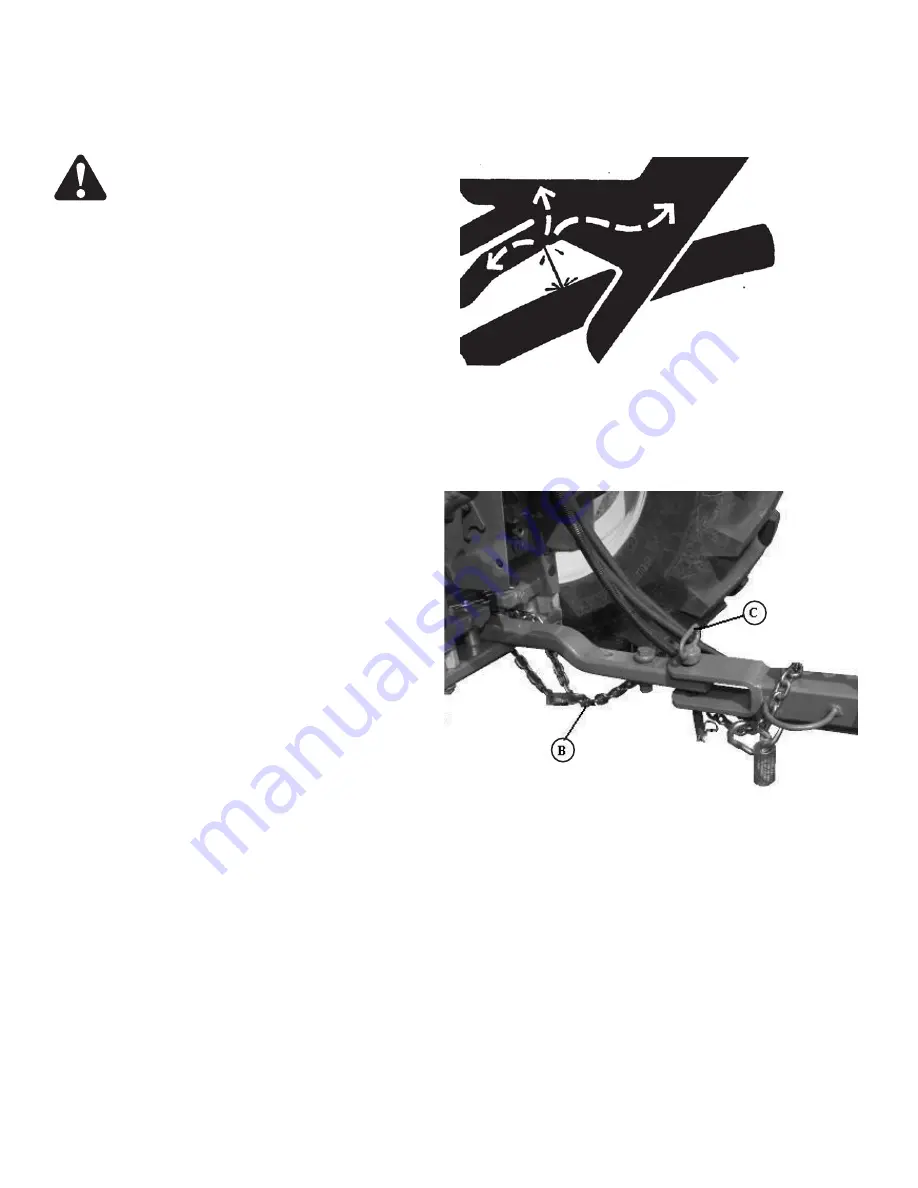
ATTACHING AND DETACHING
CAUTION: Escaping fluid under pressure
can penetrate the skin causing serious
injury. Avoid the hazard by relieving
pressure before disconnecting hydraulic
or other lines. Tighten all connections
before applying pressure.
Search for leaks with a piece of
cardboard.
Protect hands and body from high
pressure fluids.
If an accident occurs, see a doctor
immediately. Any fluid injected into the
skin must be surgically removed within a
few hours or gangrene may result.
Doctors unfamiliar with this type of injury
should reference a knowledgeable
medical source, such information is
available from Deere & Company
Medical Department in Moline, Illinois,
U.S.A.
8. Disconnect hydraulic hoses (A) from tractor
receptacles.
9. Unhook safety chain (B).
10. Remove hitch pin (C).
11. Put tractor SCV levers in the neutral position.
A—Hydraulic Hose
B—Safety Chain
C—Hitch Pin
20
ATTACHING AND DETACHING
Summary of Contents for WR 4106
Page 1: ...O P E R A T O R S M A N U A L OMUS00W41 01 23 09 4106 4109 ...
Page 34: ...33 LUBRICATION AND MAINTENANCE Grease Drawbar Support EVERY 100 HOURS Grease Drawbar Support ...
Page 55: ...SPECIFICATIONS UNIFIED INCH BOLT AND CAP SCREW TORQUE VALUES 54 ...
Page 56: ...SPECIFICATIONS METRIC BOLT AND CAP SCREW TORQUE VALUES 55 ...
Page 57: ...NOTES ...
Page 60: ...MAIN FRAME 58 ...
Page 62: ...DRAWBAR ASSEMBLY 60 ...
Page 64: ...FRONT CRAZY WHEEL AND DIRECTIONAL WHEEL ASSEMBLY 62 ...
Page 66: ...RIGHT HAND FINGER WHEEL 64 ...
Page 68: ...HYDRAULIC LIFT MECHANISM 66 ...
Page 70: ...SMV EMBLEM 68 ...
Page 72: ...RIGHT HAND LIGHT 70 ...
Page 78: ...NOTES ...
Page 79: ...NOTES ...
Page 80: ...PART NO OMUS00W41 ...