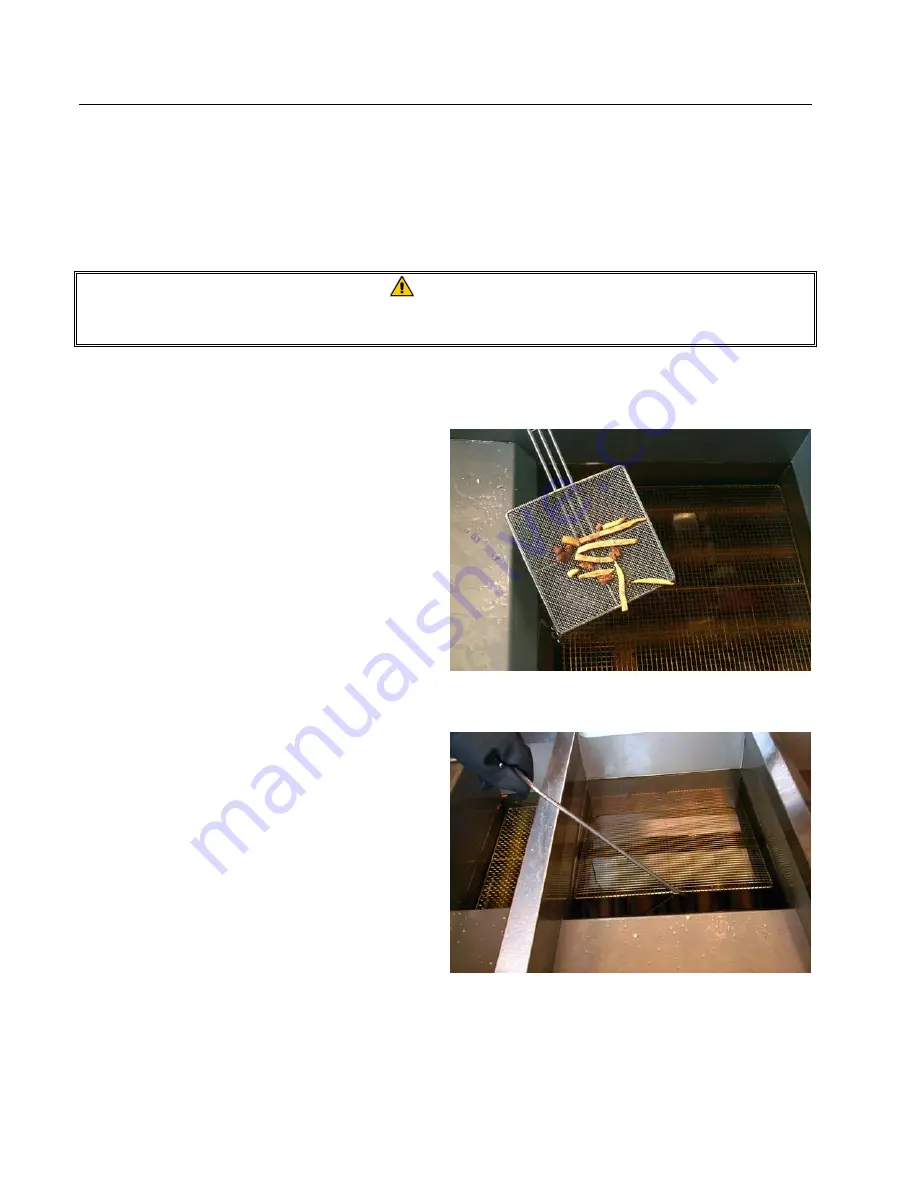
SUFF/UFF FILTRATION SYSTEMS
CHAPTER 3: INSTALLATION AND OPERATION
3-14
3.4 Operating the Filter
3.4.1 Pan Preparation and Operation
See Section 3.2.1,
Assembling the Filter
, and Section 3.2.2,
Installing the Filter
, for the appropriate
filter preparation procedure.
CAUTION
NEVER operate the filter unit unless cooking oil is
at operating temperature (~350°F/ ~177°C).
1.
Ensure the filter pan assembly is prepared as described in Section 3.2.1,
Assembling the Filter
,
and turn fryer off.
2.
Remove fry baskets from frypot and skim any
large debris from the oil. Use extreme
caution, as oil is at or near operating
temperature (~350°F/~177°C).
3.
Remove the support grid from the frypot
using the clean-out rod. Stir the oil with the
frypot/filter brush to suspend debris prior to
draining.
Prior to filtering, skim any large debris from oil in
frypot.
Removing support grid from fry vessel prior to
filtering.