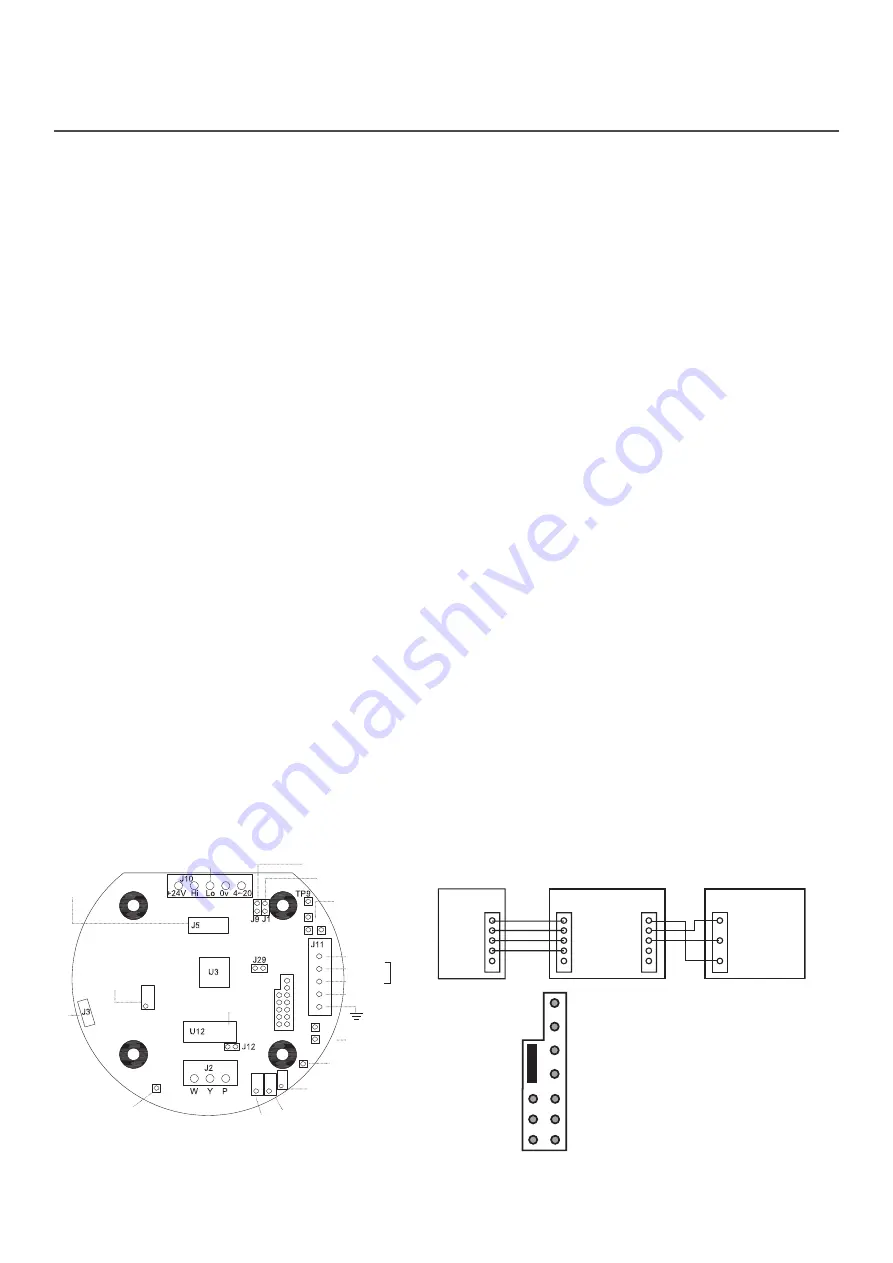
22
Fig. 11
XDI–XDIwin – 15/30J
4~20mA INPUT
Set up procedure: 204D2C Issue Tv3
Technical Sheet
ref C1180
NEW UNITS ARE SUPPLIED READY TO CONNECT TO A SYSTEM. THE FOLLOWING PROCEDURE MAY NEED TO BE CARRIED OUT
FOLLOWING CHANGES TO THE SYSTEM:
1. Insert J8 jumper to receive signal from external 4~20mA source (Fig.3)
2. Connect external 4~20mA source to the 4~20mA input terminal (J11) on the right hand side of the board.
3. Connect terminal J10 as shown in Fig.2
4. Connect DVM (mV range) across TP7 + TP15 to measure current supplied by 4~20mA device (mV = mA)
5. Ensure that the CAN LED is ON and flashing occasionally.
6. Connect RS232 pod to connector J3 and to a PC running HyperTerminal at 4800 baud.
7. The HyperTerminal display shows a continuous data output and allows input from the PC keyboard.
a. Press C to enter calibration mode
b. Press shift $ to initialise the memory if new PCB (defaults to Flam %LEL)
c. Press G to change gas/signal to the type required for the cell/unit in use. (NOTE: When using a ‘user gas’ press ‘E’ to edit name after
using ‘G’ to select. Also make sure to select a vacant user gas number, 61–68, as the addressable sensor will overwrite data entered
at the Combi panel.
