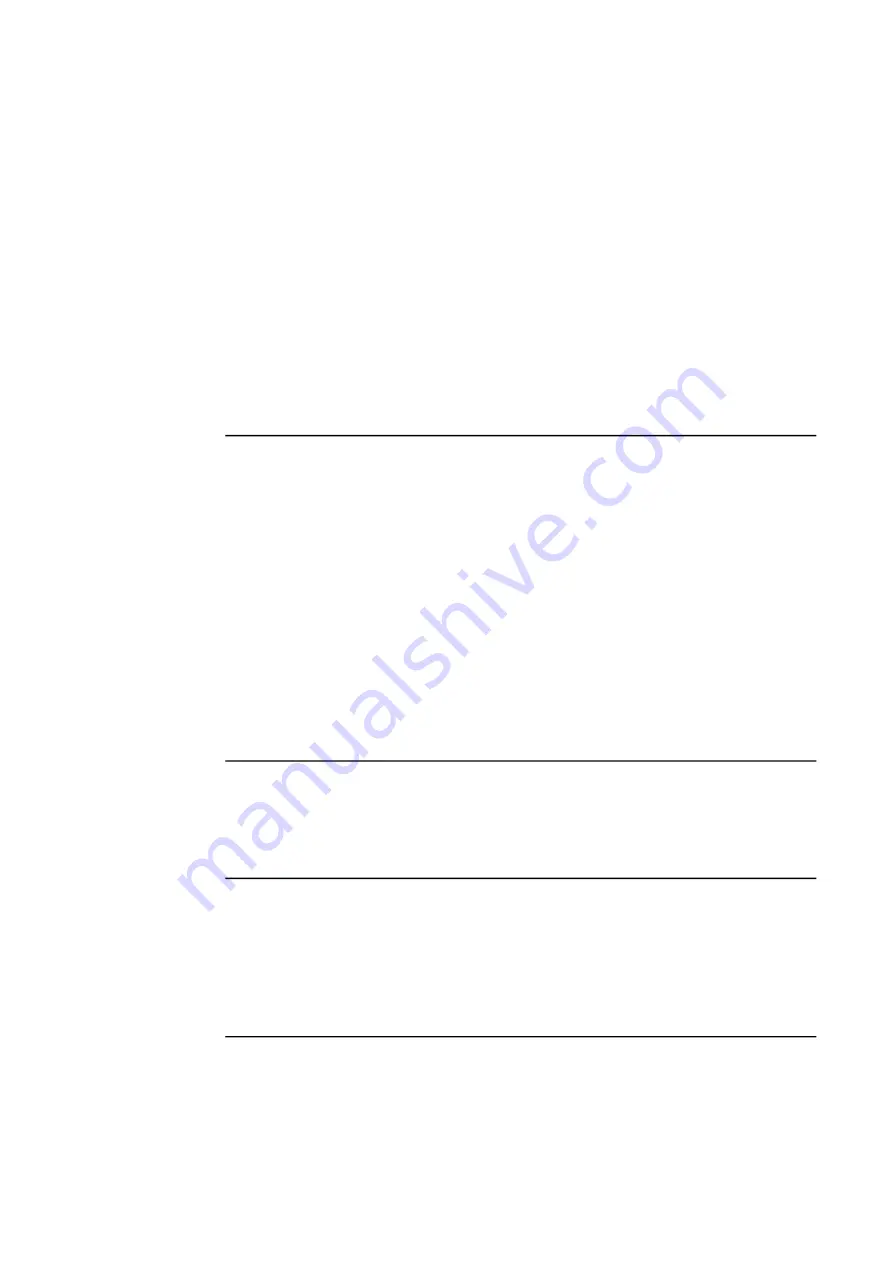
36
No protective gas shield
All other functions are OK
Cause:
Gas cylinder is empty
Remedy:
Change the gas cylinder
Cause:
The gas pressure regulator is faulty
Remedy:
Replace the gas pressure regulator
Cause:
Gas hose is not fitted or is damaged
Remedy:
Fit or change the gas hose
Cause:
Welding torch is faulty
Remedy:
Change the welding torch
Cause:
Gas solenoid valve is faulty
Remedy:
Contact After-Sales Service
Irregular wire feed speed
Cause:
Braking force has been set too high
Remedy:
Loosen the brake
Cause:
Hole in the contact tip is too narrow
Remedy:
Use a suitable contact tip
Cause:
Faulty inner liner in welding torch
Remedy:
Check the inner liner for kinks, dirt, etc. and replace if necessary
Cause:
The feed rollers are not suitable for the wire electrode being used
Remedy:
Use suitable feed rollers
Cause:
Feed rollers have the wrong contact pressure
Remedy:
Optimise the contact pressure
Wirefeed problems
when using long hosepacks
Cause:
Incorrect arrangement of hosepack
Remedy:
Arrange the hosepack in as straight a line as possible, avoid tight bends
Welding torch becomes very hot
Cause:
The specification of the welding torch is inadequate
Remedy:
Observe the duty cycle and loading limits
Cause:
Only on water-cooled systems: Inadequate coolant flow
Remedy:
Check coolant level, coolant flow, for coolant contamination, etc. For further
information refer to the cooling unit operating instructions.
Summary of Contents for VR 5000rob
Page 2: ...2...
Page 4: ...4...
Page 6: ...6 Troubleshooting 34 General 34 Safety 34 Fault diagnosis 34 Technical data 38 VR 5000rob 38...
Page 26: ...26 3 4 5 6 3 4 5 6...
Page 28: ...28 3 4 3 8 6 7 9 3 1 2 2 5 4 4 3 4 5 5 6 1 2 3 4...
Page 39: ...39 EN...