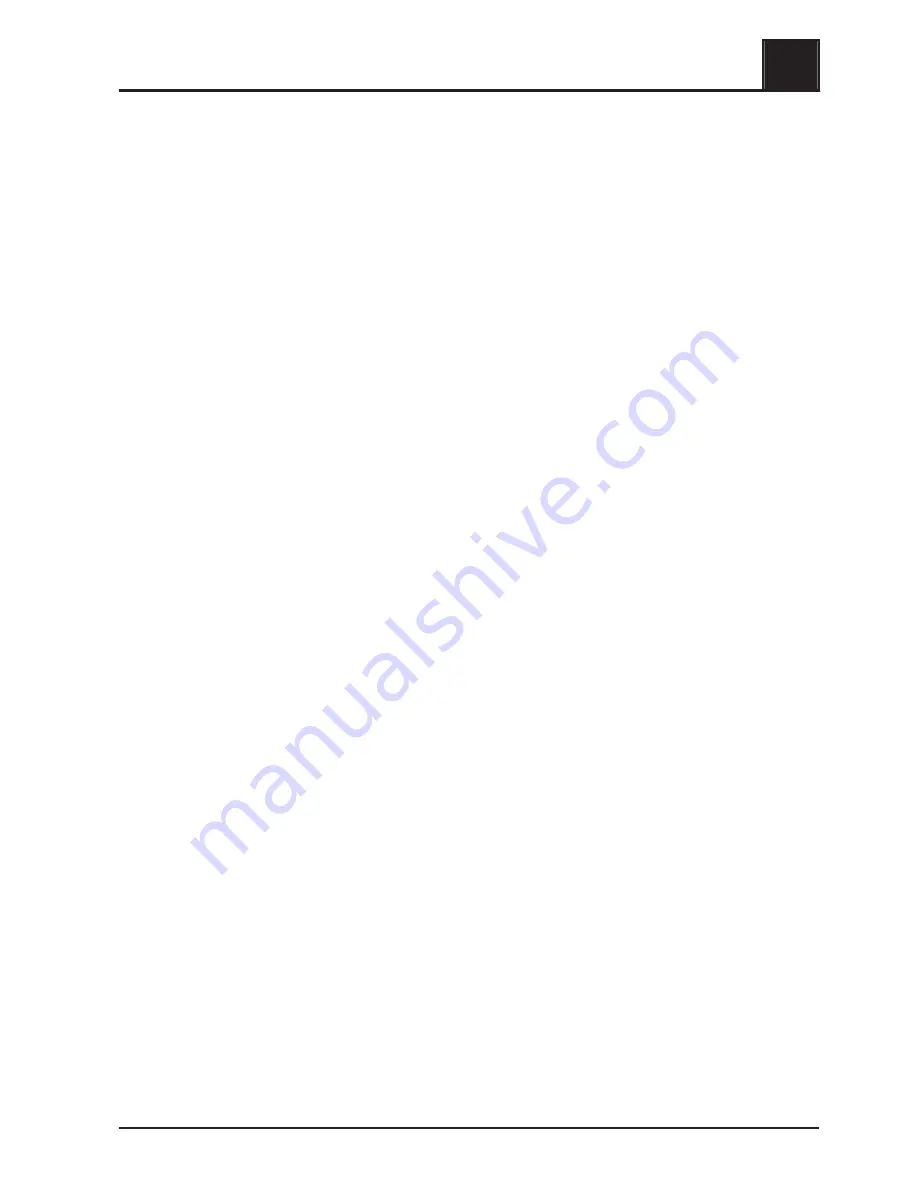
4.1
General information on servicing
28
4.2
Inspection and cleaning
30
4.2.1
Inspection
30
Checking the system pressure
30
Checking the thermal discharge safety device
30
Checking the safety valve
30
Checking the geared motors
30
4.2.2
Cleaning
31
Emptying the combustion chamber ash container
31
Emptying the heat exchanger ash container
33
Cleaning the combustion space and combustion chamber
35
4.2.3
Periodic inspection and cleaning
38
Before starting inspection and cleaning work
39
4.2.4
Periodic inspection and cleaning (approx. 1,000 hrs)
39
Cleaning the ash from the heat exchanger
40
Cleaning the heat exchanger
41
Cleaning the broadband probe
42
Cleaning the flue gas temperature sensor
42
Cleaning the flue gas recirculation (AGR) (optional)
43
Cleaning the area below the step grate
44
Checking the draught controller flap
45
4.2.5
Periodic inspection and cleaning (~3000)
45
Checking the seal on the doors
46
Cleaning the fireclay elements
46
Cleaning the combustion air fan
47
Cleaning the induced draught fan
48
Checking the heat exchanger ash removal drive
48
Checking the combustion chamber overpressure sensor
49
Checking the underpressure controller
49
4.3
Emissions measurement by chimney sweep or regulatory body
50
4.3.1
Measurement at nominal load
50
4.3.2
Measurement at partial load (if necessary)
50
4.4
Maintenance agreement / Customer service
51
4.5
Replacement parts
51
4.6
Disposal information
52
4.6.1
Disposal of the ash
52
4.6.2
Disposal of system components
52
5
Troubleshooting
53
5.1
General fault with power supply
53
5.1.1
Behaviour of system after a power failure
53
5.2
Excessive temperature
53
5.3
Faults with fault message
54
5.3.1
Procedure for fault messages
54
5.3.2
Acknowledging a fault message
54
6
Appendix
55
6.1
Addresses
55
6.1.1
Address of manufacturer
55
6.1.2
Address of the installer
55
Contents
Operating Instructions TX 200-250 | B1060217_en
3