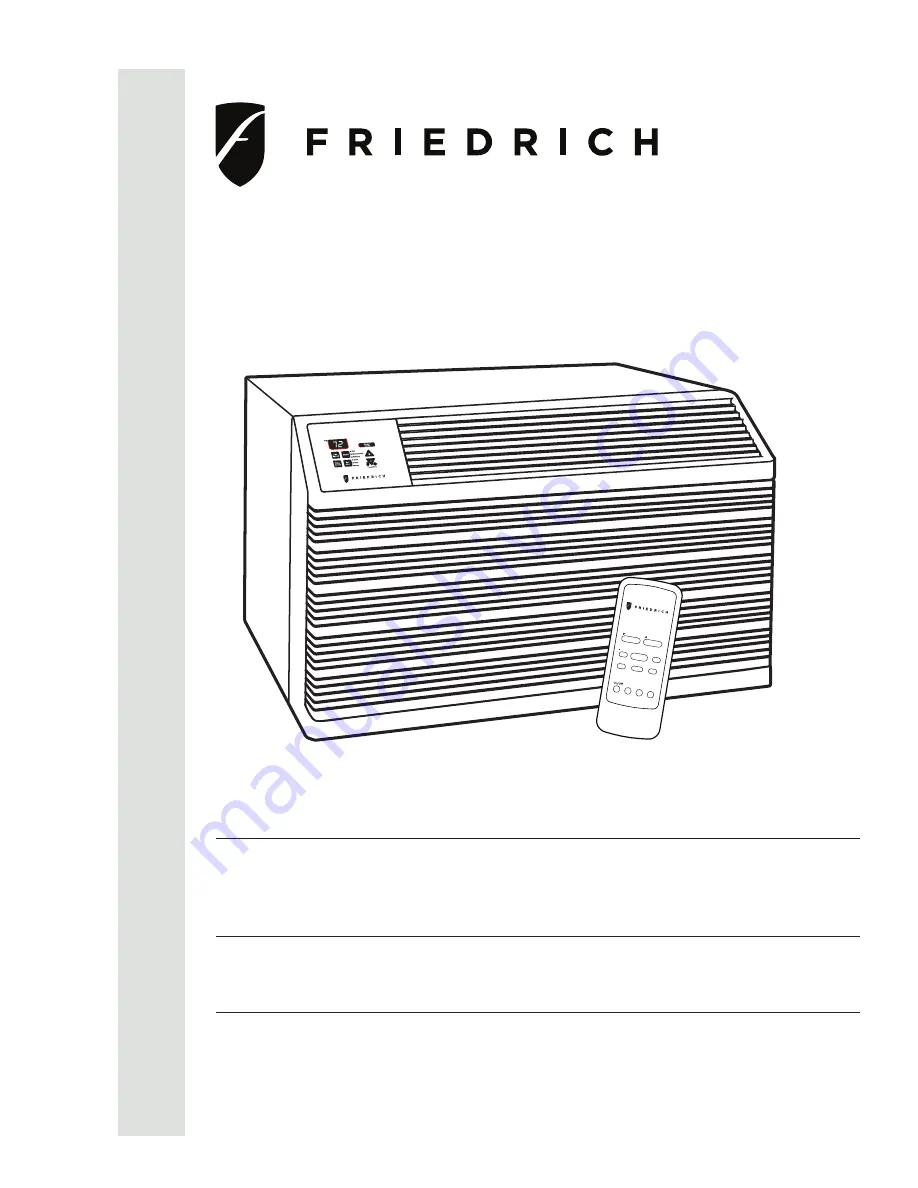
WM-ServMan (4-10)
WallMaster
®
R-410A Models
2 0 1 0
Service Manual
115-Volt: WS08C10A, WS10C10A, WS12C10A
230-Volt: WS10C30A, WS13C30A, WS15C30A
Cool Only
115-Volt: WE10C33A, WE13C33A, WE15C33A
Cool with Electric Heat
230-Volt: WY09C33A, WY12C33A
Heat Pump with Electric Heat Back Up
WallMaster
Money
Fan
Timer Operation
Set Hr.
Stop
Start
Temperature
Fan
Cool
Power
Cooler
Warmer
Only
Speed
Saver
®
Heat
Air Conditioners and Heat Pumps
Thru-the-wall
Summary of Contents for WallMaster WE10C33-A
Page 43: ...WALLMASTER WIRING DIAGRAM ELECTRONIC CONTROL COOL ONLY MODELS 42...
Page 44: ...WALLMASTER WIRING DIAGRAM ELECTRONIC CONTROL COOL WITH ELECTRIC HEAT MODELS 43...
Page 45: ...WALLMASTER WIRING DIAGRAM ELECTRONIC CONTROL HEAT PUMP WITH ELECTRIC HEAT MODELS 44...
Page 58: ...NOTES...
Page 59: ...NOTES...