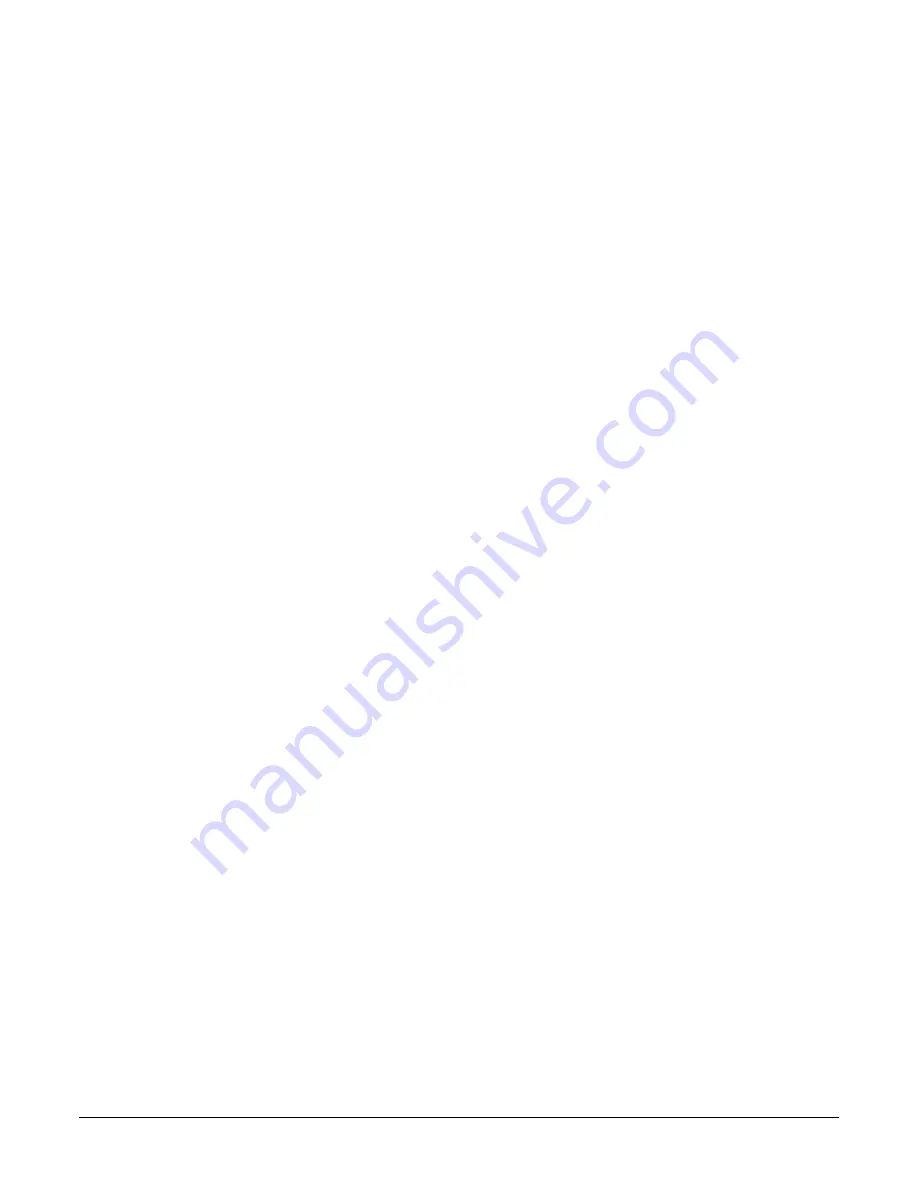
2.4.2 EVAPORATOR
1. Remove the cabinet.
2. Discharge the refrigerant by using a refrigerant
recovery system.
3. Remove the air guide upper. (Refer to Section
2.2.1)
4. After discharging the refrigerant completely,
unbraze the interconnecting tube at the condenser
connections.
5. Remove the evaporator.
6. Re-install by referring to the procedures above.
2.4.3 CAPILLARY TUBE
1. Remove the cabinet.
2. Discharge the refrigerant by using a refrigerant
recovery system.
3. Remove the air guide upper. (Refer to Section
2.2.1)
4. After discharging the refrigerant completely,
unbraze the interconnecting tube of the capillary
tube.
5. Remove the capillary tube.
6. Re-install by referring to the procedures above.
NOTES
Replacement of the refrigeration cycle.
1. When replacing the refrigerating cycle, be sure to
discharge the refrigerant by using a refrigerant
recovery system.
2. After discharging the unit completely, remove the
desired components, and unbraze the pinch-off
tubes.
3. Solder service valves into the pinch-off tube ports,
leaving the valves open.
4. Solder the pinch-off tubes with service valves.
5. After completing the above procedures, the valve
must be closed and left in place on the system for
any subsequent procedures.
6. Evacuate as follows:
6-1. Connect the vacuum pump, as illustrated in
figure 21A.
6-2. Start the vacuum pump. Slowly open manifold
valves A and B with two full turns counter-
clockwise and leave the valves closed.
The vacuum pump is now pulling through
valves A and B up to valve C by means of
manifold and the entire system.
CAUTION :
If high vacuum equipment is used,
just crack valves A and B for a few minutes, then
open slowly with the two full turns counter-clock-
wise. This will keep oil from foaming and being
drawn into the vacuum pump.
6-3. Operate the vacuum pump for 20 to 30 min-
utes, until 600 micron vacuum is obtained.
Close valves A and B and observe vacuum
gauge for a few minutes.
A rise in pressure would indicate a possible
leak or moisture remaining in the system.
With valves A and B closed, stop the vacuum
pump.
6-4. Remove the hose from the vacuum pump and
place it on the charging cylinder. See figure
23B. Open valve C.
Discharge the line at the manifold connection.
6-5. The system is now ready for final charging.
7. Recharge as follows:
7-1. Rotary compressor systems are charged from
the high-side. If the total charge cannot be put
in the high-side, the balance will be put in the
suction line through the access valve which is
installed as the system is opened.
7-2. Connect the charging cylinder as shown in fig-
ure 21B. With valve C open, discharge the
hose at the manifold connection.
7-3. Open valve A and allow the proper charge to
enter the system. Valve B is still closed.
7-4. If more charge is required, the high-side will
not take it. Close valve A.
7-5. With the unit running, open valve B and add
the balance of the charge.
a. Do not add the liquid refrigerant to the low-
side.
b. Watch the low-side gauge, allow pressure to
rise to 30 lbs.
c. Turn off valve B and allow the pressure to
drop.
d. Repeat steps B and C until the balance of
the charge is in the system.
7-6. When the unit is operating correctly, use the
pinch-off tool with the unit still running and the
clamp on the pinch-off tube. Using a tube cut-
ter, cut the pinch-off tube about 2 inches from
the pinch-off tool. Use sil-fos solder and solder
the pinch-off tube closed. Turn off the unit,
allow setting for a while and then test the leak-
age of the pinch-off connection.
- 10 -
Copyright ©2008 LG Electronics. Inc. All right reserved.
Only for training and service purposes
LGE Internal Use Only