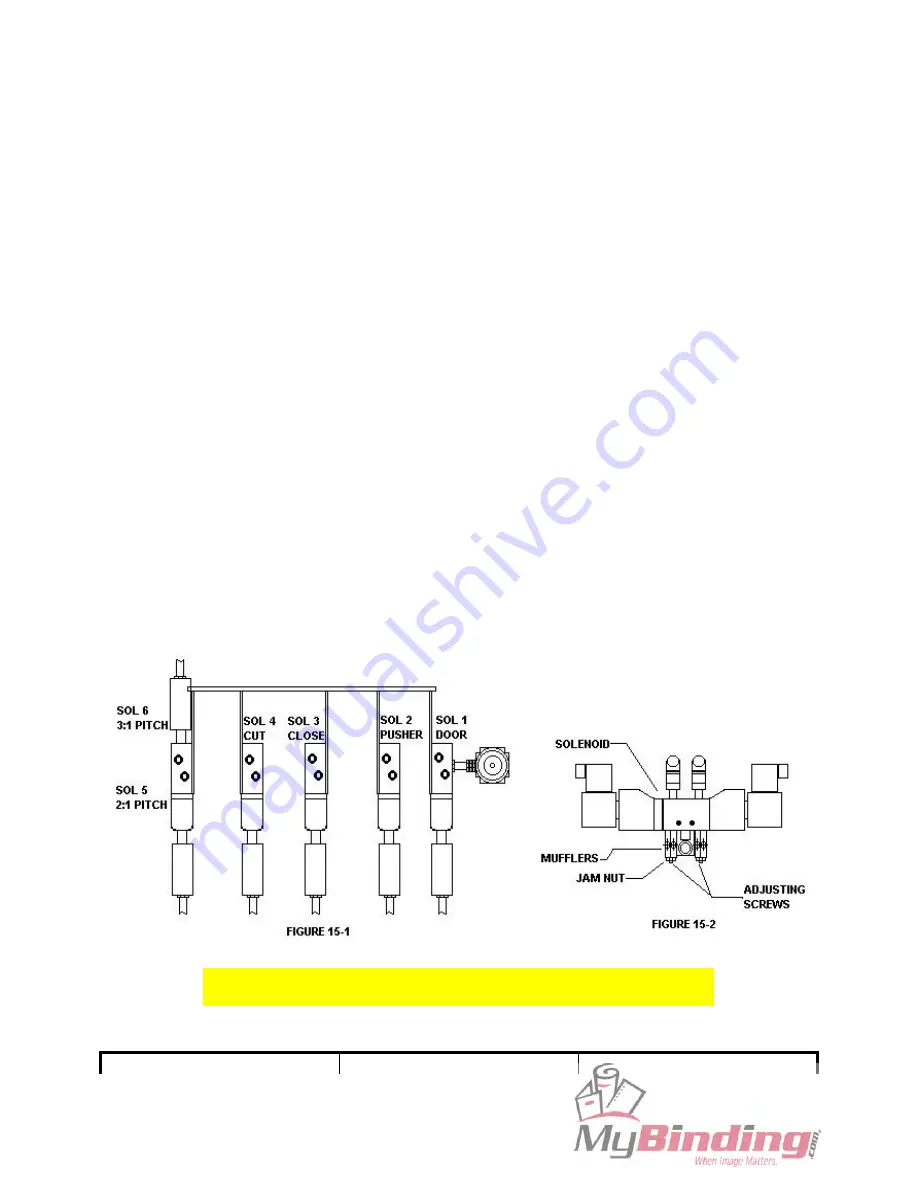
31
To get to the solenoids to either replace or adjust, the rear panel must be removed. Once the panel is
removed, the air solenoids will be before you, working left to right.
Solenoid # 1
Guard Solenoid
is responsible for opening for opening and closing guard doors to
allow entrance and exit of books into the closing area .
Solenoid # 2
Pusher
is responsible for the transporting the book from loading station to closing area
and to the conveyor.
Solenoid # 3
Closing Head Solenoid
is responsible for the actuation of the closing ram.
Solenoid # 4
Cutter Solenoid
is responsible for the actuation of the element cutting knife.
Solenoid #5&6
Feed Sprocket Selection
is responsible for the selection of 2:1 to 3:1 feed sprocket.
Solenoid #5 for 2:1, solenoid #6 for 3:1. This solenoid is different from solenoid #1
through 4 because it is a dual circuit solenoid to prevent crushing of the element on
power down.
Controlling actuation speed adjusts consist of regulating air being discharged through adjusting screws
on the exhaust mufflers (see figure 15-2). To slow down actuation, loosen jam nut on muffler and screw
in setscrew. To speed up action, back setscrew out. Once desired actuation speed has been achieved,
tighten jam nut.
16. Trouble Shooting Guide