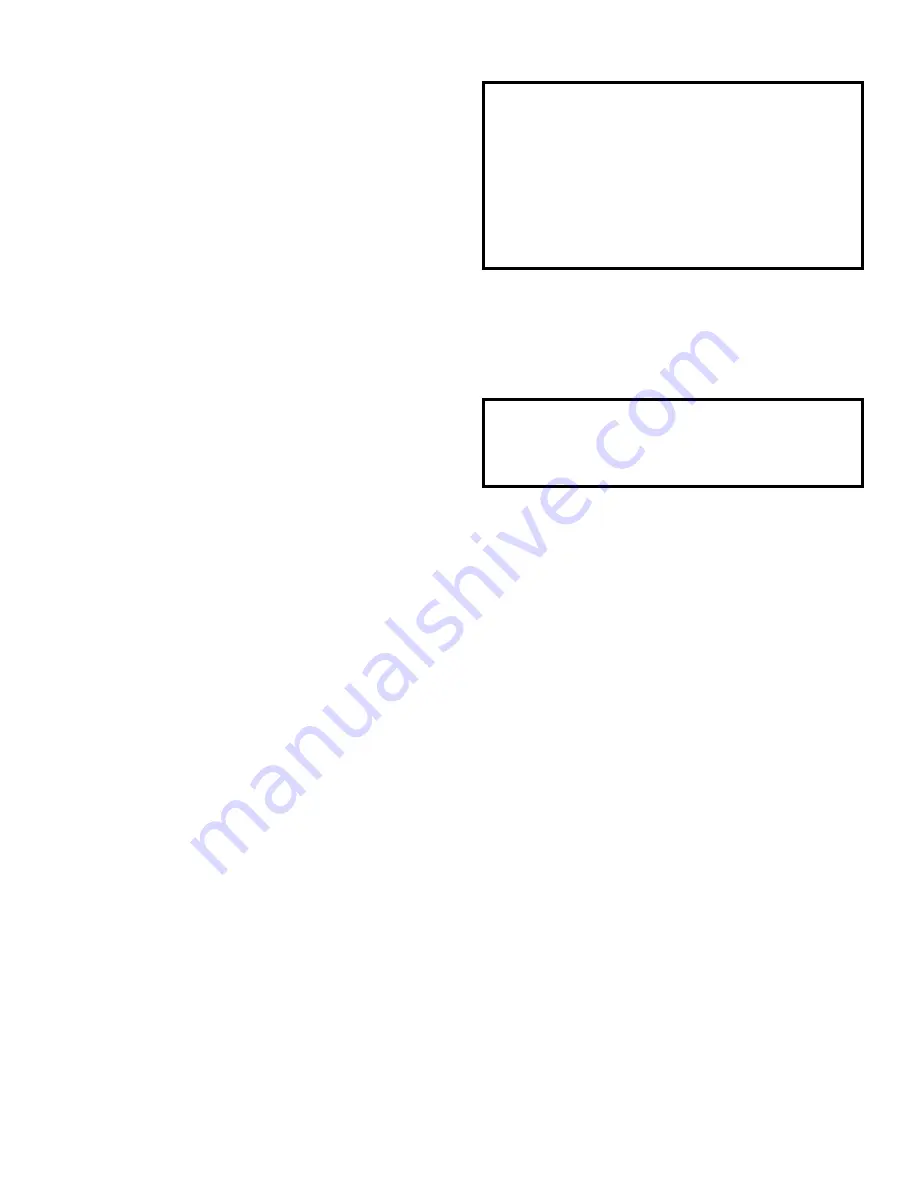
9
NOTE: This procedure can be speeded up by
the use of heat lamps, or by breaking the
vacuum with refrigerant or dry nitrogen at 5,000
microns. Pressure system to 5 PSIG and leave
in the system a minimum of 10 minutes.
Recover refrigerant, and proceed with
evacuation to a pressure of 200 microns or a
minimum of 10%.
11. Break the vacuum by charging the system from
the high side with the correct amount of
refrigerant specified. This will prevent boiling
the oil out of the crankcase.
NOTE: If the entire charge will not enter the high
side, allow the remainder to enter the low side in
small increments while operating the unit.
12. Restart the unit several times after allowing
pressures to stabilize. Pinch off the process
tubes, cut and solder the ends. Remove the
pinch off tool, and leak check the process tube
ends.
SPECIAL PROCEDURES IN THE CASE OF
COMPRESSOR MOTOR BURNOUT
1. Recover all refrigerant and oil from the system.
2. Remove the compressor, capillary tube and
filter drier from the system.
3. Flush the evaporator, condenser and all
connecting tubing with dry nitrogen, or
equivalent, to remove all contamination from the
system. Inspect the suction and discharge lines
for carbon deposits. Remove and clean if
necessary.
4. Reassemble the system, including a new drier-
strainer and capillary tube.
5. Proceed with processing as outlined under
hermetic component replacement.
HERMETIC COMPONENT REPLACEMENT
The following procedure applies when replacing
components in the sealed refrigeration circuit or
repairing refrigerant leaks. (Compressor,
condenser, evaporator, capillary tube, refrigerant
leaks, etc.)
1. Recover the refrigerant from the system at the
process tube located on the high side of the
system by installing a line tap on the process
tube. Apply the gauge from the process tube to
EPA approved gauges from the process tube
to the EPA approved recovery system. Recover
the CFC’s in the system to at least 5%.
2. Cut the process tube below the pinch off in the
suction side of the compressor.
3. Connect the line from the nitrogen tank to the
suction process tube.
4. Drift dry nitrogen through the system and
unsolder the more distant connection first. (Filter
drier, high side process tube, etc.)
5. Replace the inoperative component, and always
install a new filter drier. Drift dry nitrogen through
the system when making these connections.
6. Pressurize the system to 30 PSIG with proper
refrigerant and boost the refrigerant pressure
to 150 PSIG with dry nitrogen.
7. Leak test the complete system with the electric
halogen leak detector, correcting any leaks
found.
8. Reduce the system to zero gauge pressure.
9. Connect the vacuum pump to the high side and
low side of the system with deep vacuum hoses,
or copper tubing. (Do not use regular hoses.)
10. Evacuate the system to an absolute holding
pressure of 200 microns or less.