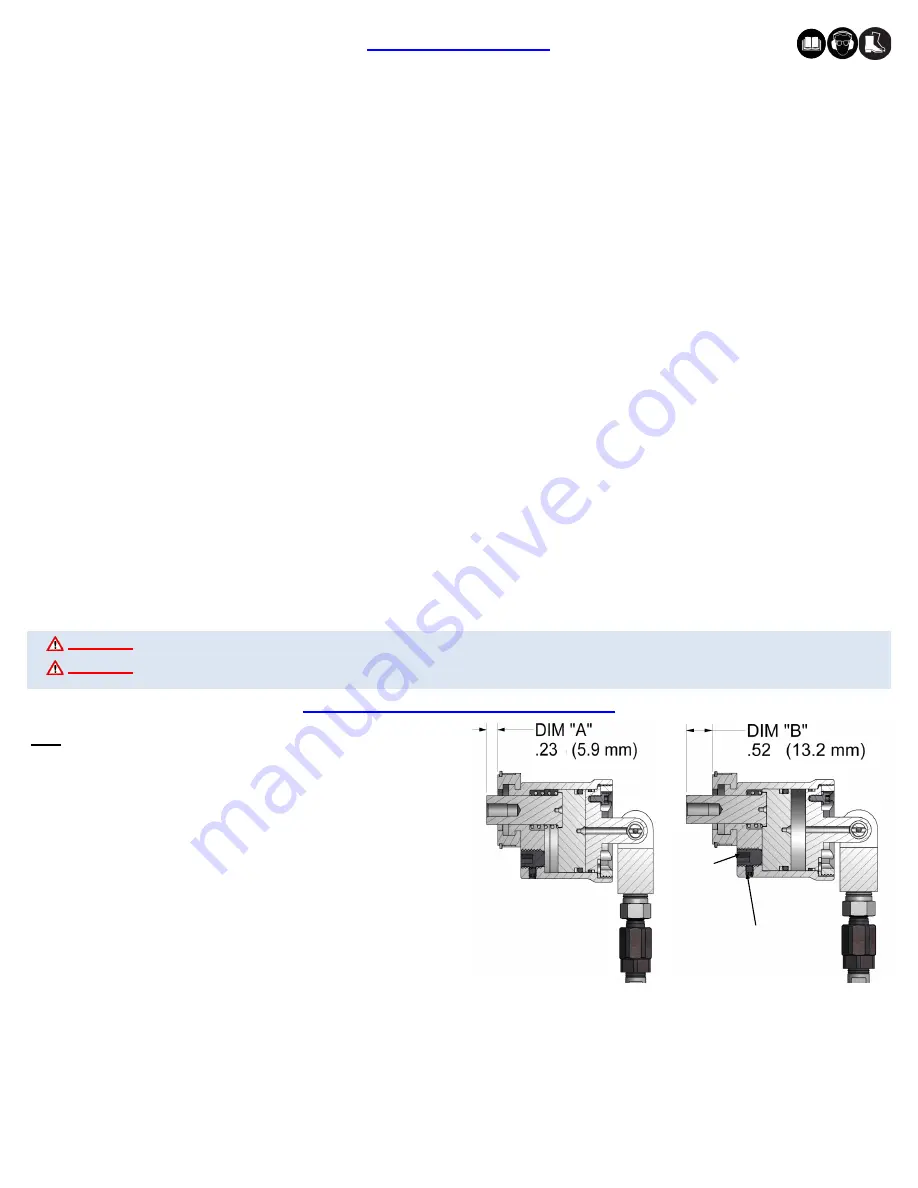
11
Rev. 6/22
GB574/GB574A Installation Tool
TROUBLESHOOTING
Providing all maintenance conditions have been met, follow this systematic approach to diagnosis.
1.
NO OPERATION WHEN ACTUATOR ASSEMBLY
-
AIR (704130) / ELECTRIC ACTUATOR (240122) IS DEPRESSED.
a.) Check powerunit power source.
b.) Control cord or air connection may be loose or damaged.
c.) Faulty Actuator. Replace.
d.) Check hydraulic couplings; tighten, repair or replace.
2.
SLOW OR PARTIAL OPERATION WHEN ACTUATOR ASSEMBLY
-
AIR (704130) / ELECTRIC ACTUATOR (240122) IS DEPRESSED.
a.) Low hydraulic pressure. Check powerunit, adjust.
b.) Back
-
up ring (401118) or o
’
ring (405887) on the piston (574109) could be worn or damaged. Replace.
c.) Excessive wear or scoring on moving parts. Check and replace faulty parts.
3. TOOL OPERATES IN REVERSE.
a.) Check that tool is properly connected to pull side of power source.
4.
HYDRAULIC OIL OVERHEATS.
a.) See hydraulic power source manual.
5.
OIL LEAKAGE.
a.) Hydraulic oil leaks from connections. Tighten threaded connections. Do not use Teflon® tape.
b.) Oil leaks from tool. Determine source of leak and replace worn or defective o
’
rings and back
-
up rings.
6.
Collar of HUCKRIMP® FASTENER NOT SWAGED COMPLETELY.
a.) Tool operating improperly (See above troubleshooting).
b.) Improper stroke. (See setting stroke below).
c.) Improper pressure. (See pressure requirements on page 8).
7.
TOOL
“
HANGS UP
”
ON SWAGED COLLAR OF HUCKRIMP® FASTENER.
a.) Tool operating improperly (see above troubleshooting).
b.) Check that tool is returning properly. Spring (A
-
1684) may be worn. Replace.
SET SCREW
75315
SET
SCREW
A
-
121
SETTING AND ADJUSTING STROKE
WARNING:
Never actuate/dry cycle the tool with nose assembly attached unless a fastener is positioned in the nose assembly.
WARNING:
Incorrect stroke will damage the nose assembly.
Note: The tool stroke is factory set at
.100” (2.54
mm).
Recommended stroke point for
5/32”, 3/16”
and
1/4”
is
.100” (2.5
mm).
When adjusting stroke remove nose assembly.
To adjust stroke: (See
WARNINGS
above).
1.
Adjust the stroke based on fastener size and manufacturers
crimp specifications.
2.
Loosen the set screw (75315).
3.
Then turn the set screw (A
-
121) clockwise to decrease the
stroke and counter clockwise to increase the stroke.
4.
After desired stroke is set, tighten set screw (75315) to lock.
5.
Check crimped fastener with GO/NOGO gage to determine
if a fine adjustment is required.
6.
Fine adjustments should be done by 1/8 to 1/4 turns until
desired diameter is achieved.
To set stroke: (See
WARNINGS
above).
1.
Using a pair of dial calipers, measure
“
A
”
dimension.
2.
Holding in actuator, measure
“
B
”
dimension.
3.
Subtracting
“
A
”
dimension from
“
B
”
dimension equals stroke.