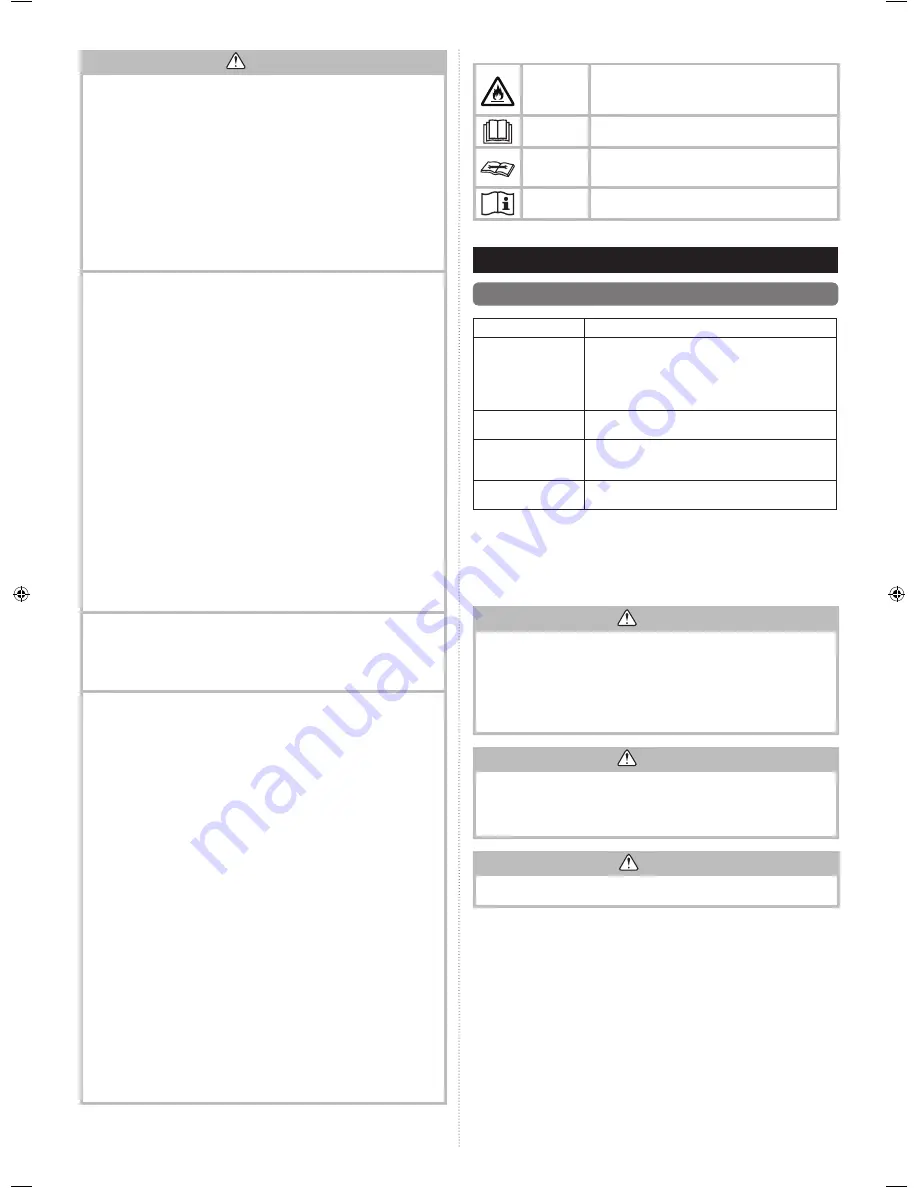
En-3
CAUTION
9-Charging procedures
• In addition to conventional charging procedures, the following requirements shall be
followed.
- Ensure that contamination of different refrigerants does not occur when using
charging equipment.
- Hoses or lines shall be as short as possible to minimize the amount of refrigerant
contained in them.
- Cylinders shall be kept upright.
- Ensure that the refrigeration system is earthed prior to charging the system with
refrigerant.
- Label the system when charging is complete (if not already).
- Extreme care shall be taken not to over
fi
ll the refrigeration system.
• Prior to recharging the system it shall be pressure tested with OFN.
• The system shall be leak tested on completion of charging but prior to commission-
ing.
• A follow up leak test shall be carried out prior to leaving the site.
10-Decommissioning
• Before carrying out this procedure, it is essential that the technician is completely
familiar with the equipment and all its details.
• It is recommended good practice that all refrigerants are recovered safely.
• Prior to the task being carried out, an oil and refrigerant sample shall be taken in
case analysis is required prior to re-use of reclaimed refrigerant.
• It is essential that electrical power is available before the task is commenced.
a) Become familiar with the equipment and its operation.
b) Isolate system electrically.
c) Before attempting the procedure ensure that:
• mechanical handling equipment is available, if required, for handling refriger-
ant cylinders;
• all personal protective equipment is available and being used correctly;
• the recovery process is supervised at all times by a competent person;
• recovery equipment and cylinders conform to the appropriate standards.
d) Pump down refrigerant system, if possible.
e) If a vacuum is not possible, make a manifold so that refrigerant can be removed
from various parts of the system.
f) Make sure that cylinder is situated on the scales before recovery takes place.
g) Start the recovery machine and operate in accordance with manufacturer’s
instructions.
h) Do not over
fi
ll cylinders. (No more than 80 % volume liquid charge).
i) Do not exceed the maximum working pressure of the cylinder, even temporarily.
j) When the cylinders have been
fi
lled correctly and the process completed, make
sure that the cylinders and the equipment are removed from site promptly and all
isolation valves on the equipment are closed off.
k) Recovered refrigerant shall not be charged into another refrigeration system un-
less it has been cleaned and checked.