d. The range of the gas/signal selected will have a default setting which can be changed by pressing ‘R’
e. Press A and enter CAN address of this sensor
f. Press N to toggle the number of decimal places between 1 and 2 (i.e. dp=1 or dp=2)
g. Press B to toggle the deadband ON and OFF
h. Press F to toggle the external fault option ON or OFF (only available when external source has local fault indication)
i. With input signal reading 4mA press Z to zero the reading.
j. Press S to span the reading. Apply gas / signal from external source and press H or L to adjust the reading.
k. Press space to exit the span.
l. Press X to exit the calibration mode.
8. Connect to a combi panel and ensure that the sensor reports in correctly.
Note:
that if this sensor is at the end of the communication
wires then it will need terminating by inserting jumper J1(EOL). The continuous data output when connected to HyperTerminal is the same
format as for the Flammable sensor. The software used is identical.
Fig.1
Fig.2
Fig.3
A
EOL
CAN
4-20
MPU
FAULT
TP1
OV
TP11
TP9
TP5
TP8
TP10
198M1C
ISS M
TP
7
ZERO
ZERO
TP12
DISP
MPU active LED
(Flashing)
Fault LED
Sens V Test Point
TP7 + TP12
Sensor cell input
Sensor Volts
(RV3)
Zero
(RV2)
Span
(RV1)
4mA
(RV4)
Sensor Zeroing LEDs
CAN Transmitting LED
4-20mA SInk/Source
4-20mA Test
Jumper
End-of-line Jumper
Relay/Win Ribbon
LCD Contrast
Win Only
RS232
PC Data In/Out
Win Data Ribbon Cable
4-20op Test Points
FIELD TERMINALS
HI LO
24V Can+ Can- OV 4-20mA
24V Hi
Lo OV 4-20
mA
P
Y
W
Control Unit
CAN 1 or 2
Sensor
Addressable
+24
Hi
Lo
0v
4~20mA
+24
Hi
Lo
0v
Control Unit
4~20mA Input
Sensor
3-Wire Direct
4~20mA Signal
+24
Hi
Lo
0v
4~20mA
+24
Sig
0v
EOL
T
FAULT
MPU
SK
SE
204M1C
ISS M
CONTRAST
Fault LED
Gas Type Header
Sensor cell input
20mA
Span
(RV2)
4mA
Zero
(RV1)
Sensor 4-20mA Routing Configurations
(see diagram)
CAN Transmitting LED
4-20mA Test
Jumper
Relay/Win Ribbon
LCD Contrast
Win Only
End-of-line Jumper
+24V Test Point
(w.r.t 0V)
+24V
RS232
PC Data In/Out
Win Data Ribbon Cable
4-20mA Test Pins
4-20mA Sink Source
External 4-20mA Input
(eg. Infrared)
+24V O/Pt
(eg. Infrared)
FIELD TERMINALS
HI LO
24V Can+ Can- OV 4-20mA
24V Hi
Lo OV 4-20
mA
P
Y
W
Mainboad to Sensor wiring
Sensor Jumper configuration
Control Unit
CAN 1 or 2
Sensor
Addressable
+24
Hi
Lo
0v
4~20mA
4~20 IN
SO
SK
+24
Hi
Lo
0v
Control Unit
4~20mA Input
Sensor
3-Wire Direct
4~20mA Signal
+24
Hi
Lo
0v
4~20mA
+24
Sig
0v
Control Unit
4~20mA Input
Sensor
2-Wire Direct
4~20mA Signal
+24
Hi
Lo
0v
4~20mA
+24
Sig
0v
Control Unit
CAN 1 or 2
Sensor
Addressable 4~20mA Input
+24
Hi
Lo
0v
4~20mA
+24
Hi
Lo
0v
4~20 IN
SO
SK
4~20 IN
SO
SK
4~20 IN
SO
SK
ange
t magnets
Command
Use
A = Set CAN address
Sets the CAN address
G = Select gas type
Select the gas type from a list
Z = Zero
Press when no gas on sensor to give zero
S = Span
Use when calibration gas applied,
H and L change reading
D = Enter calibration date
Enter the calibration date
Y = Toggle auto zero
Auto zero is ON or OFF, small drift is cleared
