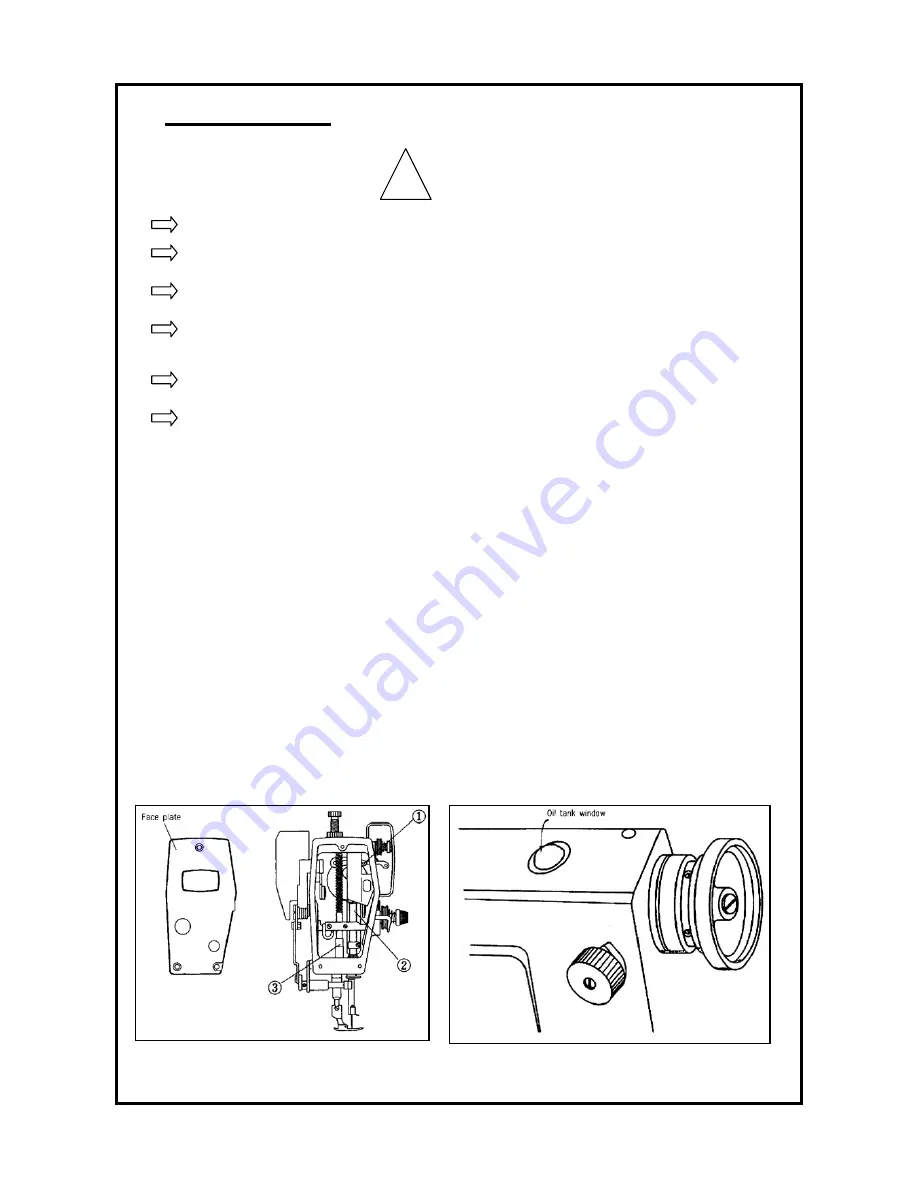
ANITA ©
6
3) INSTALLATION
Warning
The machine must be installed by a trained technician only.
Any electical wiring must be performed by a qualified technician or agent.
The machines weigh over 33 kg. As such, two or more people should carry out the installation.
Plug in only after the installation is complete. If the operator mistakenly steps down on the
pedal with the plug in, the machine will start automatically and can cause physical injuries.
Connect the ground (earth) wire.
An unstable connection may result in an electric shock or a malfunction.
Use both hands when bending the machine backward or returning it to the normal position.
Using only one hand can lead to physical injuries due to the weight of the machine.
3.1) Before Use
A:
Motor must not be switched on while the pedal is in pressure
B:
When you finish operation, always turn off the main switch
C:
During any adjustment, repair or needle xchange make sure that the machine is turned off
D:
Make sure that ground connection is properly installed
E:
Dont use too many connections on one source
F:
Keep safety distance from sources of noise
G:
Before manipulation with motor, wait several minutes after being switched off
H:
If system error is detected, indentify type of error, remove it and then switch on the machine
I:
Check carefully proper connection of all connectors and cables
J:
Check tension of V-belt according to instructions
K:
During installation of new machine or machine which has not been used for long time, apply
repeatedly oil on indicated places of thread take up lever, presser bar and needle bar (Fig 0)
L:
Keep machine going for about 10 minutes at speed 3.000 spm to test it, checking the oil level
M:
After initial testing of the machine, set the speed lower than 3.000 spm for the first 4-5 days.
(Fig. 0)
!
Summary of Contents for GF-1117 Series
Page 30: ...ANITA 30 ...