11-Labelling
• Equipment shall be labelled stating that it has been de-commissioned and emptied
of refrigerant.
• The label shall be dated and signed.
• Ensure that there are labels on the equipment stating the equipment contains
fl
am-
mable refrigerant.
12-Recovery
• When removing refrigerant from a system, either for servicing or decommissioning, it
is recommended good practice that all refrigerants are removed safely.
• When transferring refrigerant into cylinders, ensure that only appropriate refrigerant
recovery cylinders are employed.
• Ensure that the correct number of cylinders for holding the total system charge are
available.
• All cylinders to be used are designated for the recovered refrigerant and labelled for
that refrigerant (i.e. special cylinders for the recovery of refrigerant).
• Cylinders shall be complete with pressure relief valve and associated shut-off valves
in good working order.
• Empty recovery cylinders are evacuated and, if possible, cooled before recovery
occurs.
• The recovery equipment shall be in good working order with a set of instructions
concerning the equipment that is at hand and shall be suitable for the recovery of
fl
ammable refrigerants.
• In addition, a set of calibrated weighing scales shall be available and in good working
order.
• Hoses shall be complete with leak-free disconnect couplings and in good condition.
• Before using the recovery machine, check that it is in satisfactory working order, has
been properly maintained and that any associated electrical components are sealed
to prevent ignition in the event of a refrigerant release.
Consult manufacturer if in doubt.
• The recovered refrigerant shall be returned to the refrigerant supplier in the correct
recovery cylinder, and the relevant Waste Transfer Note arranged.
• Do not mix refrigerants in recovery units and especially not in cylinders.
• If compressors or compressor oils are to be removed, ensure that they have been
evacuated to an acceptable level to make certain that
fl
ammable refrigerant does not
remain within the lubricant.
• The evacuation process shall be carried out prior to returning the compressor to the
suppliers.
• Only electric heating to the compressor body shall be employed to accelerate this
process.
• When oil is drained from a system, it shall be carried out safely.
Explanation of symbols displayed on the indoor unit or outdoor unit.
WARNING
This symbol shows that this appliance uses a
fl
ammable
refrigerant.
If the refrigerant is leaked and exposed to an external igni-
tion source, there is a risk of
fi
re.
CAUTION
This symbol shows that the operation manual should be
read carefully.
CAUTION
This symbol shows that a service personnel should be
handling this equipment with reference to the installation
manual.
CAUTION
This symbol shows that information is available such as
the operating manual or installation manual.
2. ABOUT THIS PRODUCT
2.1. Special tools for R32 (R410A)
Tool name
Change from R22 to R32 (R410A)
Gauge manifold
Pressure is high and cannot be measured with a R22
gauge. To prevent erroneous mixing of other refrigerants,
the diameter of each port has been changed.
It is recommended to use gauge with seals -0.1 to 5.3 MPa
(-1 to 53 bar) for high pressure.
-0.1 to 3.8 MPa (-1 to 38 bar) for low pressure.
Charge hose
To increase pressure resistance, the hose material and base
size were changed. (R32/R410A)
Vacuum pump
A conventional vacuum pump can be used by installing a
vacuum pump adapter.
(Use of a vacuum pump with a series motor is prohibited.)
Gas leakage detector
Special gas leakage detector for HFC refrigerant R410A or
R32.
Copper pipes
It is necessary to use seamless copper pipes and it is desirable that the amount of residual
oil is less than 40 mg/10 m. Do not use copper pipes having a collapsed, deformed or
discolored portion (especially on the interior surface). Otherwise, the expansion value or
capillary tube may become blocked with contaminants.
As an air conditioner using R32 (R410A) incurs pressure higher than when using R22, it is
necessary to choose adequate materials.
WARNING
• Do not use the existing (for R22) piping and
fl
are nuts.
If the existing materials are used, the pressure inside the refrigerant cycle will rise and
cause failure, injury, etc. (Use the special R32/R410A materials.)
• Use (re
fi
ll or replace with) speci
fi
ed refrigerant (R32) only. Use of unspeci
fi
ed refriger-
ant can cause product malfunction, burst, or injury.
• Do not mix any gas or impurities except speci
fi
ed refrigerant (R32). In
fl
ow of air or ap-
plication of unspeci
fi
ed material makes the internal pressure of the refrigerant cycle too
high, and may cause product malfunction, burst of piping, or injury.
WARNING
• For appropriate working of the air conditioner, install it as written in this manual.
• To connect indoor unit and outdoor unit, use air conditioner piping and cables available
through your local distributor. This manual describes proper connections using such
installation set.
• Do not turn on the power until all work has been completed.
CAUTION
This manual describes how to install the indoor unit only. To install the outdoor unit, refer
to the installation manual included in each product.
• Be careful not to scratch the air conditioner when handling it.
• After installation, explain correct operation to the customer, using the operating manual.
9333005201_IM_En_ASTG09KMCA.indd 3
9333005201_IM_En_ASTG09KMCA.indd 3
2017/1/20 11:43:03
2017/1/20 11:43:03
Summary of Contents for ASTG12CMCB
Page 16: ......