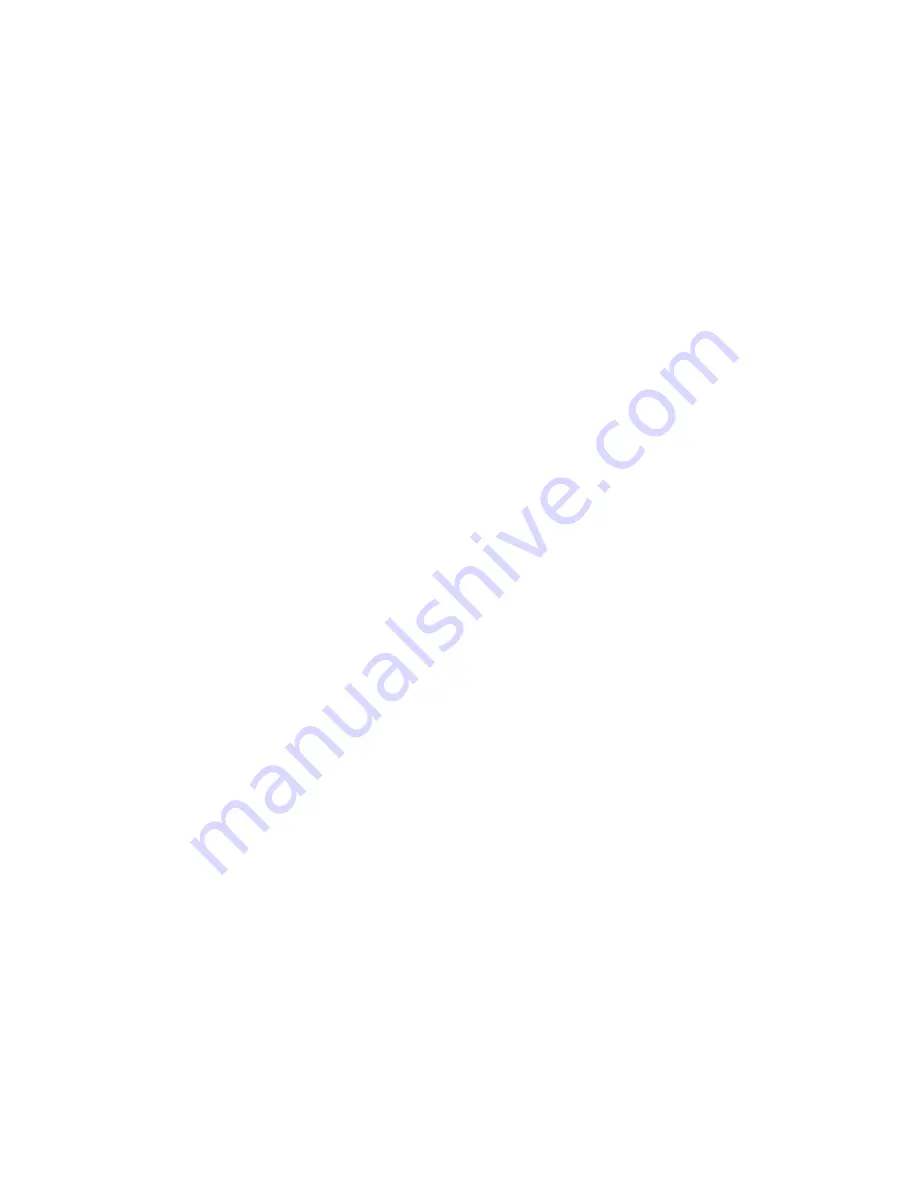
13
10.
Evacuate system to maximum absolute holding pres-
sure of 200 microns or less. NOTE: This process can
be speeded up by use of heat lamps, or by breaking
the vacuum with refrigerant or dry nitrogen at 5,000
microns. Pressure system to 5 PSIG and leave in
system a minimum of 10 minutes. Release refriger-
ant, and proceed with evacuation of a pressure of
200 microns or less.
11.
Break vacuum by charging system from the high side
with the correct amount of refrigerant specifi ed. This
will prevent boiling the oil out of the crankcase.
NOTE: If the entire charge will not enter the high
side, allow the remainder to enter the low side in
small increments while operating the unit.
12.
Restart unit several times after allowing pressures
to stabilize. Pinch off process tubes, cut and solder
the ends. Remove pinch off tool, and leak check the
process tube ends.
SPECIAL PROCEDURE IN THE CASE OF MOTOR
COMPRESSOR BURNOUT
1.
Recover all refrigerant and oil from the system.
2.
Remove compressor, capillary tube and fi lter drier
from the system.
3.
Flush evaporator condenser and all connecting
tubing with dry nitrogen or equivalent, to remove
all contamination from system. Inspect suction and
discharge line for carbon deposits. Remove and
clean if necessary.
4.
Reassemble the system, including new drier strainer
and capillary tube.
5.
Proceed with processing as outlined under hermetic
component replacement.
ROTARY COMPRESSOR SPECIAL
TROUBLESHOOTING AND SERVICE
Basically, troubleshooting and servicing rotary compres-
sors is the same as on the reciprocating compressor with
only a few exceptions.
1.
Because of the spinning motion of the rotary, the
mounts are critical. If vibration is present, check the
mounts carefully.
2.
The electrical terminals on the rotary are in a differ-
ent order than the reciprocating compressors. The
terminal markings are on the cover gasket. Use your
wiring diagram to insure correct connections.
REFRIGERANT CHARGE
1.
The refrigerant charge is extremely critical. Mea-
sure charge carefully - as exact as possible to the
nameplate charge.
2.
The correct method for charging the rotary is to
introduce liquid refrigerant into the high side of the
system with the unit off. Then start compressor and
enter the balance of the charge, gas only, into the
low side.
The introduction of liquid into the low side, without
the use of a capillary tube, will cause damage to
the discharge valve of the rotary compressor.
NOTE: All inoperative compressors returned to
Friedrich must have all lines properly plugged with
the plugs from the replacement compressor.
Summary of Contents for WallMaster WE10B33A-B
Page 21: ...21 WIRING DIAGRAM MODELS WS08B10A C WS10B10A C WS14B10A C WS10B30A C WS13B30C...
Page 22: ...22 WIRING DIAGRAM MODELS WS16B30A C...
Page 23: ...23 WIRING DIAGRAM MODELS WE10B33A B WE13B33B B...
Page 24: ...24 WIRING DIAGRAM MODELS WE16B33A B...
Page 25: ...25 WIRING DIAGRAM MODELS WY10B33A B WY13B33A B...