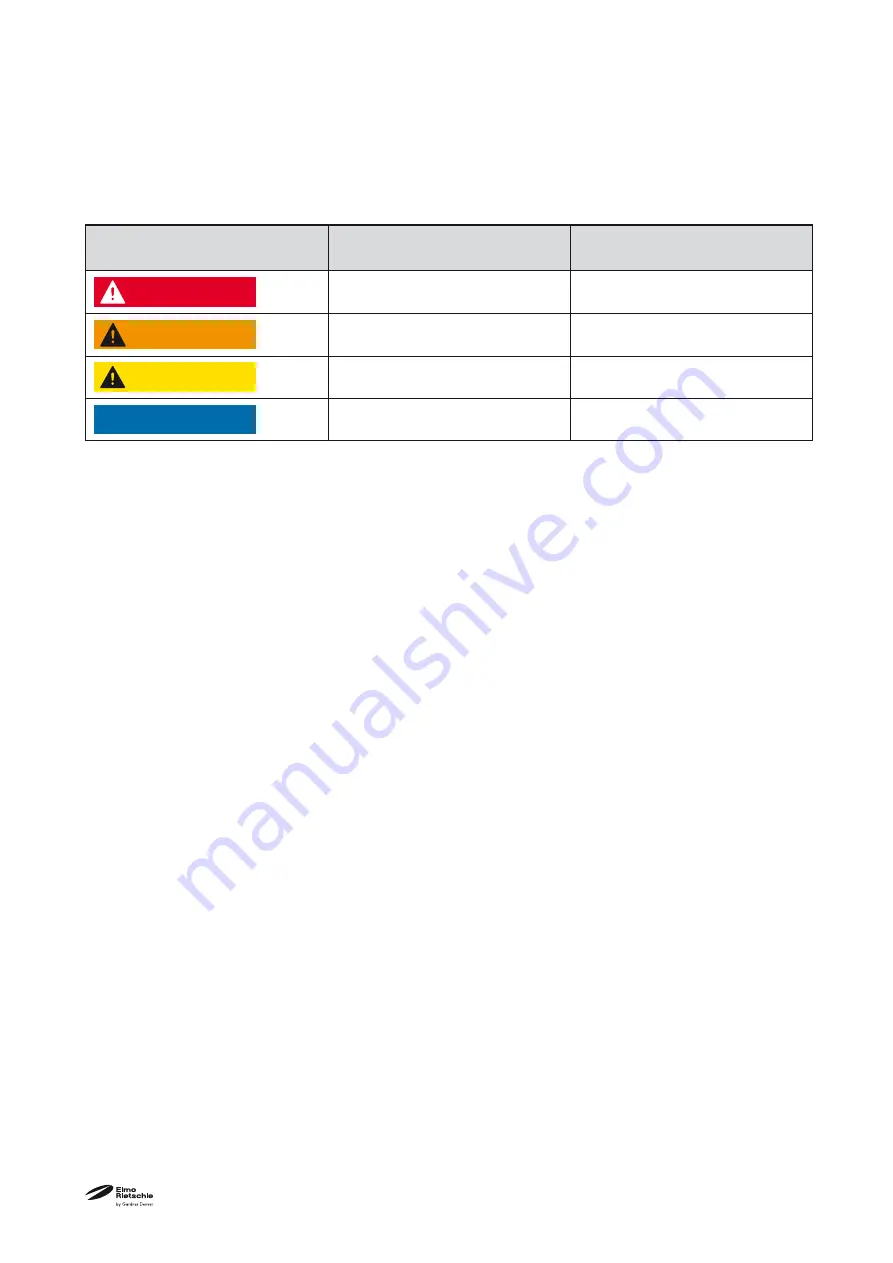
7
www.gd-elmorietschle.com © Gardner Denver Schopfheim GmbH, Gardner Denver Deutschland GmbH
|
Safety
2
Safety
The manufacturer is not responsible for damage due to non-observance of the whole documentation.
2.1 Labelling of warnings
Warning
Danger level
Consequences of
non-observance
DANGER
Imminent danger
Death, severe bodily injury
WARNING
Possible imminent danger
Death, severe bodily injury
CAUTION
Possible hazardous situation
Slight bodily injury
CAUTION
Possible hazardous situation
Material damage
2.2 General
These operating instructions contain basic instructions for installation, commissioning, maintenance and in-
spection work which must be obeyed to ensure the safe operation of the machine and prevent physical and
material damage.
Observe the safety instructions in all chapters.
The operating instructions must be read by the responsible technical personnel / user before installing and
commissioning and must be fully understood. The contents of the operating instructions must always be
available on site for the technical personnel / user. Instructions attached directly to the machine must be
obeyed and must always remain legible. For example, this applies:
• Symbols for connections
• Data plate and motor data plate
• Information signs and warning plates
The user is responsible for observing local regulations.
2.3 Intended use
The machine must only be operated in such areas as are described in the operating instructions:
• Only operate the machine in technically perfect condition
• Do not operate the machine when it is only partially assembled
• The machine must only be operated at an ambient temperature and inlet temperature of between 5 and
40 °C
Please contact us for temperatures outside this range.
• The machine may pump, compress or extract the following media:
• All non-explosive, non-combustible, non-aggressive and non-poisonous dry gases and gas-air
mixtures
• It can also pump extremely damp gases. Water vapour compatibility is very high.
• It is suitable for exhausting air or other gases with increased percentage of oxygen (content by volume
> 21 % and < 60 %) and other gaseous oxidising agents.
If used under critical conditions and/or in case of any doubts, contact the manufacturer. If this is not ob-
served, this can cause personal injuries and property damage.