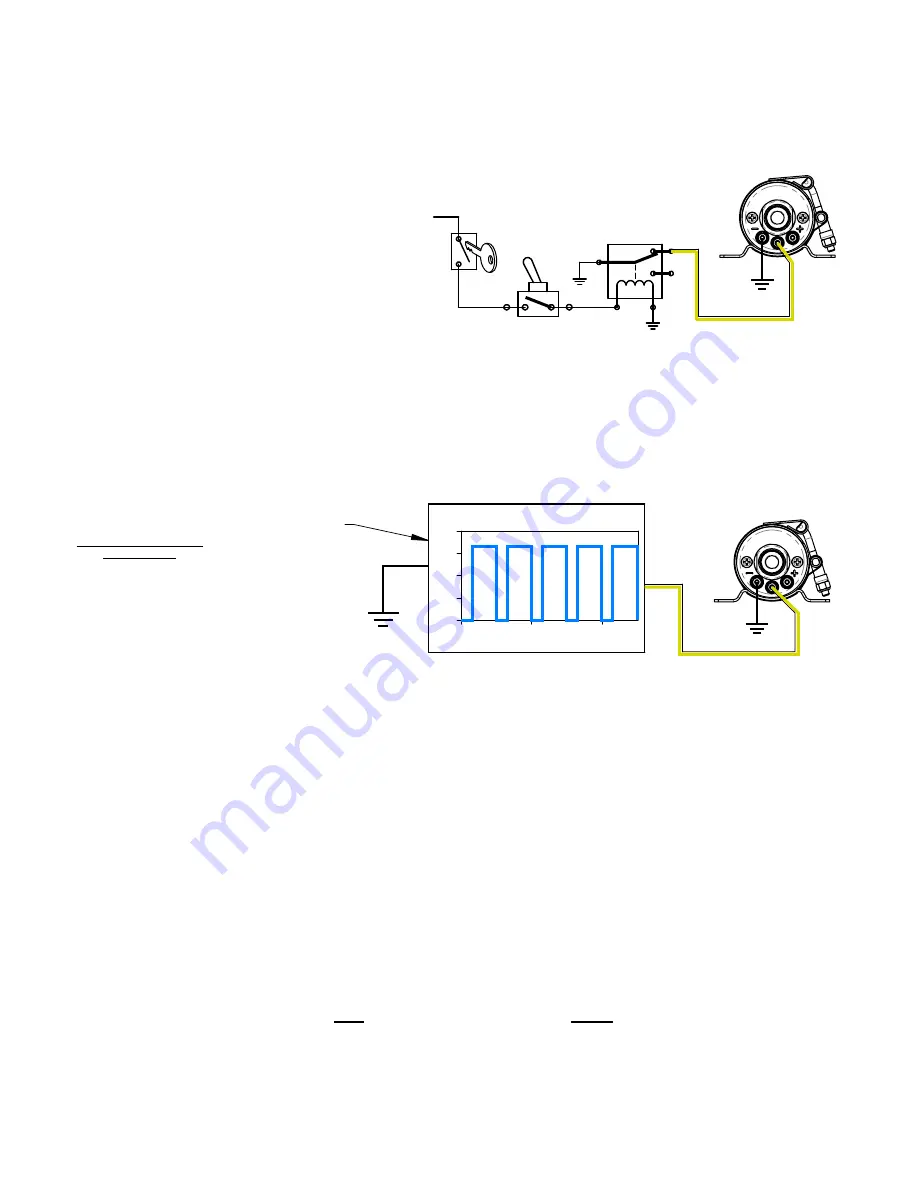
SPEED CONTROL SCHEMATIC DIAGRAMS: (cont.)
Example 4: Switch to Power Speed Changing
When the switching action is in reverse to what can be used as shown Example 3, such as some pressure
switches, the action can be reversed using
a Single Pole Dual Throw (SPDT) relay as
shown to the right. Current draw through
this circuit is extremely low (much less than
1 amp), so a very low current rating for this
relay and switch can be used. Use the
diagram to the right as a guide to properly
wire this example. Reduced speed is
recommended during long periods of low
engine fuel demand conditions to avoid fuel
system heat build-up.
