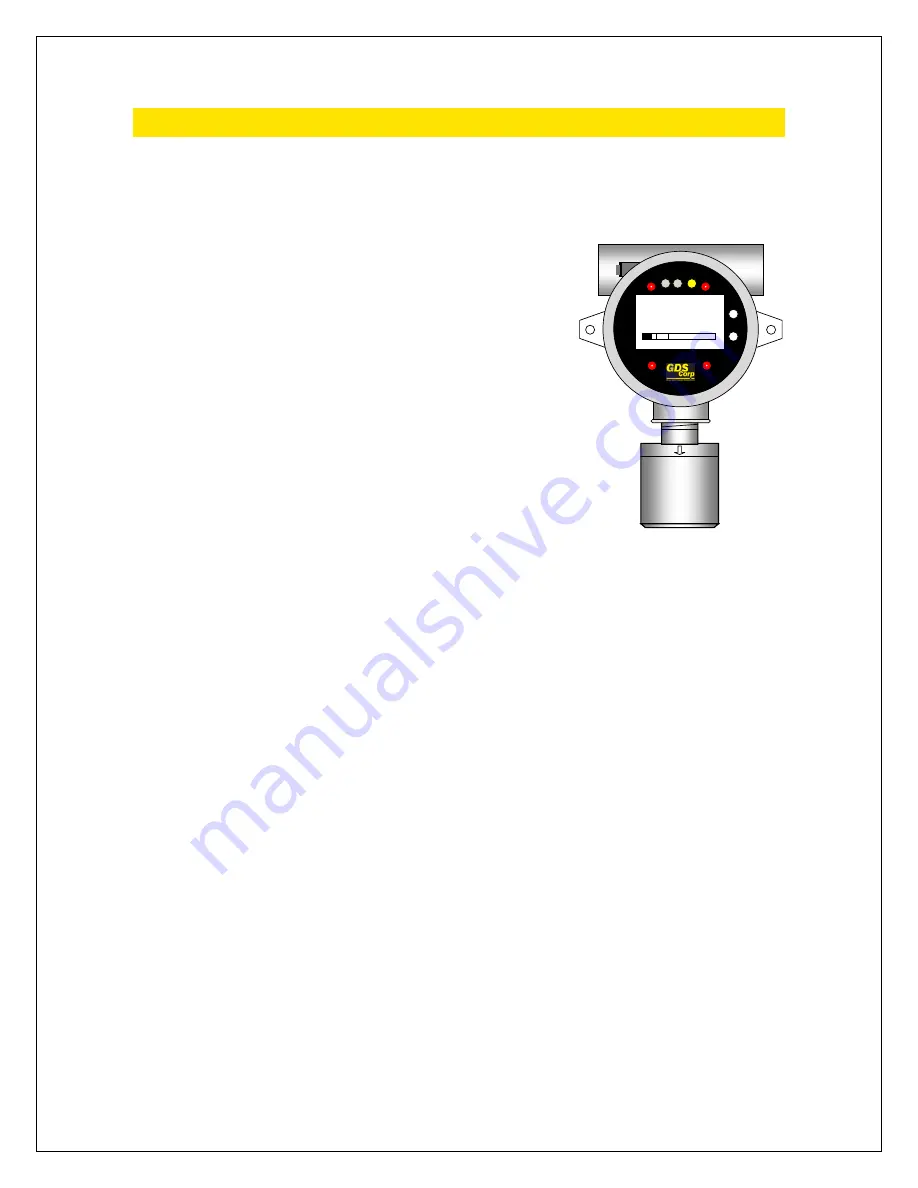
GASMAX II Operation & Maintenance Manual, Revision 7.0
Page 7
2
OVERVIEW
The GASMAX II is a single or dual channel fixed-point gas monitor designed to provide continuous
monitoring of toxic or combustible gases in hazardous areas. Gas values are displayed in calibrated
engineering units as well as bar graph or 30-minute trend graph format.
The GASMAX II supports one or two local or remote sensors for toxic
or combustible gases. The advanced microcontroller, non-intrusive
magnetic interface and superior graphic LCD interface offers rapid
setup, simplified operation and enhanced diagnostics not found in
previous generation products. On-board non-volatile memory retains
all configuration data during power interruptions. Two independent
4-20 mA outputs allow for easy connection to control systems or
other alarm instrumentation. Additional output options include alarm
relays and single or dual channel MODBUS slave interfaces.
Built-in user-prompted calibration makes it easy for one person to
perform calibration and maintenance without opening the enclosure
or declassifying the area. A battery-powered real-time clock and
event log allows the GASMAX II to track calibration and alarm events
for later recall on the LCD readout.
GASMAX II SENSORS
The GASMAX II supports a number of different sensors that fall into two categories
–
“toxic” and “bridge”.
Toxic sensors use an electrochemical process to detect gas and are often referred to as “echem” sensors.
Examples include oxygen, hydrogen sulfide and mercaptan. Toxic sensors require no excitation voltage
and
–
when operating properly
–
generate zero output when no gas is present.
Bridge sensors require an excitation voltage to operate and generate an output signal that is biased at
approximately ½ of the input and varies by a small amount proportional to the amount of gas present.
These sensors require both a VOLTAGE adjustment and a BALANCE adjustment and include catalytic
beads, SmartIR infrared sensors and PID photoionization detectors.
In the standard configuration, Channel 1 is configured to accept a toxic sensor and Channel 2 is configured
for a bridge sensor. Channel 2 can also be modified to support an industry standard 4-20mA input.
IMPORTANT
: TOXIC SENSORS MAY FAIL TO OPERATE PROPERLY IF POWER IS NOT APPLIED WITHIN 6
MONTHS OF SHIPMENT. CONTACT GDS CORP FOR RECOMMENDATIONS IF THIS SITUATION MAY OCCUR.
M E A S U R E M E N T N A M E
12
% L E L
P
T
IT
T
I