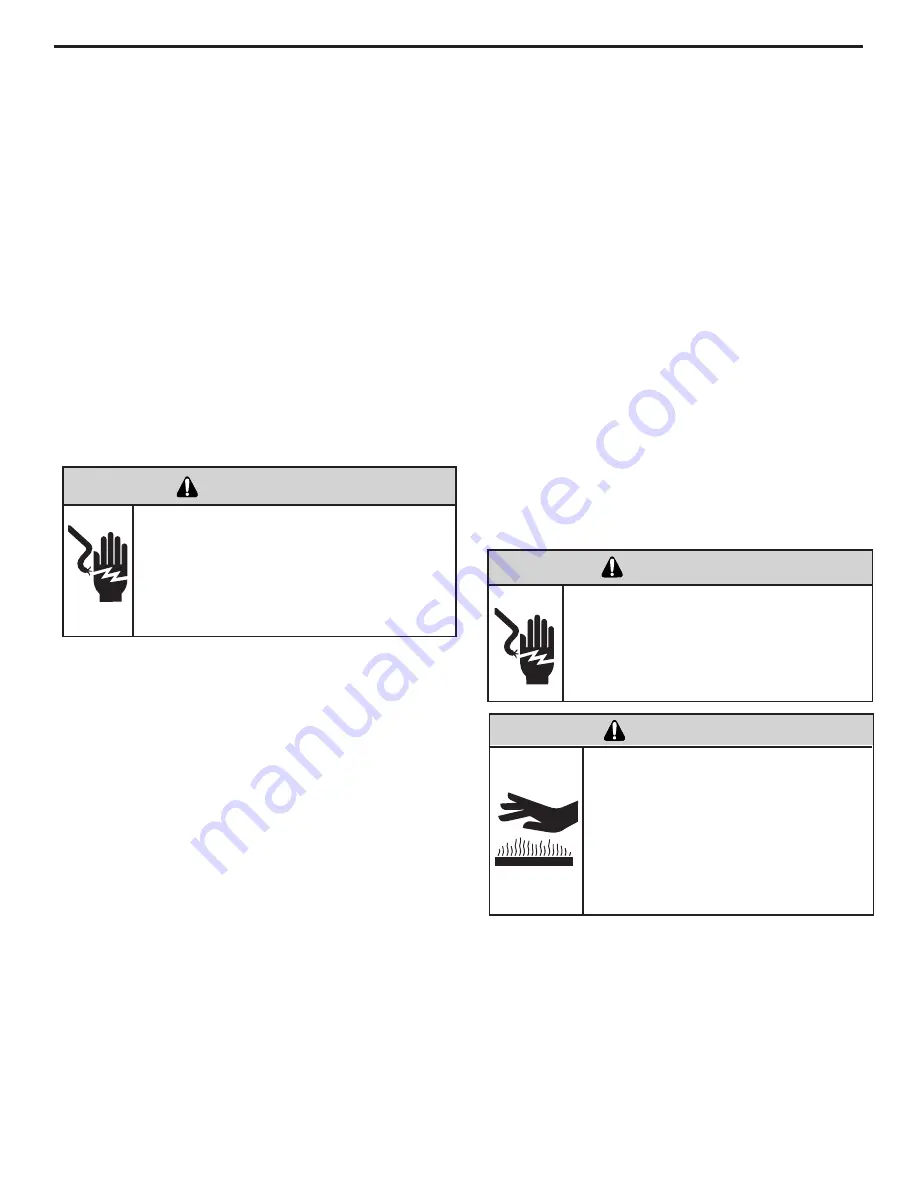
MeTeRING DeVICe
Capillary Tube Systems
All units are equipped with capillary tube metering
devices.
Checking for restricted capillary tubes.
1. Connect pressure gauges to unit.
2. Start the unit in the cooling mode. If after a few minutes
of operation the pressures are normal, the check valve
and the cooling capillary are not restricted.
