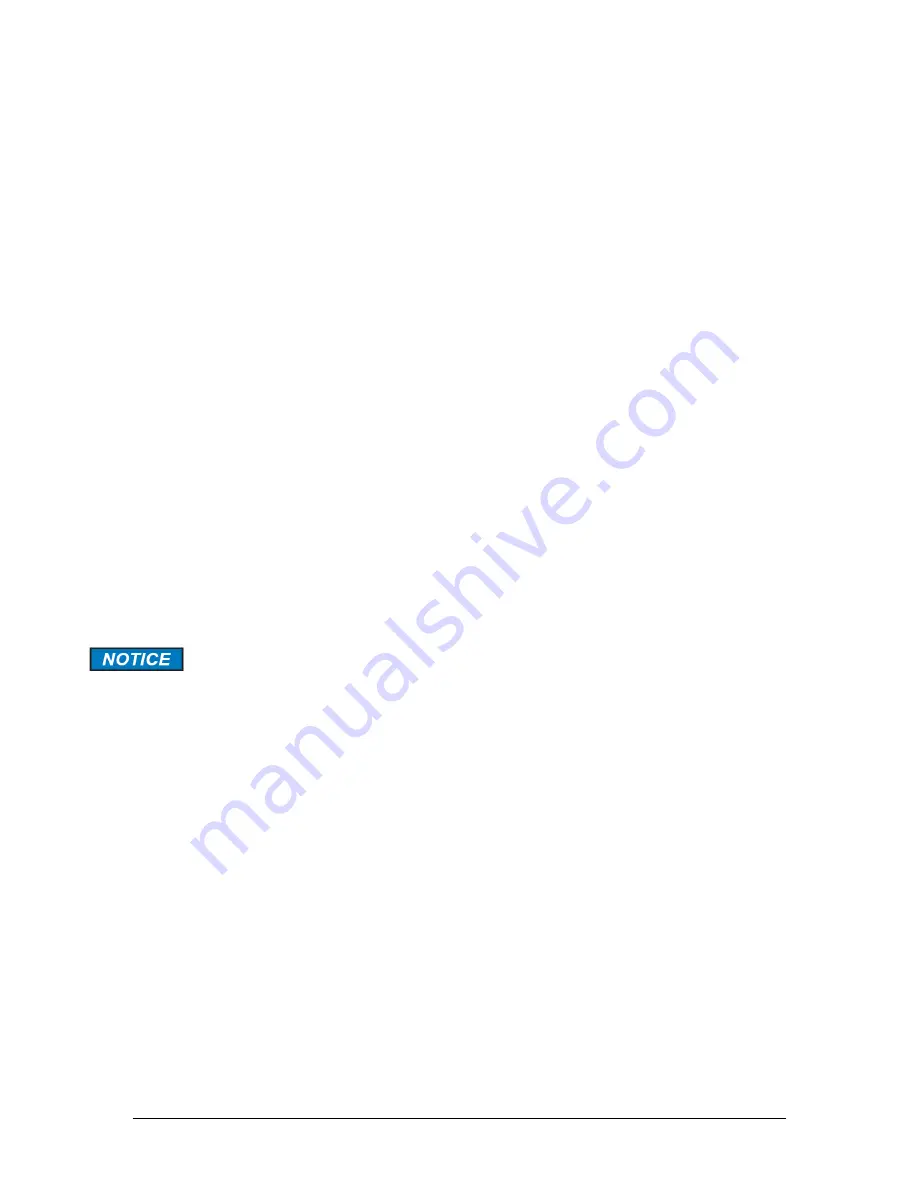
Revision 4
38
April 2020
measurement cell. If the temperature of the incoming sample gas or the sulfur vapour content
of the sample gas inside the measurement cell exceeds a user-set value, the solenoid will
switch on. The condenser control point (either sulfur vapour concentration or probe
temperature) can be configured in the web GUI
– refer to Section 5.4. The
Condenser
Cooling Air Adjust Valve
allows the user to control the flow rate of the instrument air used
to cool the condenser
‘cold finger’ section of the sample probe.
The concentration of sulfur vapour in the process sample gas that makes it into the probe
and into the measurement cell is measured and displayed on the analyzer display as
Sulfur
Vapour (Svap).
The Condenser Cooling Air Adjust Valve can be adjusted to reduce the
sulfur vapour concentration. There is normally a long time constant associated with this
adjustment. Several factors can impact the temperature of the gas exiting the probe. Factors
that affect the temperature of the gas exiting the probe include:
•
Changes in process gas temperature
•
Changes in cooling air temperature
•
Changes in the process gas sample aspiration rate
•
Elapsed time since a probe back-purge
•
Duration of a probe back purge.
During a zero-calibration sequence or back purge operation, instrument air is forced into the
sample probe and the analyzer sample handling system, including the measurement cell.
The indicated sulfur vapour concentration during and immediately after a back-purge
operation is NOT representative of the sulfur vapour concentration in the process sample
gas.
The condenser cooling air flow adjust valve is typically opened two turns from fully closed.
The optimal situtation is that the indicated concentration of sulfur vapour in the
process sample gas exiting in the measurement cell is lower with the probe
cooling air on than with the probe cooling air off, without causing plugging of the
sample probe.
3.4.3 Zero Air Flow Adjust Valve
The
Zero Air Flow Adjust Valve
is used to adjust the flow rate of the instrument air used
for back purge and zero calibration operations. The zero calibration is performed when the
analyzer is in back-purge condition, and the probe and sample handling system, including
the measurement cell, are full of zero gas. Under normal operating circumstances, the valve
is adjusted so that the response time from sample conditions to a stable zero reading is
between 2 and 5 seconds, although depending on the sample probe length, this time may
be somewhat longer. The stabilized zero response is determined by monitoring the time
required for the analyzer gas concentration outputs to stabilize at near zero levels once the
analyzer has been switched from sampling to zero (back purge) mode. Excessive zero air
flow rates will overly cool oven components and may lead to cell temperature control issues.
If the zero air flow rate is set too low, inadequate flushing of the measurement cell before a
zero adjustment is made may result. If the analyzer is zeroed before the measurement cell
has been adequately flushed with zero gas, the concentration readings obtained on sample
gas after returning to sampling mode will likely be lower than expected. This valve is typically
opened one turn from fully closed. In extraordinary circumstances, if sample system or
sample probe clogging due to sulfur vapour condensation occurs, the Zero Air Flow Adjust
Summary of Contents for 943-TGX-CE
Page 132: ...Revision 4 132 April 2020 Figure 81 Oven Cabinet Door Removed ...
Page 133: ...Revision 4 133 April 2020 Figure 82 Control Cabinet Door Removed ...
Page 134: ...Revision 4 134 April 2020 Figure 83 Power Steam Air Signals Connection Details ...
Page 135: ...Revision 4 135 April 2020 Figure 84 AC Wiring Schematic ...
Page 136: ...Revision 4 136 April 2020 Figure 85 DC Signals and Wiring Diagram ...
Page 137: ...Revision 4 137 April 2020 Figure 86 Flow Diagram ...