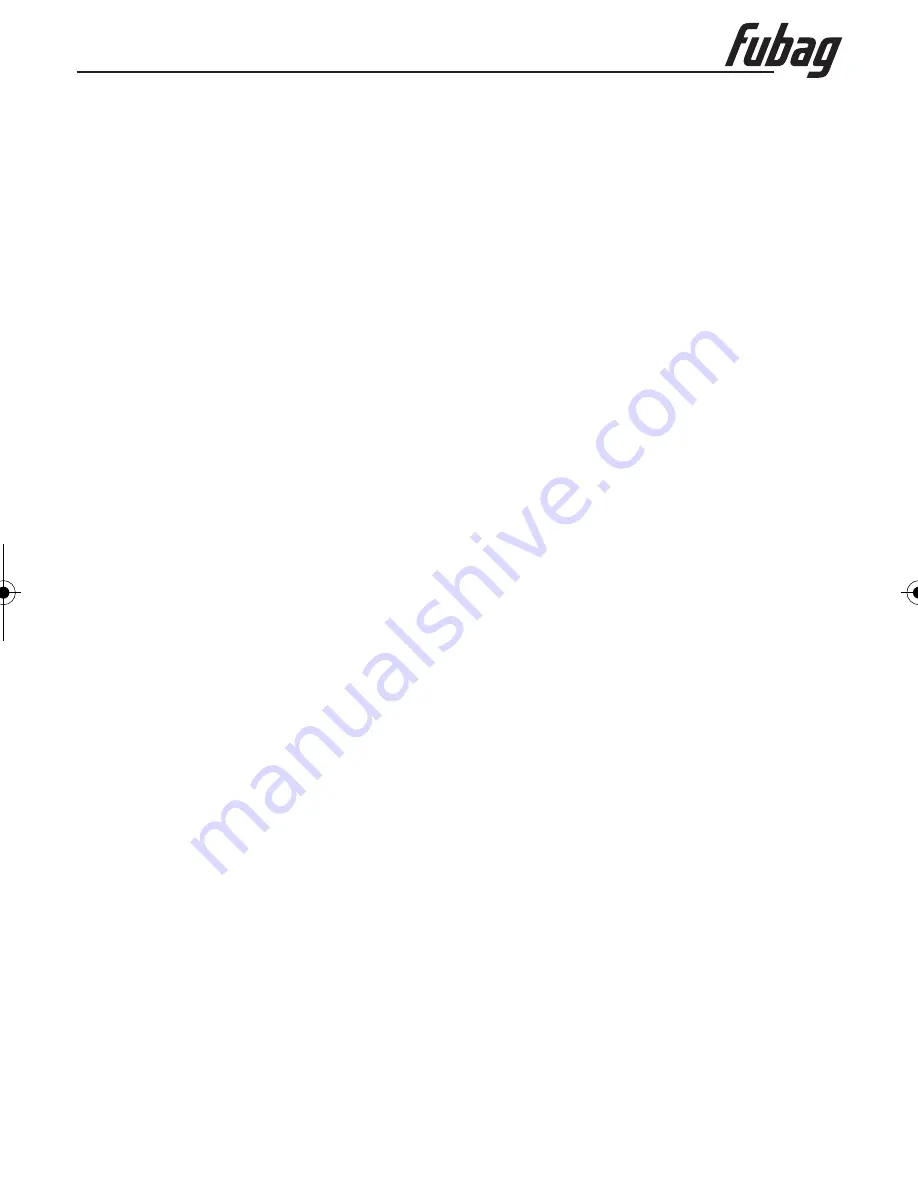
Attention:
- The ‘protection indicator light’ will be on after a long time operation, it shows that the inner
temperature is over the permitted data, then the machine should be stopped using for some time to
let it cool down. It can continue using after the ‘protection indicator light’ is off.
The power source should be switched off after the operation or while temporarily leaving job site.
Welders should dress canvas work cloth and wear welding mask to prevent the hurt from arc and
thermal radiation.
Light separating screen should be put in the job site to prevent the arc will hurt other people.
Inflammable or explosive materials are prohibited to access the job site.
Each connection of the welder should be connected correctly and creditably.
Wire, groove and surrounding 10-20 mm site must be cleaned, no existing rust, greasy dirt, water
and paint etc.
a) Debugging before welding
Install the torch, gas and welding wire, and then turn on the power switch. The power indicator is on
and fan works.
Turn on the gas regulator of gas tank, the gas pressure is shown on the meter
Turn the gas regulator anticlockwise, loose the wire roller, press down the torch switch, and then
adjust the gas flow to meet the technics requirement, and then repress the wire roller
Press the torch switch till the wire extends to the nozzle
When wire feeding, make the cable straight.
When wire feeding, make sure the wire is located on the wire roller groove reliably and the feeding
speed should be smooth. If the wire feeding speed is not smooth, please adjust the tension of the
wire roller.
When using MIG wire, the V groove wire roller should be used.
b) Welding
When welding, please adjust the welding current and welding voltage matchable according to the
set-up
Aim at the welding line, press down the torch switch, the wire feeds automatically. The arc is started
once the wire is touched the work piece. When welding, the “working indicator” is on
a) Debugging before welding
Change the polarity on the vertical board, it is, connect MIG torch lead to “-”, the ground cable lead
to “+”.
Install the torch, gas and welding wire, and then turn on the power switch. The power indicator is on
and fan works.
Press the torch switch till the wire extends to the nozzle
When wire feeding, make the cable straight.
When wire feeding, make sure the wire is located on the wire roller groove reliably and the feeding
speed should be smooth. If the wire feeding speed is not smooth, please adjust the tension of the
wire roller.
When using flux wire, the gear type groove wire roller should be used.
b) Welding
When welding, please adjust the welding current and welding voltage matchable according to the
set-up
Aim at the welding line, press down the torch switch, the wire feeds automatically. The arc is started
once the wire is touched the work piece. When welding, the “working indicator” is on
-
-
-
-
-
-
-
.
-
.
-
.
-
-
-
-
.
-
.
-
-
-
.
-
-
-
-
.
-
.
Work Piece cleaning Before Welding
MIG welding steps
Flux welding steps
www.fubag.ru
O
m
perator's
anual
-
-
10
Summary of Contents for IRMIG 140
Page 13: ...www fubag ru O m perator s anual 12 10 Troubleshooting...
Page 15: ...www fubag ru FUBAG FUBAG 1 14...
Page 16: ...10 40 50 15 1 0 300 www fubag ru 1 5...
Page 18: ...4 220 IGBT 0 10 40 25 55 40 50 20 90 1000 10 4 www fubag ru 17...
Page 19: ...5 S www fubag ru 18...
Page 20: ...www fubag ru 19 6 H 0 7 10 40 50 IP21 X 1 2 I I 1 U 2 U...
Page 21: ...www fubag ru 20 MIG 220 380 1 2 1 5 1 220 IR 140 160 IR 180 200 40 45 30 40 35 45 2 1 5 2 5 2...
Page 22: ...www fubag ru 21 Socket tip...
Page 23: ...1 1 2 3 4 5 6 7 8 9 8 IP21S www fubag ru 22 10 20 1 2 5 6 9 3 4 7 8...
Page 24: ...MIG V b b www fubag ru 23...
Page 25: ...www fubag ru 24 9 2 5 25 55 90...
Page 26: ...www fubag ru 25 10...
Page 27: ...www fubag ru 26 11 12 3 1 1 1 1 1 25 55 90 LIFT O O C C...
Page 28: ...FUBAG 495 641 31 31 info fubag ru www fubag ru...