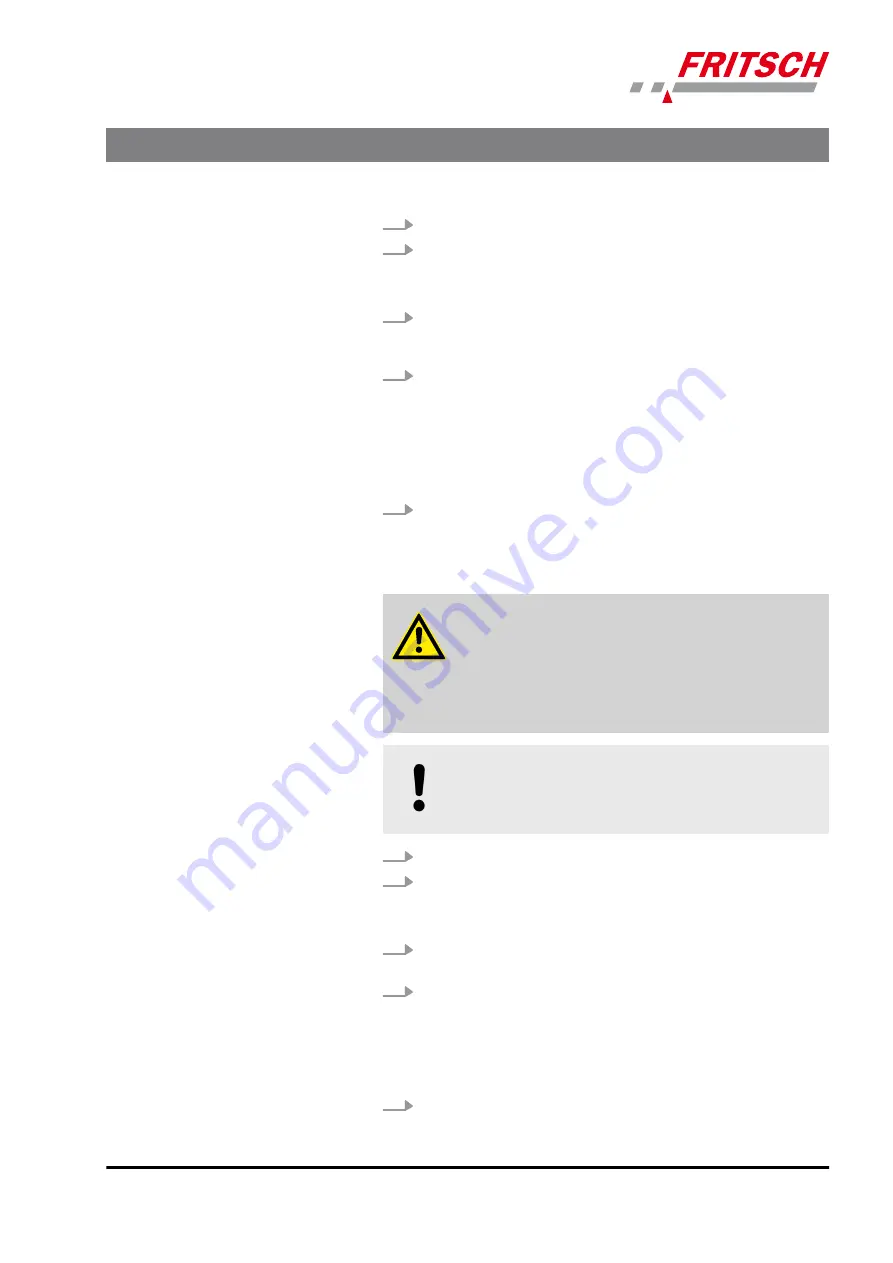
1.
Switch main switch to "0".
2.
Switch the device on at the main switch while holding down the
Stop key.
The device is now in "Setup" mode.
3.
The "Sieving Time" display now shows the default setting "04" for
230 V, "06" for 115 V. The value "07" is preset for a mains voltage
of 100 V (in Japan).
4.
These values can be changed with the "Sieving Time" +/- key and
adapted to the mains voltage.
n
230 V - 04
n
115 V - 06
n
100 V - 07
Save the set values by clicking the stop key.
5.
After making adjustments, switch on the main switch again.
4.5.1.2
Version PRO (valid from serial number 06000) and Version SPARTAN (valid from serial number 05000)
CAUTION!
If the value 01 is set at a voltage of 230V~, it will result
in a defect in the sieve shaker during operation. Failure
to observe this will render void the guarantee, and
releases us from liability for any resulting damage to
the device.
NOTICE!
Only qualified personnel may change the voltage range
on the device!
1.
Switch main switch to "0".
2.
Switch the device on at the main switch while holding down the
Stop key.
The device is now in "Setup" mode.
3.
The "Sieving Time" display now shows the default setting "02" for
230 V, "01" for 115 V.
4.
These values can be changed with the "Sieving Time" +/- key and
adapted to the mains voltage.
n
230 V - 02
n
115 V - 01
Save the set values by clicking the stop key.
5.
After making adjustments, switch on the main switch again.
Installation
- 21 -