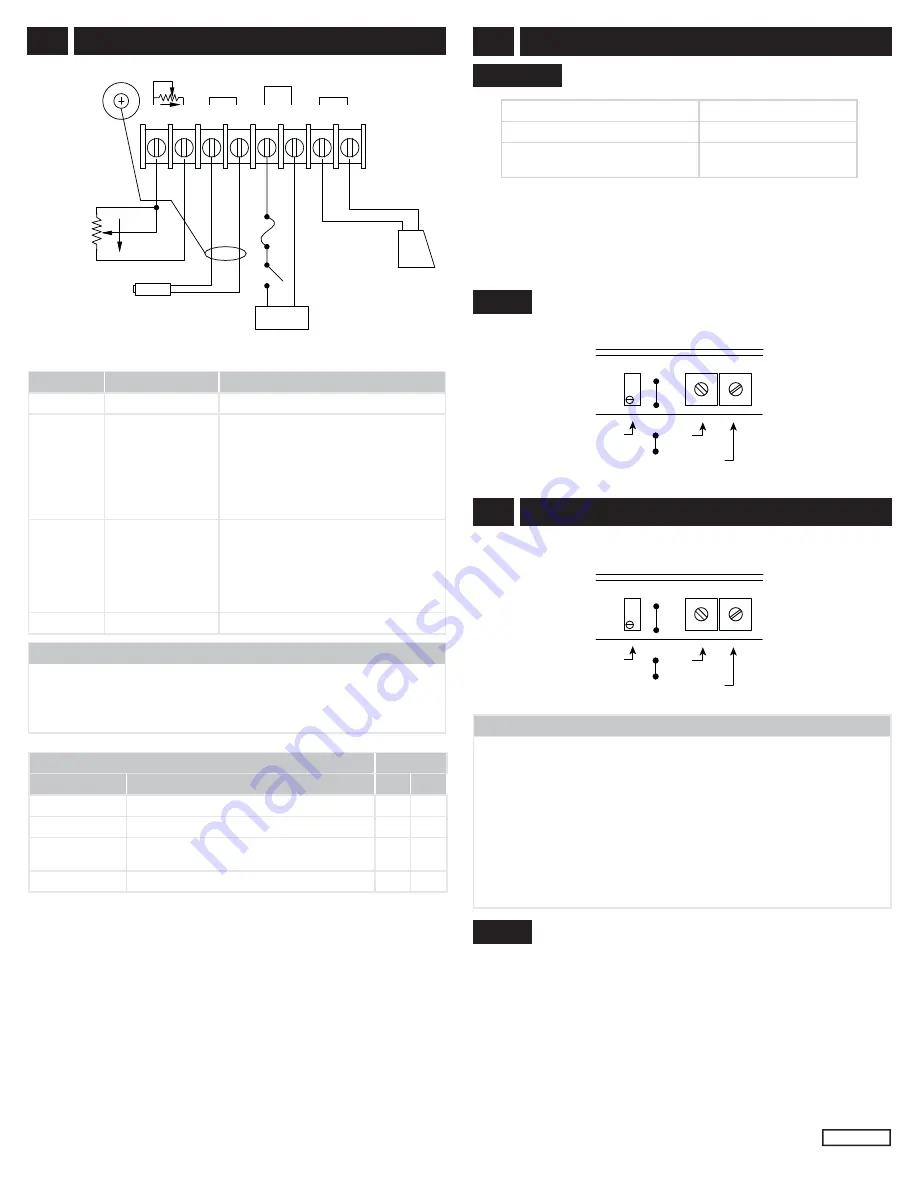
2
© 2016 Copyright All Rights Reserved
ESD2200 Electronic Speed Control Unit
10.14.16
PIB 1022
D
3
WIRING
A
B
C
D
E
F
G
H
ACTUATOR
PICK-UP
BATTERY
+
_
SPEED TRIM
OPTIONAL
SPEED TRIM
CONTROL
15A
FUSE
S1
BATTERY
ACTUATOR
MAGNETIC
SPEED PICK-UP
+
_
CW
4
5
STARTING THE ENGINE
ADJUSTING FOR STABILITY
The speed control unit governed speed setting is factory set at approximately
engine idle speed. (1000 Hz., Speed sensor signal or 600 RPM)
Crank the engine with DC power applied to the governor system. The actuator
will energize to the maximum fuel position until the engine starts. The governor
system should control the engine at a low idle speed. If the engine is unstable
after starting, refer to Section 5 ADJUSTING FOR STABILITY.
START FUEL ADJUSTMENT
1.
Rotate the GAIN adjustment clockwise until instability develops. Gradu-
ally move the adjustment counterclockwise until stability returns. Move
the adjustment one division further counterclockwise to insure stable
performance (270° pot).
2.
Rotate the STABILITY adjustment clockwise until instability develops.
Gradually move the adjustment counterclockwise until stability returns.
Move the adjustment one division further to insure stable performance
(270° pot).
3.
Gain and stability adjustments may require minor changes after engine
load is applied. Normally, adjustments made at no load achieve satis-
factory performance.
Gain
Middle Position
Stability
Middle Position
Speed Trim Control
(Infused)
Middle Position
IMPORTANT
Make sure the following adjustments are set before starting
the engine.
The governed speed set point is increased by clockwise rotation of
the SPEED adjustment control. Remote speed adjustment can be
obtained with an optional 5K Speed Trim Control.
NOTE
Once the engine is running at operating speed and at no load, the following
governor performance adjustments can be made to increase engine stability.
TERMINAL
DEFINITION
NOTES
A & B
Speed Trim
#18 AWG (1.3mm sq) or larger wire
C & D
Magnetic Speed
Pickup
(D is ground)
Wires must be twisted and/or shielded
for their entire length
Gap between speed sensor and gear
teeth should not be smaller than 0.02 in.
(.51mm)
Speed sensor voltage should be at least
1V AC RMS during crank
E & F
Battery Power (+/-)
#16 AWG (1.3mm sw) or larger wire
A 15 amp fuse must be installed in the
positive battery lead to protect against
reverse voltage
Battery positive (+) input is Terminal E
G & H
Actuator (+/-)
#16 AWG (1.3mm sw) or larger wire
RECOMMENDATIONS
1.
2.
Shielded cable should be used for all external connections to the ESD
control.
One end of each shield, including the speed sensor shield, should be
grounded to a single point on the ESD case.
If instability cannot be corrected or further performance improve-
ments are required, refer to Section 6 SYSTEM TROUBLE-
SHOOTING.
NOTE
SPEED
GAIN
STABILITY
E4
E5
SPEED
GAIN
STABILITY
E4
E5
Versions
Voltage
Part Number
Feature / Product Details
12V
24V
ESD2210
Standard Unit
X
X
ESD2241
Standard Unit with Idle
X
ESD2243
For Hoist FT/Operates with Foot Pedal,
5000 Hz Speed Range
X
ESD2244
Light Force (Low-Current Optimized PID)
X
X
25x
TORQE