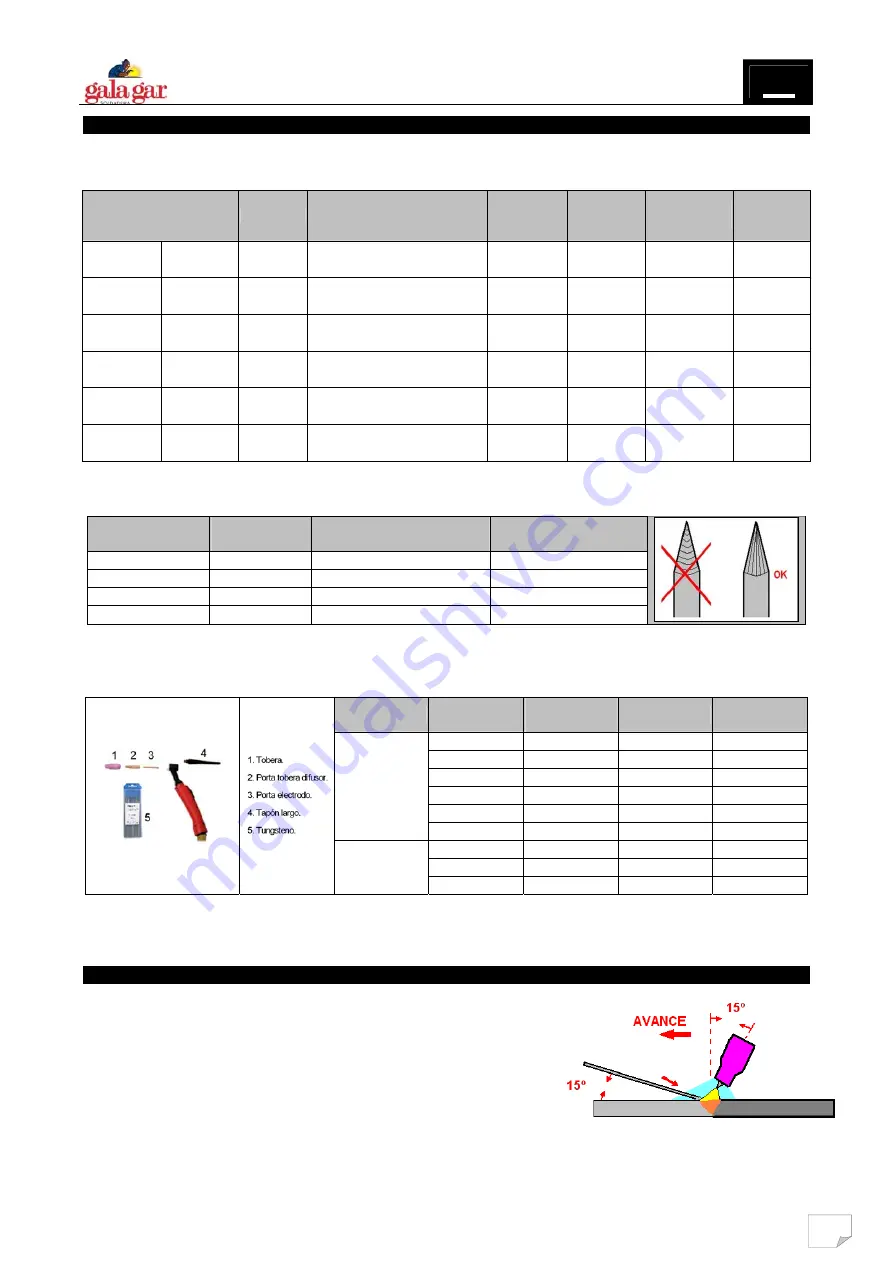
61
GALAXY 3000 GE MV VRD
PT
3.4.1. RECOMENDAÇÕES DE SOLDADURA TIG.
Disporemos de diferentes soluções de eléctrodos de tungsténio em função da sua aplicação e da
percentagem de liga que o compõe.
Tipo de eléctrodo
Corrente
Metal a soldar
Estabilidade
de arco.
Escorvamento
de arco.
Duração do
eléctrodo
Resistência à
temperatura
Tório 0,5%
AZUL
Contínua
Aços ao carbono, inoxidável ,
titânio, ...
** * * **
Tório 1%
AMARELO
Contínua
Aços ao carbono, inoxidável ,
titânio, ...
* ** ** **
Tório 2%
VERMELHO
Contínua
Aços ao carbono, inoxidável ,
titânio, ...
* *** ** **
Cério 2%
CINZENTO
Contínua
Aços ao carbono, inoxidável ,
titânio, ...
** * ** **
Lantânio 1%
PRETO
Contínua
Aços ao carbono, inoxidável ,
titânio, ...
** *** *** ***
Lantânio
1,5%
OURO
Contínua
Aços ao carbono, inoxidável ,
titânio, ...
** *** *** ***
Na tabela inferior identificam-se os tipos de correntes de emprego para cada um dos diâmetros de
eléctrodo e a densidade de corrente recomendadas segundo o material que se deve soldar.
Ø ELÉCTRODO
Intensidades
Min-Max
MATERIAL
Intensidade /
Espessura
1,6 mm
60 a 150A
AÇOS AO CARBONO
30 A/mm
2,0 mm
100 a 200A
AÇOS INOXIDÁVEIS
30-33 A/mm
2,4 mm
170 a 250A
COBRE
70 A/mm
3,2 mm
225 a 330A
A forma da extremidade do eléctrodo afectará directamente a estabilidade do arco eléctrico. O afiamento
debe ser entre 1,5 e 2 vezes o diâmetro do eléctrodo. Com a longitude de 2 vezes o diâmetro do mesmo e o
afiamento debe ser de maneira longitudinal para facilitar a transmissão da corrente.
Material
Espessura
Ø
Tungsténio
Amperes
Nº Boquilha
1,0 1,0
20
-50 4
1,5
1,0 / 1,6
40 - 80
5
2,0
1,6
50 - 90
5
3,0
1,6 / 2,4
70 - 120
6
4,0
2,4
100 - 160
7
Aço ao
carbono e
aço
inoxidável
6,0
3,2
120 - 200
7
1,0
1,0
60 - 80
4
1,5
1,6
100 - 150
5
Cobre e ligas
de cobre
3,0
2,4
160 - 240
6
Como norma geral utilizaremos Árgon como gás de protecção porque a sua baixa energia de ionização
que origina escorvamentos fáceis, arcos muito estáveis e pouco energéticos que o convertem em idóneo para
pequenas espessuras.
3.4.2. EXECUÇÃO DE SOLDADURA.
O material de aportação deverá ser da mesma natureza do que o
metal de base, verificar que se encontre isento de humidade e
seleccionar o diâmetro apropriado em função da espessura que se
deve soldar. Durante a soldadura devemos manter a extremidade da
varinha dentro do campo de actuação do gás de protecção, para
evitarmos a sua contaminação.
Em espessuras inferiores aos 3 mm e com a preparação dos bordes
adequada não sempre é necessário o metal de aportação.