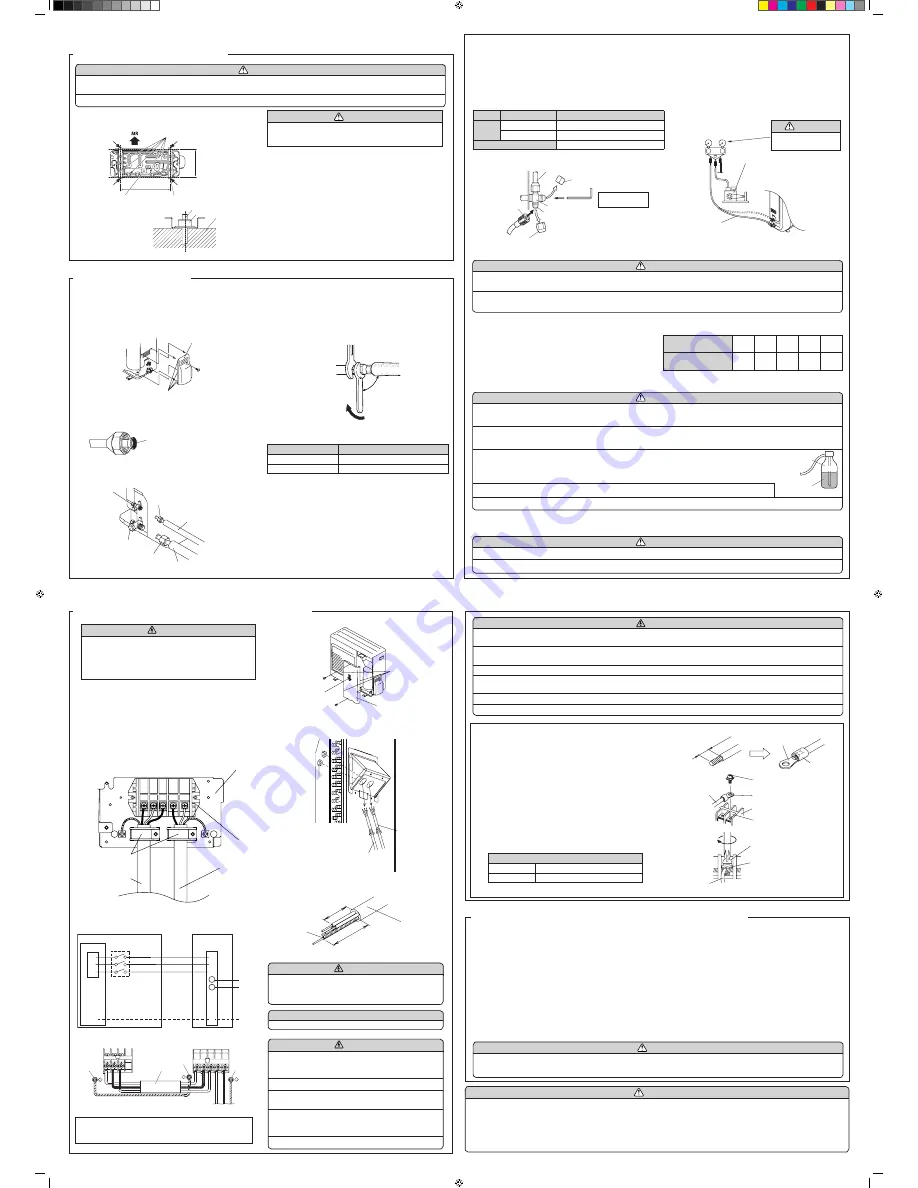
OUTDOOR UNIT
WARNING
Install the unit where it will not be tilted by more than 3°. However, do not install the unit with it tilted to-
wards the side containing the compressor.
When installing the outdoor unit where it may exposed to strong wind, fasten it securely.
(1) Outdoor unit to be fasten with bolts at the four places
indicated by the arrows without fail.
(2) Fix securely with
b o l t s o n a s o l i d
block. (Use 4 sets of
commercially avail-
able M10 bolt, nut
and washer.)
CAUTION
Do not use the drain pipe and drain cap. If the drain pipe and drain
cap are used, the drain water in the pipe may freeze in extremely
cold weather.
Bolt
Nut
Block
PUMP DOWN OPERATION (FORCED COOLING OPERATION)
To avoid discharging refrigerant into the atmosphere at the time of relocation or disposal, recover refrigerant by doing the cooling operation
or forced cooling operation according to the following procedure. (When the cooling operation cannot start in winter, and so on, start the
forced cooling operation.)
(1) Do the air purging of the charge hose by connecting the charging hose of gauge manifold to the charging port of 3-way valve (large) and
opening the low-pressure valve slightly.
(2) Close the valve stem of 3-way valve (small) completely.
(3) Start the cooling operation or following forced cooling operation.
When using the remote controller
Press the TEST RUN button after starting the cooling operation by the remote controller.
The operation indicator lamp and timer indicator lamp will begin to flash simultaneously during test run.