H = Set high alarm
Sets the high alarm threshold
L = Set low alarm
Sets the low alarm threshold
O = Set over range alarm
Sets the over range alarm threshold
P = List command
List these commands on screen
X = Exit calibration mode
Exit this PC mode
$ = Initialise this sensor
Use on new PCB to set gas type to Flam
U = Alarm direction
Sets rising or falling alarms
R = Range
Allows a change in maximum value
N = Decimal points
Toggles between 1 and 2 decimal places
E = Edit user gas text
Choose gas description
B = Toggle deadband
Deadband of 2.5% can be on or off
F = Toggle fault Input
External fault input contact can be disabled
# = Normally energised
Low /high alarm relays and fault relay can be
made normally energised
V= View gas log
From current log, display how many historical
readings to display, up to 2880
% = Clear gas log
Set all 2880 log readings to 0.00
I = Log interval
Choose how many seconds between each log
reading and whether the log will roll over or
stop at 2880 (60 second interval and 2880
readings = 48 hours)
EOL
CAN
4-20
MPU
FAULT
TP1
OV
TP11
TP9
TP5
TP8
TP10
198M1C
ISS M
TP
7
ZERO
ZERO
TP12
DISP
MPU active LED
(Flashing)
Fault LED
Sens V Test Point
TP7 + TP12
Sensor cell input
Sensor Volts
(RV3)
Zero
(RV2)
Span
(RV1)
4mA
(RV4)
Sensor Zeroing LEDs
CAN Transmitting LED
4-20mA SInk/Source
4-20mA Test
Jumper
End-of-line Jumper
Relay/Win Ribbon
LCD Contrast
Win Only
RS232
PC Data In/Out
Win Data Ribbon Cable
4-20op Test Points
FIELD TERMINALS
HI LO
24V Can+ Can- OV 4-20mA
24V Hi
Lo OV 4-20
mA
P
Y
W
Control Unit
CAN 1 or 2
Sensor
Addressable
+24
Hi
Lo
0v
4~20mA
+24
Hi
Lo
0v
Control Unit
4~20mA Input
Sensor
3-Wire Direct
4~20mA Signal
+24
Hi
Lo
0v
4~20mA
+24
Sig
0v
EOL
T
FAULT
MPU
SK
SE
204M1C
ISS M
CONTRAST
Fault LED
Gas Type Header
Sensor cell input
20mA
Span
(RV2)
4mA
Zero
(RV1)
Sensor 4-20mA Routing Configurations
(see diagram)
CAN Transmitting LED
4-20mA Test
Jumper
Relay/Win Ribbon
LCD Contrast
Win Only
End-of-line Jumper
+24V Test Point
(w.r.t 0V)
+24V
RS232
PC Data In/Out
Win Data Ribbon Cable
4-20mA Test Pins
4-20mA Sink Source
External 4-20mA Input
(eg. Infrared)
+24V O/Pt
(eg. Infrared)
FIELD TERMINALS
HI LO
24V Can+ Can- OV 4-20mA
24V Hi
Lo OV 4-20
mA
P
Y
W
Mainboad to Sensor wiring
Sensor Jumper configuration
Control Unit
CAN 1 or 2
Sensor
Addressable
+24
Hi
Lo
0v
4~20mA
4~20 IN
SO
SK
+24
Hi
Lo
0v
Control Unit
Addressable Sensor PCB
J10
+24V
Hi
Lo
0v
4~20mA
4~20mA O/P Sensor
4~20mA
+24V
0v
+24V
0v
Sig
+24V
Hi
Lo
0v
J11
Control Unit
4~20mA Input
Sensor
3-Wire Direct
4~20mA Signal
+24
Hi
Lo
0v
4~20mA
+24
Sig
0v
Control Unit
4~20mA Input
Sensor
2-Wire Direct
4~20mA Signal
+24
Hi
Lo
0v
4~20mA
+24
Sig
0v
4~20 IN
SO
SK
4~20 IN
SO
SK
204
Toxic
TP8
TP15
TP7
Display
Contrast
Test
Addressable
Test Pins (mV)
Add
Vo
Direct test
pins (mV)
4~20mA In (mV)
TP2
TP1
A
20mA
4mA
AG
Offset
Sensor
Comms
Port
EOL
Field terminals
Relay PCB
Connector
Display PCB
Connector
4~20mA
24v DC
OV
FLT
IN
OUT
IN
Summary of Contents for 404+ Series
Page 23: ......