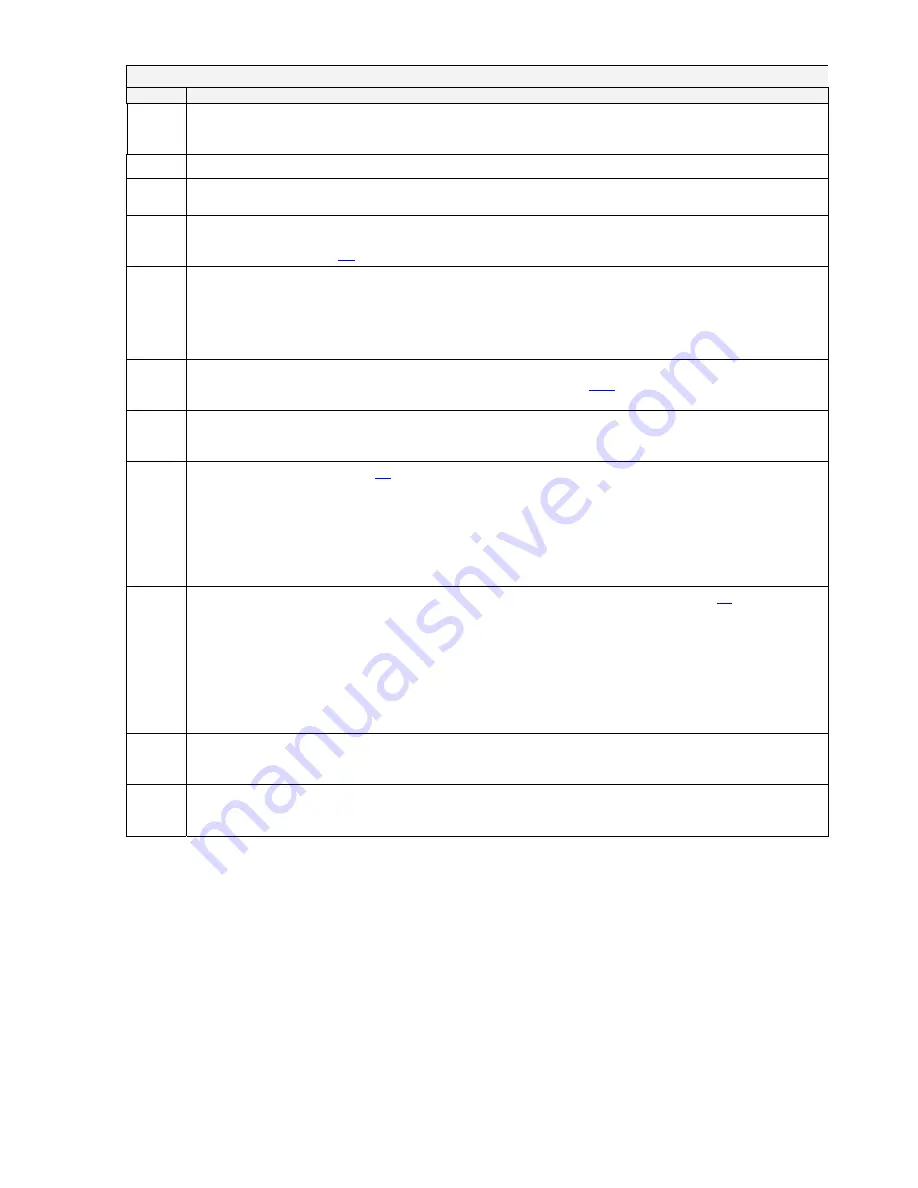
Product Specification
Page 15 of 18
1303090MS01
LA-309 Controlled Atmosphere Infrared Furnace
April 15, 2009
Table 16-1. Base Equipment Features
KEY
DESCRIPTION
PC
Computer, Managed Platform.
PC configured to act as the interface the operator uses communicate with the
furnace PLC, store process recipes, log furnace behavior and reinstall furnace software. Includes dual drives in
RAID1 array and dual Ethernet network interface ports.
PCM
Monitor, LCD.
Standard 4:3 aspect ratio, 17 inch LCD monitor.
Standard on most furnaces.
PH2 Product
Height.
Standard furnace clearance allows a maximum of 50 mm (2 inch) high product to pass through all
baffle and cooling section throats, and zone dividers.
Standard on all furnaces.
PLC
Programmable Logic Controller.
The 32-bit industrial computer that controls the actual operation of the furnace. It
sends and receives analog and digital signals from the furnace to control the furnace behavior. Programming of the
PLC is performed from the
.
Standard on most furnaces.
SCR
Computerized SCR Load Management.
Computer/PLC controlled SCR power modules that operate the furnace
efficiently through phase angle firing, providing steady state, true proportioning control of the IR lamps without flicker.
Each SCR firing circuit accepts process command signals from the PLC to regulate the power delivered to the heating
elements in each furnace zone. Actual power output to the lamps in each zone is displayed directly on the OIT. Each
SCR can be calibrated for maximum voltage output and maximum permissible power applied to each zone can be
limited via the OI. Loads shall be balanced across phases.
Standard on all furnaces.
SI
Metric Units of Measure.
Furnace control software shall depict belt speed in centimeters per minute (cm/min).
Temperature units shall be degrees Celcius (°C).
No cost option in lieu of
on most furnaces if SI is selected at
time of order.
SPL
Split for Shipment:
Furnace may be manufactured to allow separation into sections to facilitate shipping and
relocation.
Standard on all furnaces 5.7 m (225 in.) long or longer. Option available on furnaces 4.6 m –5.3 m (180 in.-
210 in.) long.
TT Transition
Tunnel.