When using the MANUAL AUTO button of the indoor unit (The remote controller is lost, and so on.)
Keep on pressing the MANUAL AUTO button of the indoor unit for more than 10 seconds.
(The forced cooling operation cannot start if the MANUAL AUTO button is not kept on pressing for more than 10 seconds.)
(4) Close the valve stem of 3-way valve (large) when the reading on the compound pressure gauge becomes 0.05~0 MPa (0.5~0 kg/cm
2
).
(5) Stop the operation.
• Press the START/STOP button of the remote controller to stop the operation.
• Press the MANUAL AUTO button when stopping the operation from indoor unit side.
(It is not necessary to press on keeping for more than 10 seconds.)
CAUTION
Install heat insulation around both the gas and liquid pipes. Failure to do so may cause water leaks.
Use heat insulation with heat resistance above 248 °F (120 °C). (Reverse cycle model only)
In addition, if the humidity level at the installation location of the refrigerant piping is expected to exceed 70%, install heat
insulation around the refrigerant piping. If the expected humidity level is 70-80%, use heat insulation that is 9/16” (15 mm) or
thicker and if the expected humidity exceeds 80%, use heat insulation that is 13/16” (20 mm) or thicker.
If heat insulation is used that is not as thick as specified, condensation may form on the surface of the insulation.
In addition, use heat insulation with heat conductivity of 0.045 W/(m·K) or less [at 68 °F (20 °C)].
CAUTION
During the pump-down operation, make sure that the compressor is turned off before you remove the refrigerant piping.
Do not remove the connection pipe while the compressor is in operation 3-way valve open. This may cause abnormal pres-
sure in the refrigeration cycle that leads to breakage and even injury.
Bottom side
Drain port
Drain port
25-9/16”
(650 mm)
4-ø 12 hole
14-9/1
6”
(370 mm)
ELECTRICAL WIRING (OUTDOOR UNIT)
(1) Service cover removal
• Remove the two mounting screws.
• Remove the service cover by pushing downwards.
(2) Fasten the power supply cord and the connection cord to the
conduit holder using the lock nut.
(open the knock out holes if necessary)
(3) Connect the power supply cord and the connection cord to
terminal.
(4) Fasten the power supply cord and connection cord with cord
clamp.
1-3/1
6” (30 mm)
Keep the earth wire longer than the other wires.
CAUTION
Be sure to comply with local codes while running the
wire from the indoor unit to the outdoor unit (size of
wire and wiring method, etc.).
Every wire must be connected firmly.
No wire should be allowed to touch refrigerant tubing,
the compressor or any moving part.
Loose wiring may cause the terminal to overheat or
result in unit malfunction. A fire hazard may also exist.
Therefore, be sure all wiring is tightly connected.
Connect wires to the matching numbers of terminals.
1
2
3
1
2
3
G
G
L1
L2
INDOOR
INDOOR UNIT
OUTDOOR UNIT
TERMINAL
DISCON-
NECT
SWITCH
(FIELD
SUPPLY)
Grounding
line
14AWG
(Inter-unit)
Power lines
230/208 V
230/208 V
230/208 V
TERMINAL
Power supply line
Single-phase, 230/208
V
G
G
G
G
Control box
Terminal
Power supply cord
Connection cord
(indoor unit and
outdoor unit
connection cord)
Cord clamp
CAUTION
When connecting the power supply cord, make sure that
the phase of the power supply matches with the phase of
the terminal board. If the phases do not match, the
compressor will rotate in reverse and will not be able to
compress.
WARNING
Disconnect switch for over current protection given in
the table below is to be installed between the indoor
unit and the outdoor unit.
Disconnect switch
20A
Lock
nut
Inter-unit line
Power supply
Hook
(3 places)
Direction of
the service
panel removal
Service cover
Power supply
cord or connec-
tion cord
Earth wire
1-9
/16
” (
40
mm
)
or more
Power supply line
G
1
2
3
4
1
2
3 L1 L2
G
G
Earth screw
Earth screw
Earth screw
Disconnect switch
Indoor unit
terminal block
Outdoor unit
terminal block
NOTE:
Factory installed protective inline fuses for indoor units’ conductors
are installed on the Power Supply PCB.
Valve cover removal.
• Remove the one mounting screw.
• Remove the valve cover by sliding upward.
Valve cover
Hook (4 places)
WARNING
Use ring terminals and tighten the terminal screws to the specified torques, otherwise, abnormal overheating
may be produced and possibly cause heavy damage inside the unit.
Match the terminal block numbers and connection cord colors with those of the outdoor unit. Erroneous wir-
ing may cause burning of the electric parts.
Connect the connection cords firmly to the terminal block. Imperfect installation may cause a fire.
Always fasten the outside covering of the connection cord with the cord clamp. (If the insulator is chafed,
electric leakage may occur.)
Securely earth the power cord plug.
Do not use the earth screw for an external connector. Only use for interconnection between two units.
(1) Use ring terminals with insulating sleeves as shown in the
figure below to connect to the terminal block.
(2) Securely clamp the ring terminals to the wires using an
appropriate tool so that the wires do not come loose.
