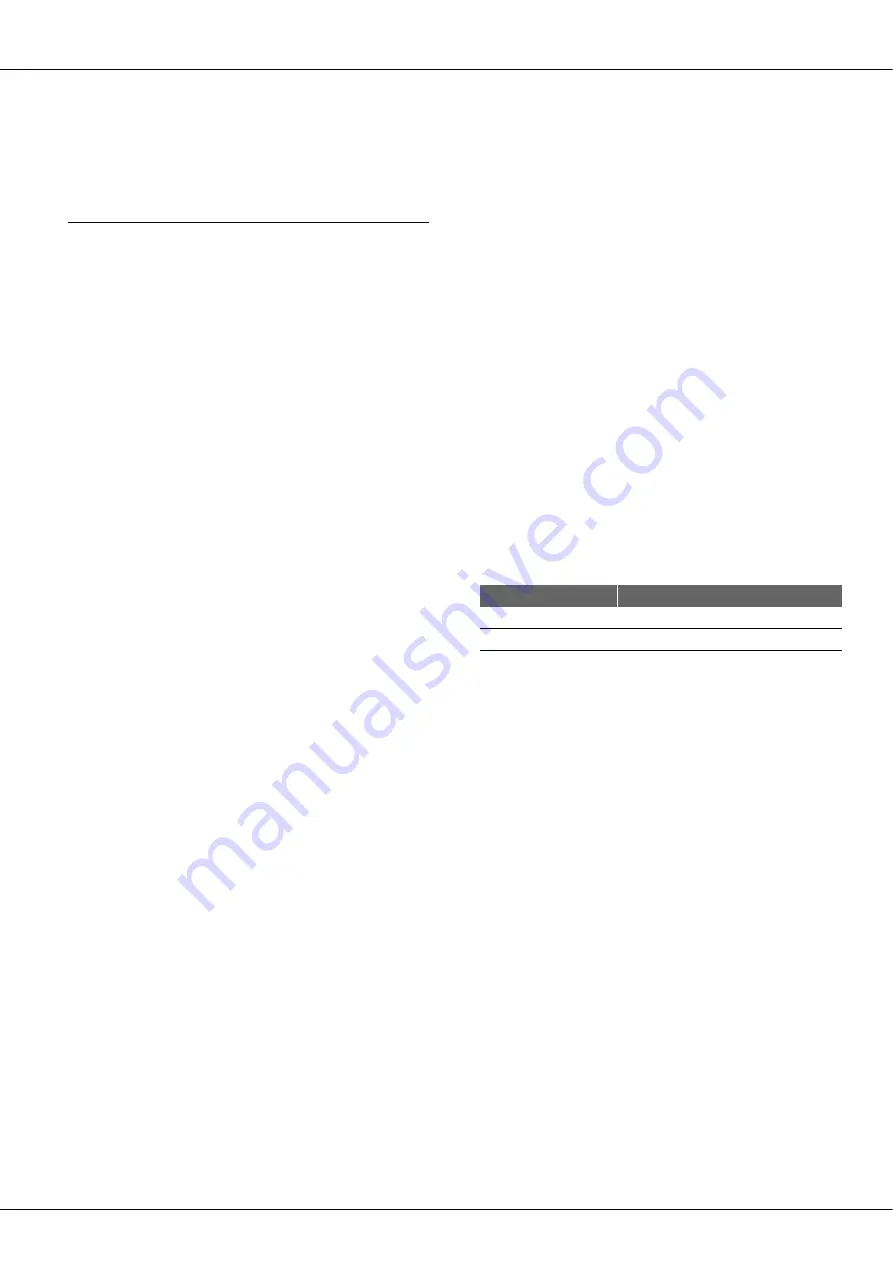
/ / FP PUMP SERIES / / /
14
– A max. pressure of 0.2 bar is allowed for seals to which
sealing fluid is applied without pressure or which are
flushed.
►
The temperature of the sealing liquid is maintained at
T < 70 °C.
1. Open the valve in the suction line.
2. Close the valve in the discharge line.
3. Fill the pump and the suction line up to the upper edge of
the pump with pumping medium. Allow any air pockets that
are present to escape.
4. Turn on the motor. The pump now pumps against the closed
valve in the discharge line. This will limit the starting current.
5. Slowly open the valve in the discharge line and adjust to the
working point.
7.3
Monitoring of Operation
During operation heed the following points:
►
Damage to shaft seal: Regulation of the pump output via the
suction-side valve can lead to damage of the pump and the
shaft seals. Regulate the pump output only by means of the
discharge-side valve.
►
Damage to pumping medium: If during operation the valve
in the discharge line is closed abruptly or for a long period of
time, water hammers can occur in the pump and lead to
damage to the pump and/or the pumping medium. During
operation do not close the valve in the discharge line
abruptly or for a long period of time.
►
Damage to pump: Exceeding of the output can lead to
damage of the pump and the shaft seals. Do not exceed the
maximum speed of 3,600 rpm.
►
Damage to motor during operation with frequency
converter: If the speed is too low, the motor will overheat.
Please refer to the motor supplier documentation in the
attached documents.
7.4
Stopping of Operation
1. Turn off the motor.
2. Close the valve in the suction line to prevent dry running of
the pump.
3. Close the valve in the discharge line.
7.5
Pump Decommissioning
1. Turn off the motor.
2. Close the valve in the suction line.
3. Close the valve in the discharge line.
4. De-energize the pump.
5. Empty the pump.
6. Clean the pump.
7. Dry the pump.
8. Protect the interior of the pump from moisture, e.g., with sili-
ca gel.
9. Seal the pipe connections with caps to prevent penetration
of dirt and foreign objects.
10. Please see
for additional steps.
7.6
Cleaning in Place
7.6.1
CIP Process
The FP series pumps are suitable for the CIP (Cleaning In Place)
process. The following guidelines apply to the CIP process:
Example of a Cleaning Cycle
1. Perform preliminary flush with water.
2. Perform caustic flush with lye (NaOH; see
3. Perform intermediate flush with water.
4. Perform acid flush with nitric acid (HNO
3
; see
).
5. Flush with water.
The pump's differential pressure should be 2–3 bar so that
adequate flow rates are reached.
If values deviate from these specifications, please contact
Fristam
.
7.6.2
SIP Process
The FP series pumps can only be used with the SIP (Sterilization
In Place) process with the prior approval of
Fristam
.
Suitability depends on the selected elastomers.
The maximum process temperature is 145°C.
In ATEX operation, temperatures might deviate, see
supplementary ATEX manual, "
Temperature limits
".
8
Faults
For information on faults, possible causes, and remedies, please
see
Chapter 10.3, "Troubleshooting Table," page 29
Medium
Process Temperature [°C]
NaOH (approx. 1%–2%)
80–85
HNO3 (approx. 1%)
60–65
Table 2
CIP cleaning