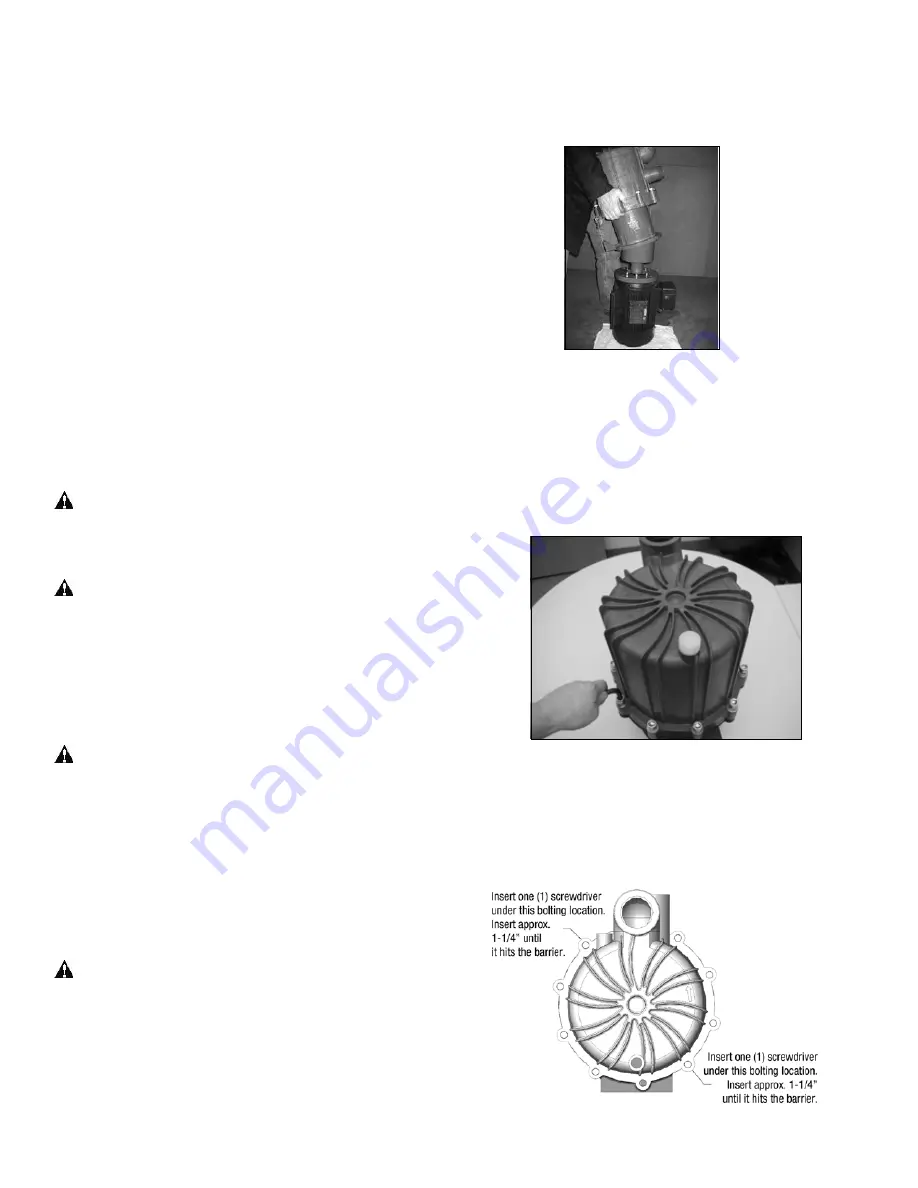
9
Maintenance
Recommended maintenance schedule
The recommended maintenance schedule depends upon the
nature of the fluid being pumped and the specific application
If the pump is used on a clean fluid, it is recommended that the
pump be removed from service and examined after six months
of operation or after 2,000 hours of operation If the pump is
used on fluids with solids, high temperatures or other items that
could cause accelerated wear this initial examination should be
sooner
After the initial examination of the internal components and wear
items are measured, a specific maintenance schedule can be
determined For best results, it is recommended that the pump
be removed from service annually for examination
Section V - Disassembly
Tools Required:
3/8” Allen wrench or ballpoint hex socket, 3/16” Allen wrench,
(2) flat head screw drivers, 10 mm hex socket, metric socket set
(for pumps with IEC outer drives)
WARNING:
Rotating Parts This pump has components that
rotate while in operation Follow local safety standards for
locking out the motor from the power supply during mainte-
nance or service
WARNING:
Chemical Hazard This pump is used for trans-
ferring many types of potentially dangerous chemicals
Always wear protective clothing, eye protection and follow
standard safety procedures when handling corrosive or per-
sonally harmful materials Proper procedures should be
followed for draining and decontaminating the pump before
disassembly and inspection of the pump There may be
small quantities of chemicals present during inspection
WARNING
: Magnetic force hazard This pump should only
be disassembled and assembled using the recommended
procedures The magnetic attraction is powerful enough to
rapidly pull the motor end and the wet end together Do not
place fingers between the mating surfaces of the motor and
wet ends to avoid injuries Keep the drive magnet and
impeller assembly away from metal chips or particles
1 Stop the pump, lock out the motor starter, close all the
valves that are connected to the pump, and drain/decon-
taminate the pump
WARNING:
The pump must be thoroughly flushed of any
hazardous materials and all internal pressure relieved prior
to opening the pump Allow the pump to reach ambient
temperatures prior to performing maintenance
2 Place the pump/motor on the floor with the pump facing
up Remove (4) 1/2” socket head cap screws, lock washers
and flat washers (items 18, 19,
20) securing the pump to the motor Use 3/8” Allen wrench
or 3/8” hex socket on universal joint
3 Firmly grab the motor adapter and pull straight up to disen-
gage the motor and pump See figure 10
For 182, 184, 213, and 215TC motor frame pumps,
make
sure the o-ring (item 12B) does not fall out of the motor
adapter (motor end)
4 Place pump on bench with housing (item 1) facing up Using
a 10 mm hex (Allen) wrench, remove (10) M12 socket head
cap screws, lock washers and flat washers (items 15, 16,
17) See figure 11
Figure 10
Figure 11
Remove the housing (item 1) by carefully inserting two flat
head screwdrivers at the locations shown in Figure 12 Slide
the screwdrivers in at the bolt holes between the metal mot-
or adapter and the housing until they stop
Figure 12