(3) Use the specified wires, connect them securely, and fasten
them so that there is no stress placed on the terminals.
(4) Use an appropriate screwdriver to tighten the terminal screws.
Do not use a screwdriver that is too small, otherwise, the screw
heads may be damaged and prevent the screws from being
properly tightened.
(5) Do not tighten the terminal screws too much, otherwise, the
screws may break.
(6) See the table below for the terminal screw tightening torques.
HOW TO CONNECT THE WIRE TO THE TERMINALS
1. CONNECTION PIPES
Outdoor unit
(1) Detach the caps and plugs from the pipes.
(2) Centering the pipe against port on the outdoor unit, turn the
flare nut with your hand.
2. VACUUM
(1) Remove the cap, and connect the gauge manifold and the vacuum pump to the charging valve by the service hoses.
(2) Vacuum the indoor unit and the connecting pipes until the pressure gauge indicates -0.1 MPa (-76 cmHg).
(3) When -0.1 MPa (-76 cmHg) is reached, operate the vacuum pump for at least 60 minutes.
(4) Disconnect the service hoses and fit the cap to the charging valve to the specified torque.
(5) Remove the blank caps, and fully open the spindles of the 2-way and 3-way valves with a hexagon wrench [Torque: 6~7 N·m (60 to 70
kgf·cm)].
(6) Tighten the blank caps of the 2-way valve and 3-way valve to the specified torque.
3. ADDITIONAL CHARGE
Refrigerant suitable for a piping length of 66ft(20m) is
charged in the outdoor unit at the factory.
When the piping is longer than 66ft(20m), additional
charging is necessary.
For the additional amount, see the table below.
4. GAS LEAKAGE INSPECTION
Tightening torque
M4 screw
1.2 to 1.8 N·m (12 to 18 kgf·cm)
M5 screw
2.0 to 3.0 N·m (20 to 30 kgf·cm)
Ring terminal
Strip
3/8” (10 mm)
Sleeve
Ring terminal
Wire
Screw with special washer
Screw with special washer
Ring terminal
Terminal block
Wire
Terminal board
(3) Tighten the flare nut of the connection pipe at the outdoor unit
valve connector.
(4) When the flare nut is tightened properly by your hand, use a
torque wrench to finally tighten it.
Tightening torque
Blank
cap
3/8” (9.52 mm)
20 to 25 N·m (200 to 250 kgf·cm)
5/8” (15.88 mm)
30 to 35 N·m (300 to 350 kgf·cm)
Charging port cap
12.5 to 16 N·m (125 to 160 kgf·cm)
CONNECTING THE PIPE
OUTDOOR UNIT INSTALLATION
CAUTION
Do not purge the air with refrigerants, but use a vacuum pump to vacuum the installation!
There is no extra refrigerant in the outdoor unit for air purging!
Use a vacuum pump and gauge manifold and charging hose for R410A exclusively.
Using the same vacuum for different refrigerants may damage the vacuum pump or the unit.
CAUTION
When moving and installing the air conditioner, do not mix gas other than the specified refrigerant R410A in-
side the refrigerant cycle.
When charging the refrigerant R410A, always use an electronic balance for refrigerant charging (to measure
the refrigerant by weight).
When charging the refrigerant, take into account the slight change in the composition of
the gas and liquid phases, and always charge from the liquid phase side whose composi-
tion is stable.
Add refrigerant from the charging valve after the completion of the work.
If the units are further apart than the maximum pipe length, correct operation cannot be guaranteed.
CAUTION
After connecting the piping, check the all joints for gas leakage with gas leak detector.
When inspecting gas leakage, always use the vacuum pump for pressure. Do not use nitrogen gas.
Piping length
66ft
(20m)
99ft
(30m)
131ft
(40m)
165ft
(50m)
Rate
Additional charge
None 14.2oz
(400g)
1lb 12oz
(800g)
2lb 10oz
(1200g)
0.43oz/ft
(40g/m)
R410A
Liquid
Gas
To prevent gas leakage, coat the flare
surface with alkylbenzene oil (HAB).
Do not use mineral oil.
3-way valve
(Liquid)
3-way valve
(Gas)
Flare nut
Flare nut
Connection pipe
(Liquid)
Connection pipe
(Gas)
Body side
90°
Torque wrench
Holding spanner
Blank cap
Charging port
Cap
Service hose
with valve core
Outdoor unit
3-way valve
Connecting pipe
Hexagon wrench
Use a 3/16” (4 mm)
hexagon wrench.
Lo
Hi
CAUTION
Use a clean gauge mani-
fold and charging hose
for R410A exclusively.
Service hose
Gauge manifold
Vacuum pump
Flare nut tightening torque
Flare nut [in. (mm)]
Tightening torque [lbf·ft (N·m)]
3/8 (9.52) dia.
23.6 to 31.0 (32 to 42)
5/8 (15.88) dia.
46.5 to 55.3 (63 to 75)
9374995462_IM_EN.indd 2
23-Feb-16 08:45:13