Example 5: Variable Speed
Devices such as an aftermarket ECM can create a pulsed signal (“pulling” voltage to ground at a given
frequency). This signal has a characteristic of dwell time, which is a ratio of on-time vs. off-time (in other words,
the amount of time the signal is “high” vs. “low”). This difference in dwell time percentage will enable the fuel
pump to operate at various speeds or flow rate. A graph demonstrating an example signal created by such a
device is shown below. The example signal is at 66% duty cycle, whereas the amount time that the signal is
above 1.65V voltage is about twice the amount of time at zero volts. When duty cycle is between 5%-20%, the
fuel pump is turned off. A duty cycle between 20%-90% will be variable speed between Minimum and Maximum
Speeds, while duty cycles of 90%-100% are at Full Speed. Frequency range is allowed between 100Hz and
5000Hz. “High” voltage may be as high as the vehicle’s voltage.
Refer to above Example 5, for use with the Fuelab Electronic Fuel Pressure Regulator, Models 52901 and
52902, that creates its own pulsed signal. These regulators automatically control the fuel pump, without the use
of switching means or other components such as described in examples 2 and 3. Refer to instructions for the
Electronic Regulator for proper wiring and installation.
Installation Steps:
1. Disconnect the ground terminal from battery and allow the vehicle’s engine and exhaust system to cool.
Relieve fuel system pressure per applicable service manual. Follow all Warnings, Cautions and Instructions
written on previous pages of these instructions.
2. Modify, remove, or replace other fuel system components as required per established build plan (reference
notes on previous pages and above).
3. Use the supplied brackets attached to the fuel pump, as a drilling template to mark holes for mounting bracket.
Choose a location that minimizes exposure to road hazards and debris, away from engine exhaust pipes, near
fuel tank or cell. Note position and plumbing requirements as stated earlier in these instructions.
4. Install the fuel fittings (not supplied). The threads used on these fuel ports are not tapered or pipe threads. Do
not use Teflon
thread tape or thread sealant on these threads, as this can cause leakage or introduce debris
into the fuel system. Fittings to be used with these style of ports require use of the enclosed -910 o-rings for
proper sealing. Use light oil to lubricate the o-rings just prior to installation. Install the O-rings onto the fuel
fitting first. Position the o-ring in the thread relief of the fitting. Thread fitting into fuel pump and tighten
between 5 and 15 ft
ꞏ
lbs of torque.
ALL
fuel line that is internal to tank
MUST
be fuel compatible both inside
and outside of the line. PTFE based fuel line is recommended for a long service life.
5. Upon installation of fuel tank or cell and installation of all other fuel system components, Inspect fuel system for
any contact of fuel lines or wires with other components that can cause chafing or rubbing. Secure all
components and fuel lines. Ensure that moving components of vehicle are clear.
6. Connect the vehicle’s battery. Perform initial priming: The fuel pump may require priming during initial
operation and for moment after depletion of fuel from fuel tank or cell. This action can be accomplished by
removing fuel line from fuel rail (downstream of fuel pump and filters), allowing the fuel line to empty fluid into
110020271-1, Rev E Sheet 4 of 6
AT REDUCED SPEED
SPDT RELAY
NO
C
SHOWN (OPEN).
NC
WITH SWITCH POSITION
(1+A Rating)
PUMP OPERATES
FROM
FUSED
SOURCE
2
4
-3
Input Signal
(shown right):
* Freq. = 1000Hz
Example Square Wave,
4
3
2
1
0
* 0 to 3.3 Volts
* Dwell Time = 66%
Voltage (v)
0
Electronic Device,
such as Aftermarket
Engine Control Unit
(Oscilloscope-like
displayshown,
representing incoming
speed control signal).
Time (sec X10 )