Similar to the
Exit Baffle/Exhaust Eductor, the transition tunnel works as a barrier to prevent
contaminants from passing from the heating section into the cooling section. The transition tunnel is housed inside an
aluminum shell lined with ceramic fiber insulation and is fully insulated so that it will lose heat gradually. A metal air
rake introduces a gas curtain above the belt to purge the tunnel and a series of four equally spaced hanging baffle
gates effectively isolate the high temperature furnace section from the cooling section.
A venturi-assisted exhaust stack draws furnace gases from the last zone, across a drip tray and out of the furnace to
prevent exhaust condensation from falling into the transition baffle. Proper operation of this system keeps the furnace
interior clean.
Standard on most furnace models.
TTDE
Transition Tunnel, Dual Eductors.
The TTDE module is similar in construction and design to the
Tunnel with the addition of a 2
nd
Exhaust Eductor to prevent contaminants from passing from the heating section into
the cooling section. The transition tunnel is housed inside an aluminum shell lined with ceramic fiber insulation and is
fully insulated so that it will lose heat gradually. A metal air rake introduces a gas curtain above the belt to purge the
tunnel and a series of four equally spaced hanging baffle gates effectively isolate the high temperature furnace
section from the cooling section. Two exhaust eductors, one at each end of the tunnel, expedite removal of gaseous
contaminants from the furnace atmosphere and establish a counter flow of cooler gas from the cooling section, raising
a high barrier to contamination passing from furnace to cooling section. Each eductor shall have a separate flow
meter control for proper balancing of the exhaust flow.
Standard on some furnace models with multiple CACT or
CACW cooling modules. Option available on most other furnaces.
ULOAD Unload
Station.
The unload station is an area 38.1 cm long (15 inch) at the exit of the furnace which provides open
access to accommodate removing product from the continuous belt after processing by the furnace.
Standard on all
furnaces.
UT Universal
Transformers.
Multi-tap transformers that convert power lines ranging from 208 Vac to 480 Vac to
voltages required by the furnace control system and accessories, and allow change to a different power line voltage
with a single tap change. Other voltages can be accommodated upon request.
Standard on all furnaces.
Summary of Contents for LA-309
Page 5: ...10 004 676 110000 v WARRANTY Warranty goes here ...
Page 6: ...vi LA 309 Owner s Manual ...
Page 12: ...Contents xii LA 309 Owner s Manual ...
Page 20: ...Section 1 1 8 LA 309 Owner s Manual ...
Page 68: ...Section 3 3 28 LA 309 Owner s Manual ...
Page 70: ...Section 4 4 2 LA 309 Owner s Manual ...
Page 72: ...Section 4 4 4 LA 309 Owner s Manual ...
Page 98: ...Section 5 5 2 LA 309 Owner s Manual ...
Page 100: ...Section 5 5 4 LA 309 Owner s Manual ...
Page 106: ...Section 5 5 10 LA 309 Owner s Manual ...
Page 108: ...Section 5 5 12 LA 309 Owner s Manual ...
Page 110: ...Section 5 5 14 LA 309 Owner s Manual ...
Page 112: ...Section 6 6 2 LA 309 Owner s Manual ...
Page 114: ......
Page 115: ......
Page 126: ...Section 7 1 Fiberfrax Cements MSDS 042006 Owner s Manual ...
Page 139: ...MSDS 2 Fiberfrax Duraboard MSDS 042006 MATERIAL SAFETY DATA SHEETS ...
Page 140: ...Section 7 2 Fiberfrax Duraboard MSDS 042006 Owner s Manual ...
Page 153: ...MSDS 3 Fiberfrax Fibers MSDS 042006 MATERIAL SAFETY DATA SHEETS ...
Page 154: ...Section 7 3 Fiberfrax Fibers MSDS 042006 Owner s Manual ...
Page 167: ...MSDS 4 Fiberfrax Papers MSDS 042006 MATERIAL SAFETY DATA SHEETS ...
Page 168: ...Section 7 4 Fiberfrax Papers MSDS 042006 Owner s Manual ...
Page 181: ...MSDS 5 Magnaform MSDS 050406 MATERIAL SAFETY DATA SHEETS ...
Page 182: ...Section 7 5 Magnaform MSDS 050406 Owner s Manual ...
Page 183: ......
Page 184: ......
Page 185: ...Section 7 6 RTU Silicone Red Hi Temp 042006 Owner s Manual ...
Page 186: ...MSDS 6 RTU Silicone Red Hi Temp 042006 MATERIAL SAFETY DATA SHEETS ...
Page 189: ...Section 7 7 Kaowool Insulation MSDS 050406 Owner s Manual ...
Page 190: ...MSDS 7 Kaowool Insulation MSDS 050406 MATERIAL SAFETY DATA SHEETS ...
Page 201: ...Material Safety Data Sheets 7 15 Notes ...
Page 202: ...Section 7 7 16 Owner s Manual ...
Page 204: ...Section 8 Owner s Manual ...
Page 206: ...Section 8 Owner s Manual ...
Page 212: ...iv Operation and Troubleshooting ...
Page 214: ...vi Operation and Troubleshooting ...
Page 224: ...Page 10 Operation and Troubleshooting ...
Page 231: ...9 1 Section 9 APPENDIX B 9 1 EC913 CALIBRATION REPORT 9 2 SERIES EC900 OXYGEN ANALYZERS ...
Page 232: ...Section 8 Owner s Manual ...
Page 233: ......
Page 234: ...Section 8 Owner s Manual ...
Page 279: ...Section 8 Owner s Manual ...
Page 281: ...MSDS MATERIAL SAFETY DATA SHEETS ...
Page 282: ...16 Notes ...