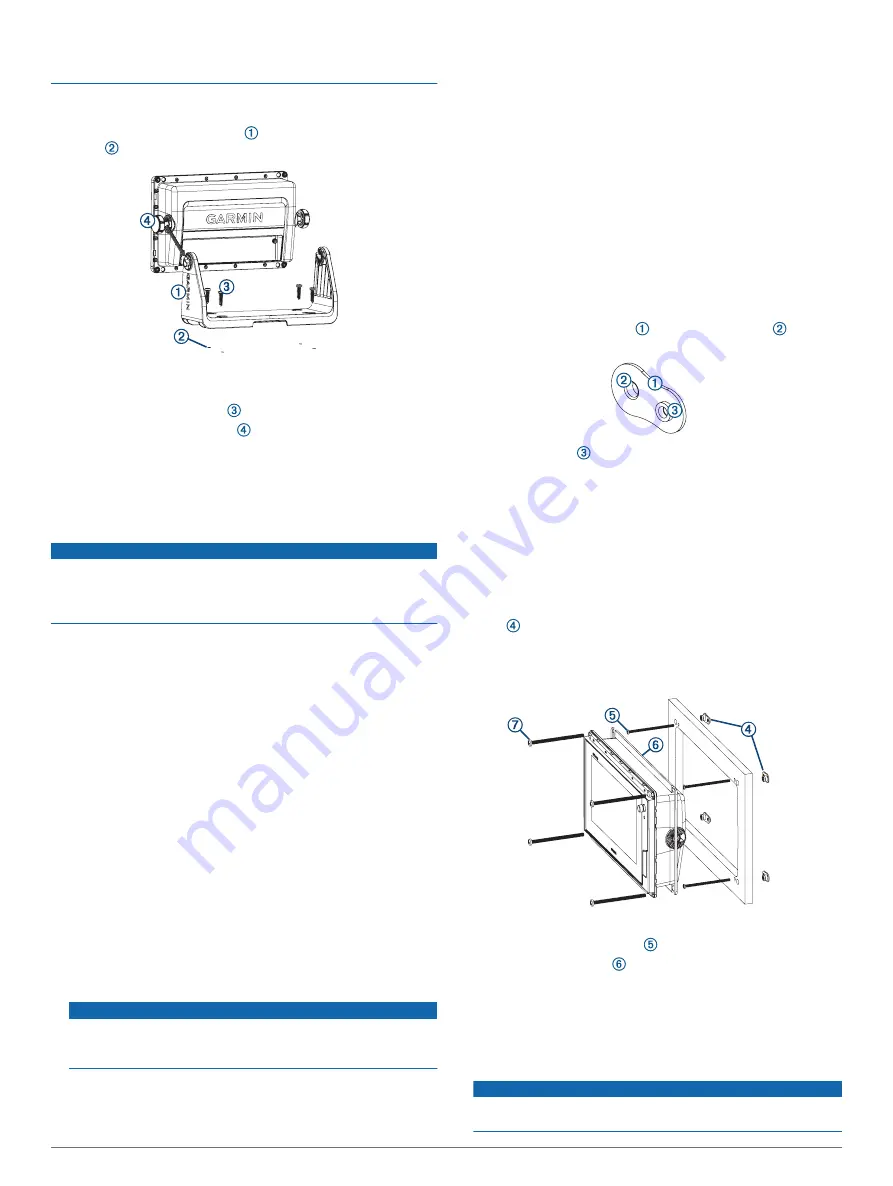
avoid cracking in the gel-coat layer when the screws are
tightened.
You can use the included bracket to bail mount the device on a
flat surface.
1
Using the bail-mount bracket as a template, mark the pilot
holes .
2
Using a 3.2 mm (
1
/
8
in.) drill bit, drill the pilot holes.
3
Secure the bail-mount bracket to the surface using the
included M4 wood screws .
4
Install the bail-mount knobs on the sides of the device.
5
Place the device in the bail-mount bracket, and tighten the
bail-mount knobs.
6
Install the trim caps by snapping them in place around the
edges of the device.
Flush Mounting the Device
NOTICE
Be careful when cutting the hole to flush mount the device.
There is only a small amount of clearance between the case and
the mounting holes, and cutting the hole too large could
compromise the stability of the device after it is mounted.
The included template and hardware can be used to flush mount
the device in your dashboard. There are three options for
hardware based on the mounting surface material.
• You can drill pilot holes and use the included wood screws.
• You can drill holes and use the included nut plates and
machine screws. The nut plates can add stability to a thinner
surface.
• You can punch and tap holes, and use the included machine
screws.
1
Trim the template, and make sure it fits in the location where
you want to mount the device.
2
Secure the template to the mounting location.
3
Using a 13 mm (
1
/
2
in.) drill bit, drill one or more of the holes
inside the corners of the solid line on the template to prepare
the mounting surface for cutting.
4
Using a jigsaw or a rotary tool, cut the mounting surface
along the inside line on the template.
5
Place the device in the cutout to test the fit.
6
If necessary, use a file and sandpaper to refine the size of
the cutout.
7
If necessary, remove the trim caps.
NOTICE
Use a plastic pry tool when possible. Using a metal pry tool,
such as a screwdriver, can damage the trim caps and the
device.
8
After the device fits correctly in the cutout, ensure the
mounting holes on the device line up with the larger holes on
the template.
9
If the mounting holes on the device do not line up, mark the
new hole locations.
10
Based on your mounting surface and model, drill or punch
and tap the larger holes:
• For the included wood screws on 702 models, drill 2 mm
(
5
/
64
in.) holes, and skip to step 18.
• For the included wood screws on 902 models, drill 3.2 mm
(
1
/
8
in.) holes, and skip to step 18.
• For the included nut plate and machine screws, drill 6 mm
(
1
/
4
in.) holes in the larger hole locations.
• For the included machine screws without the nut plate on
702 models, punch and tap M3.5 holes, and skip to step
18.
• For the included machine screws without the nut plate on
902 models, punch and tap M4 holes, and skip to step 18.
11
If you are using a nut plate, starting in one corner of the
template, place a nut plate over the larger hole drilled in
the previous step.
The smaller hole on the nut plate should line up with the
smaller hole on the template.
12
If the smaller hole on the nut plate does not line up with the
smaller hole on the template, mark the new hole location.
13
If you are using a nut plate, drill a 4 mm (
3
/
16
in.) hole in the
smaller hole location.
14
Repeat to verify placement of the remaining nut plates and
holes on the template.
15
Remove the template from the mounting surface.
16
Starting in one corner of the mounting location, place a nut
plate on the back of the mounting surface, lining up the
large and small holes.
The raised portion of the nut plate should fit into the larger
hole.
17
Secure the nut plates to the mounting surface by fastening
the smaller machine screws through the smaller holes.
18
Install the foam gasket on the back of the device.
The pieces of the foam gasket have adhesive on the back.
Make sure you remove the protective liner before installing
them on the device.
19
If you will not have access to the back of the device after you
mount it, connect all necessary cables to the device before
placing it into the cutout.
NOTICE
To prevent corrosion of the metal contacts, cover unused
connectors with the attached weather caps.
2