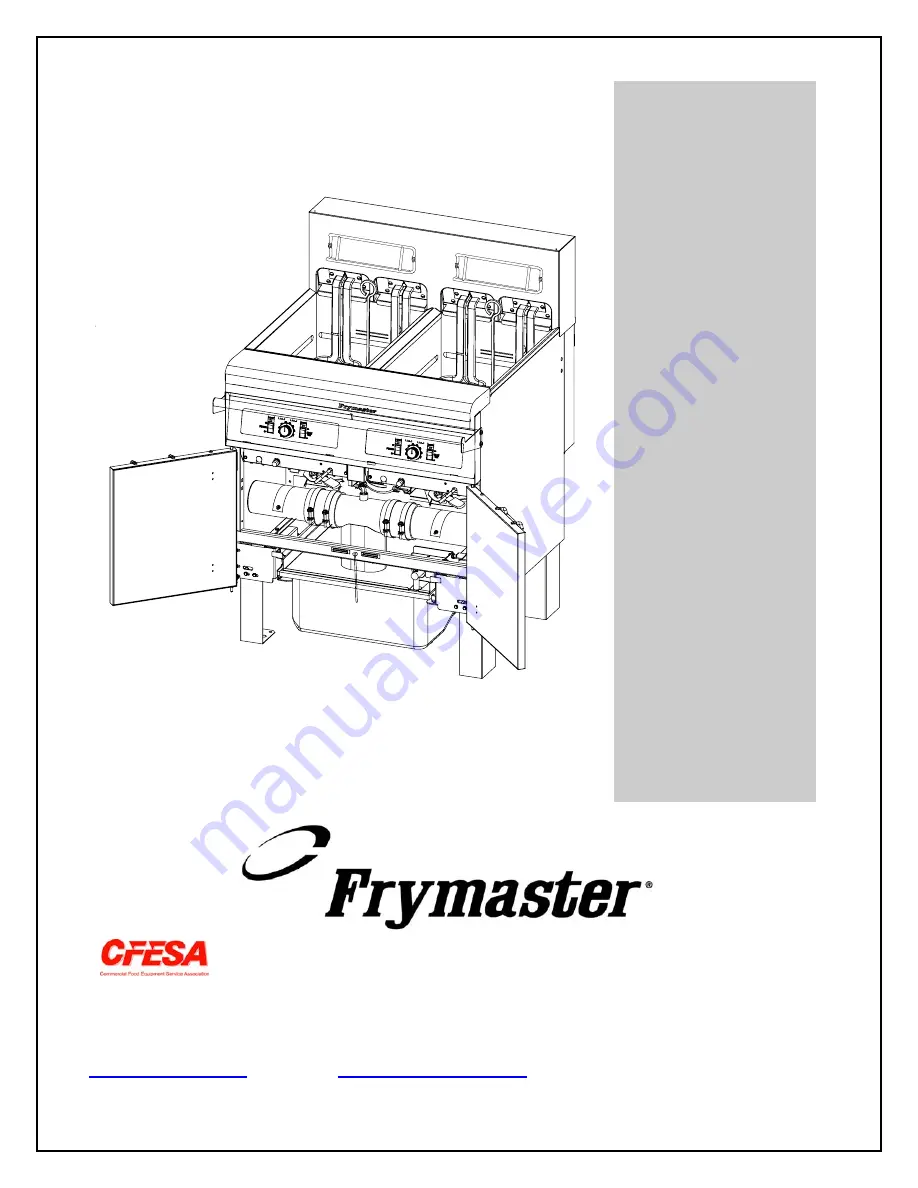
Frymaster, a member of the Commercial Food Equipment Service Association, recommends
using CFESA Certified Technicians.
24-Hour Service Hotline 1-800-551-8633
AUGUST 2005
www.frymaster.com
E-mail:
*8196004*
This manual is applicable to fryers manufactured beginning
August 2003
with serial
numbers beginning with 0308. For serial numbers prior to 0308, refer to manual
819-5184.
NAVY SURFACE SHIP ELECTRIC
FRYERS
Installation, Operation, Service, and Parts Manual
H14S
C/H1
7SC/H22
S
C Sing
le Fryers, FPPH17S
C
a
n
d
FPH17
S
C Series Filtr
a
tion System
Fryers