3. Switch the unit to the heating mode and observe
the gauge readings after a few minutes running time.
If the system pressure is lower than normal, the heating
capillary is restricted.
4. If the operating pressures are lower than normal in
both the heating and cooling mode, the cooling
capillary is restricted.
locked Rotor Voltage (l.R.V.) Test
Locked rotor voltage (L.R.V.) is the actual voltage available
at the compressor under a stalled condition.
Single Phase Connections
Disconnect power from unit. Using a voltmeter, attach one
lead of the meter to the run “R” terminal on the compressor
and the other lead to the common “C” terminal of the com
-
pressor. Restore power to unit.
Determine l.R.V.
Start the compressor with the volt meter attached; then stop
the unit. Attempt to restart the compressor within a couple
of seconds and immediately read the voltage on the meter.
The compressor under these conditions will not start and will
usually kick out on overload within a few seconds since the
pressures in the system will not have had time to equalize.
Voltage should be at or above minimum voltage of 197 VAC,
as specified on the rating plate. If less than minimum, check
for cause of inadequate power supply; i.e., incorrect wire
size, loose electrical connections, etc.
COMPReSSOR CHeCKS
ELECTRIC SHOCK HAZARD
WARNING
Turn off electric power before service or
installation. Extreme care must be used, if it
becomes necessary to work on equipment with
power applied.
Failure to do so could result in serious injury or
death.
Amperage (l.R.A.) Test
The running amperage of the compressor is the most impor
-
tant of these readings. A running amperage higher than that
indicated in the performance data indicates that a problem
exists mechanically or electrically.
Single Phase Running and L.R.A. Test
NOTE:
Consult the specification and performance section
for running amperage. The L.R.A. can also be found on the
rating plate.
Select the proper amperage scale and clamp the meter
probe around the wire to the “C” terminal of the compres
-
sor. Turn on the unit and read the running amperage on
the meter. If the compressor does not start, the reading
will indicate the locked rotor amperage (L.R.A.).
external Overload
The compressor is equipped with an external overload
which senses both motor amperage and winding tem
-
perature. High motor temperature or amperage heats the
overload causing it to open, breaking the common circuit
within the compressor.
Heat generated within the compressor shell, usually due
to recycling of the motor, is slow to dissipate. It may take
anywhere from a few minutes to several hours for the
overload to reset.
Checking the external Overload
With power off, remove the leads from compressor termi
-
nals. If the compressor is hot, allow the overload to cool
before starting check. Using an ohmmeter, test continu
-
ity across the terminals of the external overload. If you
do not have continuity; this indicates that the overload is
open and must be replaced.
Certain unit components operate at
temperatures hot enough to cause burns.
Proper safety procedures must be followed,
and proper protective clothing must be
worn.
Failure to follow this warning could result
in moderate to serious injury.
WARNING
BURN HAZARD
ELECTRIC SHOCK HAZARD
WARNING
Turn off electric power before service or
installation. Extreme care must be used, if it
becomes necessary to work on equipment
with power applied.
Failure to do so could result in serious injury or
death.
18
Summary of Contents for CP14E10
Page 1: ...Service Manual Compact Programmable CP 14 18 24 ServMan 04 09 Models 2009 2008...
Page 31: ...29 ELECTRONIC CONTROL WIRING DIAGRAM 2009 MODEL CP24E30 CP14E10 CP18E30...
Page 32: ...30 ELECTRONIC CONTROL WIRING DIAGRAM 2008 MODEL CP24N30 CP14N10 CP18N30...
Page 33: ...EXPLODED VIEW AND LIST OF PARTS 2009 MODEL CP14E10 CP18E30 AND CP24E30 31...
Page 34: ...2009 PARTS 32...
Page 35: ...2009 PARTS Continued 33...
Page 36: ...EXPLODED VIEW AND LIST OF PARTS 2008 MODEL CP14N10 CP18N30 AND CP24N30 34...
Page 40: ......
Page 41: ......
Page 42: ......