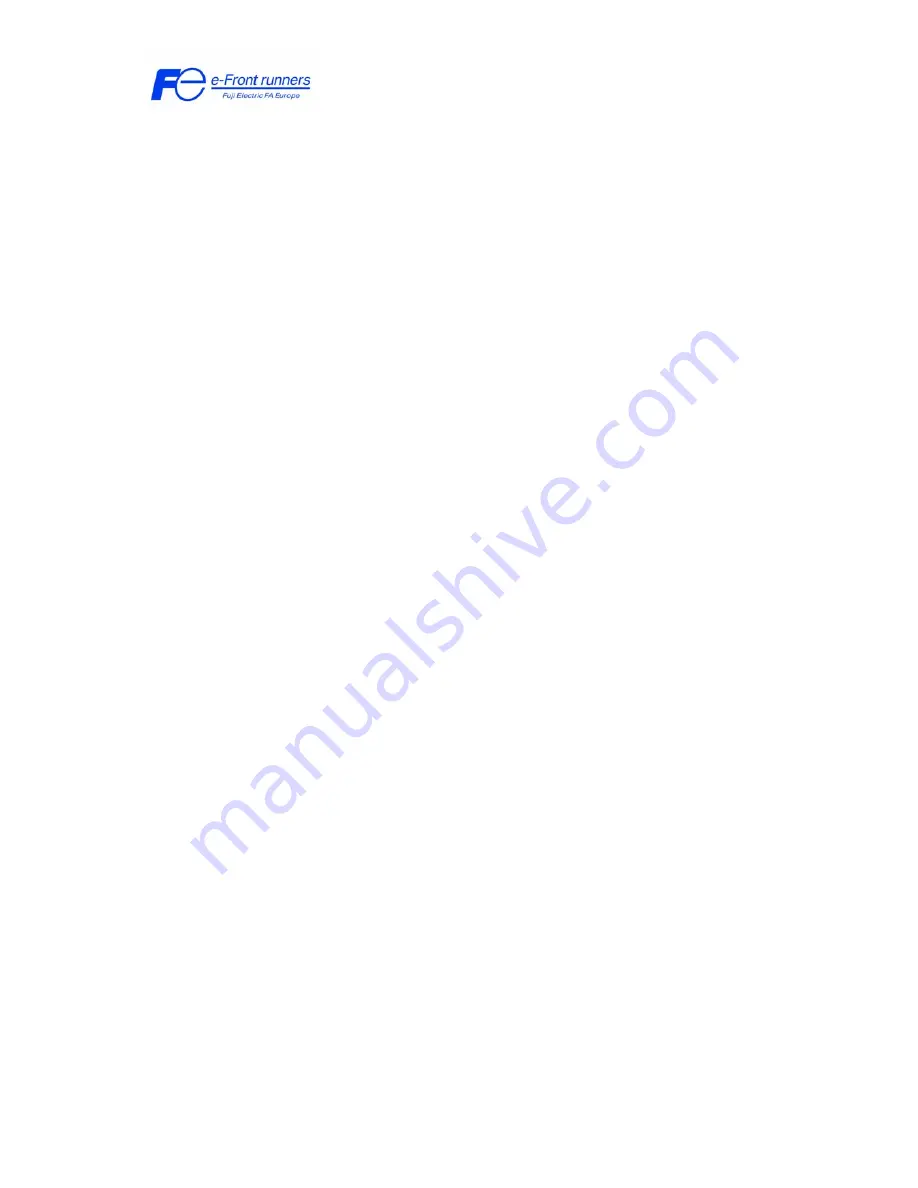
PID SET UP WITH FRENIC Eco series inverter.
9
J17. PID Control (Starting frequency).
Specifies the starting frequency. Select a frequency higher than the slow flowrate
level stop frequency. If the specified starting frequency is lower than the slow flowrate
level stop frequency, the later stop frequency is ignored; the slow flowrate level stop
is triggered when the output of the PID processor drops below the specified starting
frequency.
Factory setting is 0 Hz.
3
rd
Step:
Tuning of the System
•
Set acceleration (function F07) and deceleration times (function F08) of the
inverter as small as possible. Use 1.00 second as starting point.
•
Check that the Frequency Limiter (functions F15, F16) do not obstruct the
operation of the PID controller or the system.
•
Check if the sensor levels and responses are fitted for the application. When
controlling a process up to 8 Bar do not use an 8 Bar sensor but for example a
12 Bar sensor.
•
Try to keep the set-point of the PID to a lower value of its operating range.
This means for example when using 0-10V input, choose a source that has an
output value of 8 Volt at the set value.
•
When setting up a control system make sure the motor has sufficient capacity.
There is no good control when the set value of a compressor is set to 4 Bar
when the maximum achievable pressure of the system is 4 Bar.
•
Measure or estimate the time lag between the process control and the
feedback signal of the process. It is important to anticipate on the time lag of
the process or instability can easily occur. It is important to know this time.
One can determine this time in many ways. One way can be to change the
set-point of the controller and monitor the feedback value for a change. The
time it takes is the time lag of the control loop.
When setting up a PID, we start disabling the I and D action by programming them to
0. Then we set a P value of 1.000 and we operate the inverter. When the process
oscillates we lower the gain of P. When the process does not reach the set-point but
only goes half way of the set-point we can slowly increase the P gain until 80-90% is
achieved. We have to test the response of the system by adding different loads.
When the process starts to oscillate we have to lower the P gain again until a stable
control is achieved. It may be possible that the feedback does not reach the set-point.
This will be solved with the I action of the PID controller. At this moment it is only
important that no oscillation occurs when the load of the process is changed.
When we are sure that the system does not oscillate with the P setting we can start
to optimise the control loop by adding some I action. We could start by entering the
value of the time lag of the process as the I parameter. After this, we have to test if
the system is stable when applying different loads.