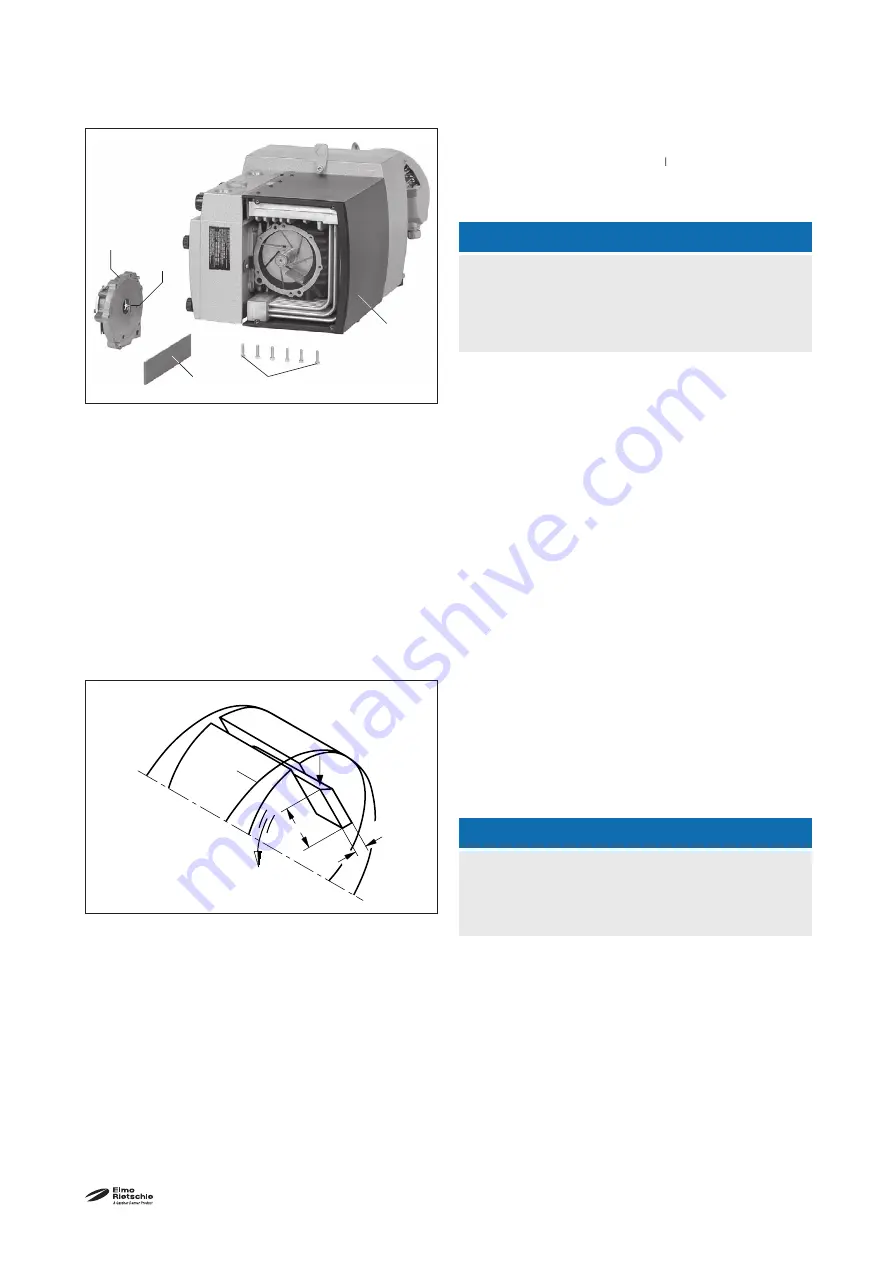
21
www.gd-elmorietschle.com
© Gardner Denver Schopfheim GmbH, Gardner Denver Deutschland GmbH
|
Z
Y
X
O
1
W
Maintenance and repair
s
d
G
1
b
c
Changing blades:
If the minimum height or the minimum thickness has
already been reached or if the blades have fallen
below these levels the whole blade set must be
changed.
NOTICE
Do not undo the
slotted nuts
(Fig. 4/w
1
) on the
housing lid (Fig. 5/b). Only the screws (Fig. 4/s) need
to be removed to change the blades.
Blow out the housing and rotor slot. Insert the
blades into the rotor slot. BWhen doing this you
must ensure that the blades with the sloping side
(Fig. 6/Y) point outwards and the direction of rota-
tion of these sloping sides (Fig. 6/O1) matches that
of the drilled holes for the housing (Fig. 6/Z).
Before putting the housing cover (Fig. 5/ b) back
onto the shaft end the excess grease in the grease
store (Fig. 5/c) of the B bearing must be completely
removed from the bearing cage. Also grease residue
should be wiped off the end of the shaft and where
the shaft passes through the housing lid. Otherwise
this grease would get into the compressor housing
and would mix with the blade wear debris to form
a paste-like coating that could cause the blades to
jam in the rotor slots.
When screwing the housing lid on the grease-free
screws should be tightened alternately and evenly
so that the lid does not get jammed on the locating
pins. As soon as the lid is almost resting on the front
of the housing, it is advisable to turn the fan to and
fro (using a screw driver or similar) while you fi nish
screwing in the screws. This will prevent the corners
of the blades getting jammed and breaking away.
Screw in the inlet grating (Fig. 4/G)
NOTICE
Ensure that no dirt gets into the bearing. At each
blade change check the grease reservoir (Fig. 5/c)
on the B bearing and top up if necessary.
Fig. 6 Blades
O
1
Direction of rotation
W
Minimum thickness
X
Minimum heigh
Y
Slanting side of the blade
Z
Drilled holes in the housing
Fig. 5 Lubrication/ Blades
G
1
Protective cover
b
Housing lid
c
Grease store
d
Blade
s
Screws
Summary of Contents for Elmo Rietschle V-KTR 100
Page 29: ......