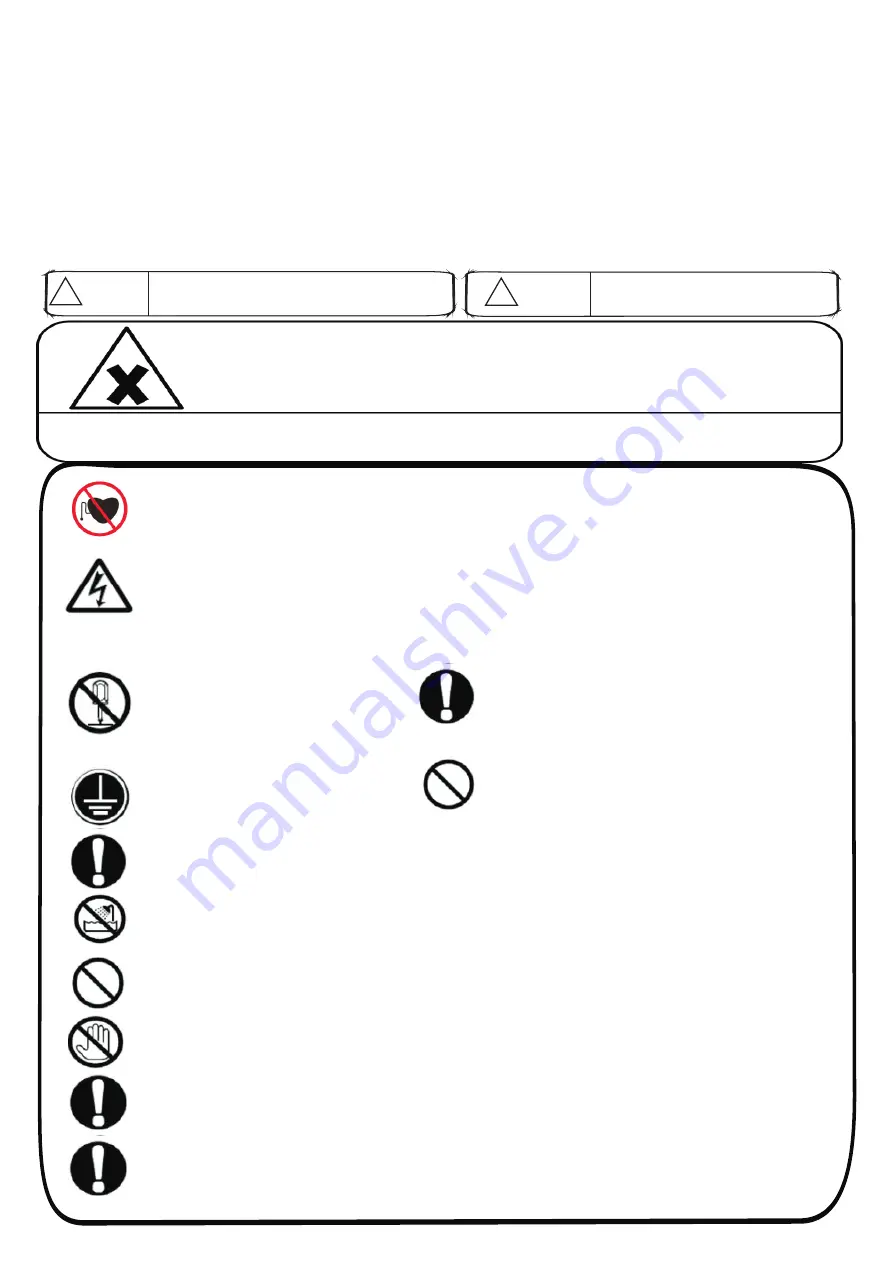
▲
▲
◆
◆
◆
◆
◆
◆
◆
◆
◆
◆
◆
◆
◆
◆
◆
Preface
Please
read
this
instruction
manual
carefully
before
using
and
the
equipment
and
refer
to
it
as
needed
to
ensure
the
continued
safe
operation
of
the
equipment
.
This instruction manual should be read completely before attempting to use or service the equipment.
Failure to follow the instructions in this manual could result in property damage, severe personal injury, or
death.
The followingwarnings and importantnotices are used in the instructionmanual:
!
WARNING
Improper use of this equipment can cause
personal injury or property property damage
操 作 错 误 时 。 有 可 能 会 造 成 人 体 死 亡 或 重 伤 的 危 险
DANGER
Improper use of this equipment can cause
serious or fatal injury
.
Magnetic fields can affect pacemakers. Pacemaker wearers keep away from the equipment.
Wearers should consult their doctor before going near equipment operations.
Do not touch any live electrical parts. Wear dry, hole-free insulating gloves and body
protection. The input power circuit and machine internal circuit are live with high voltage
when power is on. Touching live electrical parts can cause fatal shocks or severe burns. High
voltage exists in the power supply socket. Never touch the conductor terminals with bare
hand.
Input power installation must meet national standard. All electrical connections must be
made by a qualified electrician. Insulated gloves and shoes must be worn when connecting
input power or maintaining equipment.
Never
disassemble
,
repair
,
alter
or
rebuild
the
equipment
without
approval
from
the
manufacturer
.
There
is
a
risk
for
electrical
shock
and
fire
.
Electric
shock
can
kill
.
Properly
ground
this
equipment
according
to
its
user
manual
and
national
standard
.
Make sure the supply cable is up to national standard or
local code.Use only the right gauge of electrical
wire/cable.There is a risk of fire or electrical shock if
overload building wiring
-
be sure power supply system is
properly sized,rated and protected to handle
this unit
.
Replace power cord/wire/cable immediately
-
bare wiring can kill
.
Do
not
step
on
,
twist
or
pull
the
power
cord
..
Frequently inspect input power cord and regularly clean the unit to
remove dust and dirt.Any worn or damaged power
cord
or
internal
components
in
heavy
dust
may
cause
electrical
shock
,
short
circuit
or
fire
.
In the event of abnormal
,
operation must
be
immediately stopped
.
If smoke, smell or abnormal noise is produced by the
unit, disconnect
the
power
cord
immediately and contact your
local dealer
.
Do
not
use
it
until
the
problem
is
fixed
.
Do
not
operate
or
place
the
device
near
water
or
in
wet
locations
.
Risk
for
electrical
shock
or
damage
to
the
device
.
Do
not
operate
the
equipment
in
potential
hazardous
areas
:
chemicals
,
oil
,
gas
and
mining
,
or
the
worksites
where
power
supply
system
is
in
poor
condition
.
Use
only
well
-
maintained
device
.
Inspect
and
maintain
the
device
for
safety
every
12
months
,
including
cleaning
and
removing
dust
.
Repair
or
replace
damaged
parts
/
cables
at
once
.
Follow the installation and operation instruction to ensure user safety and proper equipment
performance. It is the responsibility of the owner to ensure that the equipment has been installed and
operated as specified in the instructions provided. The manufacturer takes no responsibility for any loss
or damage suffered as a result of using the equipment incorrectly or improperly.
X
Improper use of this equipment
can cause
serious or fatal injury
◆
◆
◆
Hot parts can cause severe burns.Do not touch workpieces or metallic parts of torch with bare hands during or after
welding.Allow cooling period and use a proper tools or wear welding gloves to handle hot parts to prevent burns.