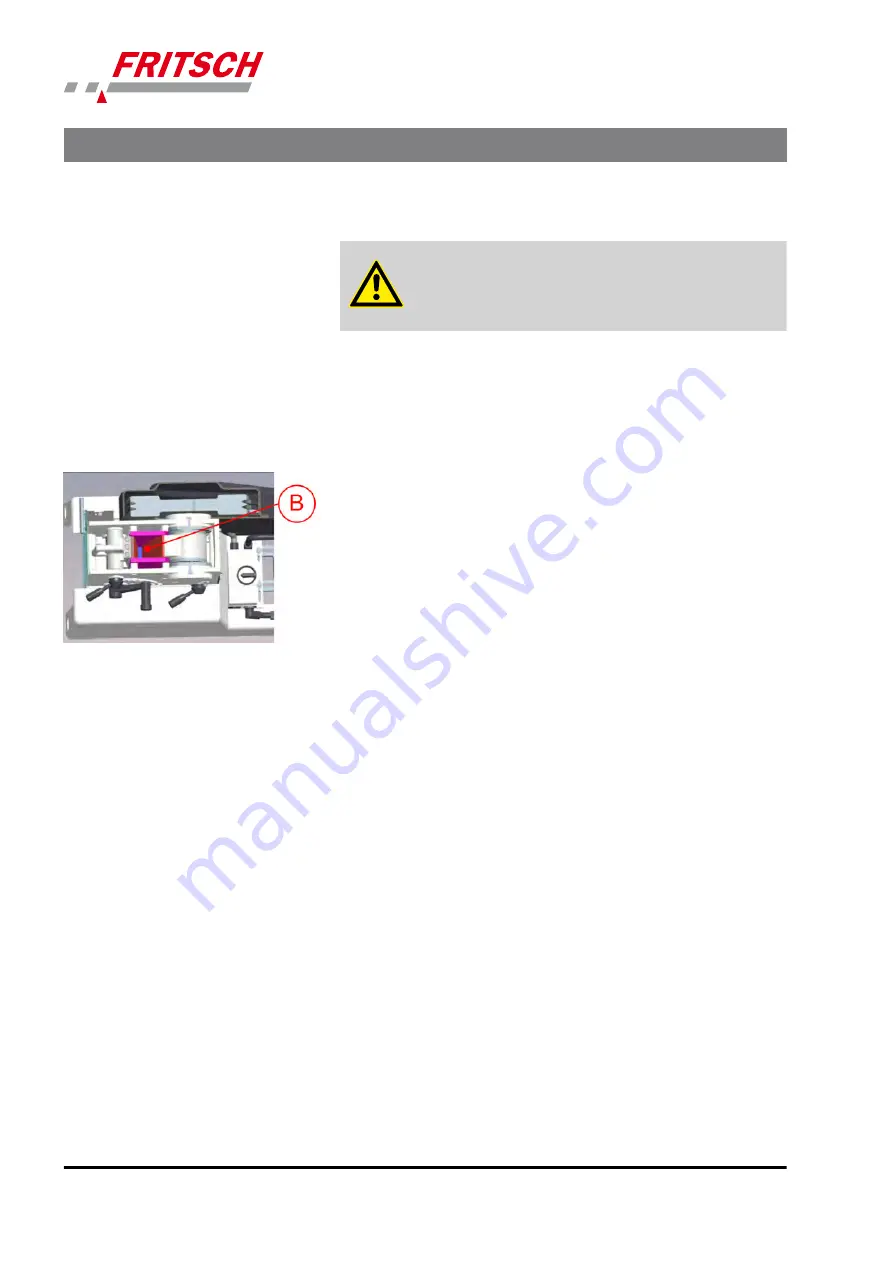
6.1.2 Adding material
CAUTION!
Switch the device on before filling material into the
funnel.
Larger pieces of material should be put into the funnel one piece at a
time:
n
Model I maximum edge length 60 mm,
n
Model II maximum edge length 95 mm,
Only add the rest of the material once the crushing noise becomes
noticeably quieter.
B Crushing chamber
Never fill more material to be crushed into the funnel than the actual
crushing chamber (B) can hold. The upper edges of the support walls and
crushing plates form the border of the crushing chamber at the top.
There should not be any material above these edges. During continuous
operation, only the same quantity may be added that is discharged as
crushed material.
The maximum quantity to be fed depends on the crushing properties of
the material and the selected gap width. Observe the crushing process
(crushing noise) for each new material and determine the optimum
quantity to be fed.
6.1.3 Dust extraction
Dust may form during comminution with small gap widths and accumu-
late in the crushing chamber (B). To stop it from spreading, the PULVERI-
SETTE 1 classic line can be equipped with a vacuum cleaner. See
Chapter 7.1 ‘Conversion for use with the dust exhaust system’
6.1.4 Final fineness
The achievable final fineness depends on the material properties and the
gap setting between the two crushing plates. This gap width, however,
only determines one dimension of the crushed material. That means, for
materials which form platelets when crushed, the proportion of the
pieces with a larger length or area can be significantly decreased by per-
forming a second pass.
When the smallest gap width is set, the mean particle feed size (d
50
) of
the crushed material is approx. 2 mm.
Example: Approx. 80 % of stone crushed with the smallest gap has a final
fineness of < 4 mm.
Using the device
- 24 -