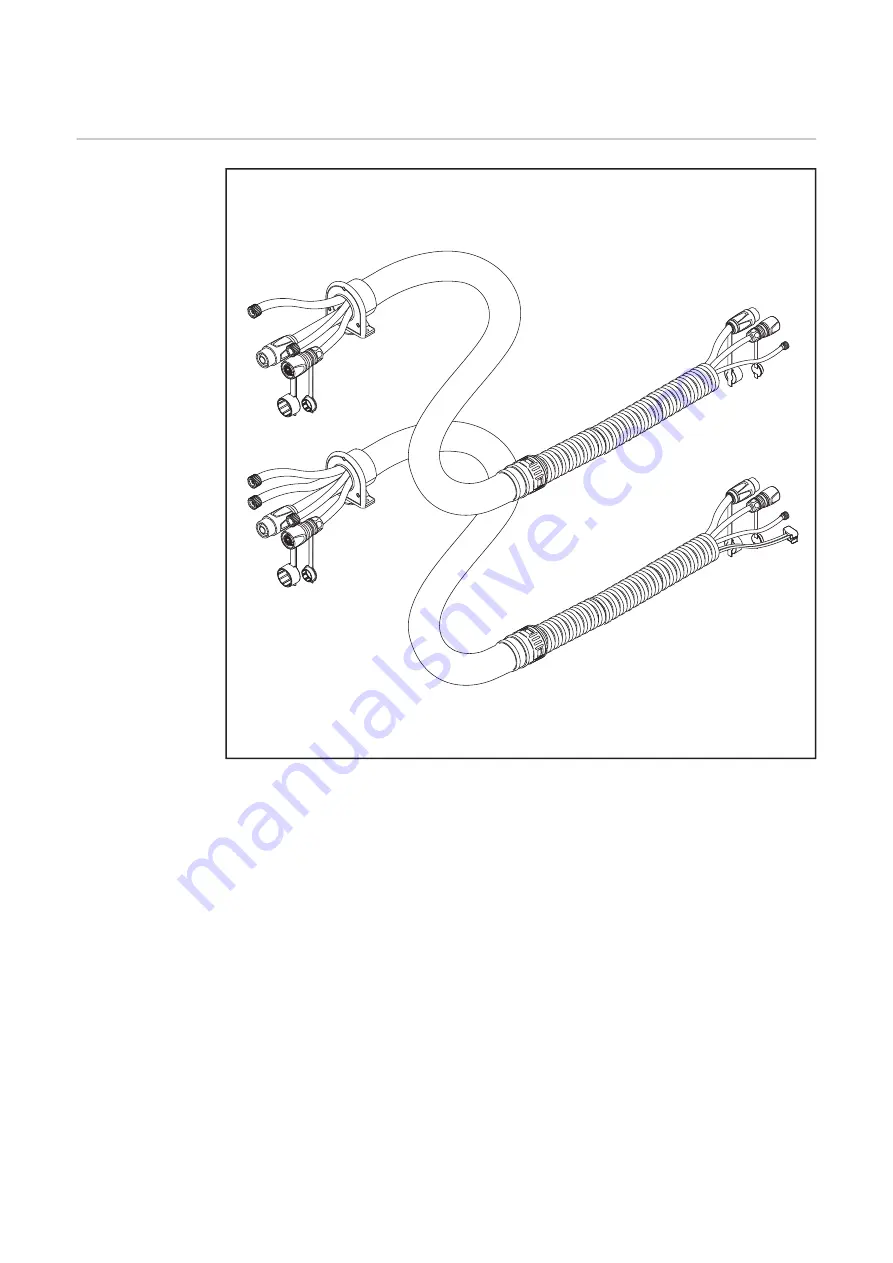
Interconnecting hosepack
Interconnecting
hosepack
G
W
G = gas-cooled interconnecting hosepack, W = water-cooled interconnecting hosepack
The interconnecting hosepacks connect the power sources to the TWIN wirefeeder or
the two robot wirefeeders.
In TWIN welding systems, one water-cooled and one gas-cooled interconnecting hosep-
ack are used.
38
Summary of Contents for CMT Twin
Page 2: ......
Page 18: ...18...
Page 19: ...General information 19...
Page 20: ...20...
Page 30: ...The balancer mounting Y piece can also be used instead of the robot support Y piece 30...
Page 31: ...System components 31...
Page 32: ...32...
Page 44: ...44...
Page 45: ...Welding Technology Aspects 45...
Page 46: ...46...
Page 64: ...64...
Page 65: ...Operating controls connections and mechanical components 65...
Page 66: ...66...
Page 74: ...74...
Page 75: ...Installation and commissioning TWIN Push 75...
Page 76: ...76...
Page 92: ...7 8 9 10 11 12 92...
Page 96: ...1 2 4 1 5 96...
Page 103: ...Installation and commissioning TWIN Push Pull CMT 103...
Page 104: ...104...
Page 126: ...7 8 9 10 11 12 126...
Page 130: ...1 2 4 1 5 130...
Page 137: ...Troubleshooting Maintenance and Disposal 137...
Page 138: ...138...
Page 146: ...146...
Page 147: ...Technical data 147...
Page 148: ...148...
Page 159: ...159 EN US...