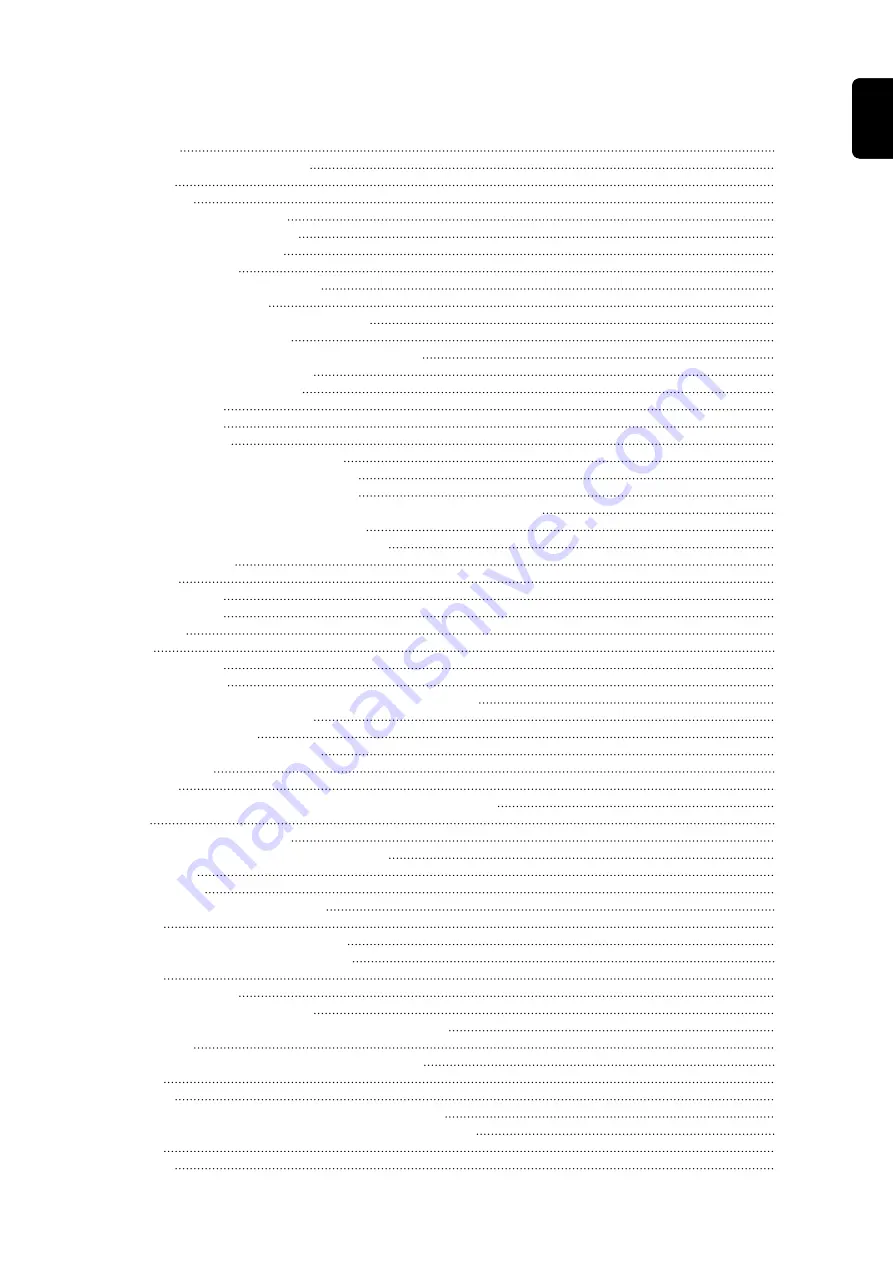
Contents
Protecting yourself and others
Danger from toxic gases and vapours
Risks from mains current and welding current
Requirement for the shielding gas
Danger from shielding gas cylinders
Danger from escaping shielding gas
Safety measures at the installation location and during transport
Safety measures in normal operation
Commissioning, maintenance and repair
Validity of "General Delivery and Payment Conditions"
FK 4000 R, FK 4000 Rob, FK 4000 R FC, FK 4000 R US
FK 4000 R flow sensor with coolant filter
Control elements and connections
Control elements and connections
Before installation and commissioning
Guarantee provisions regarding the coolant pump
Fitting coolant connections to the front of the unit
Fitting coolant connections to the front of the unit
Adapting the cooling unit to the respective mains voltage
3
EN
Summary of Contents for FK 4000
Page 2: ......
Page 40: ...40...
Page 41: ...Troubleshooting 41...
Page 42: ...42...
Page 51: ...51 EN...