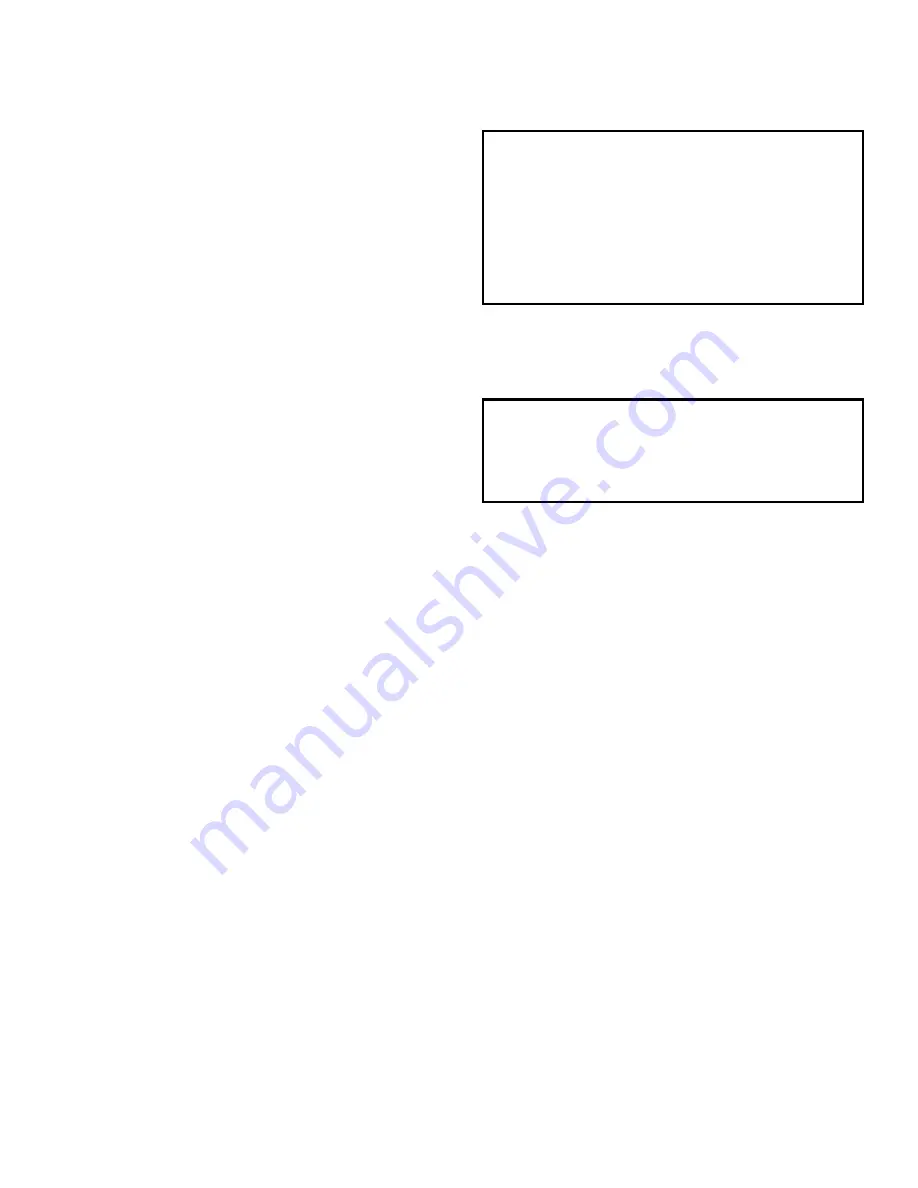
9
10.Evacuate the system to an absolute holding
pressure of 200 microns or less.
NOTE: This procedure can be speeded up
by the use of heat lamps, or by breaking the
vacuum with refrigerant or dry nitrogen at
5,000 microns. Pressure system to 5 PSIG
and leave in the system a minimum of 10
minutes. Recover refrigerant, and proceed
with evacuation to a pressure of 200
microns or a minimum of 10%.
11. Break the vacuum by charging the system
from the high side with the correct amount
of refrigerant specified. This will prevent
boiling the oil out of the crankcase.
NOTE: If the entire charge will not enter
the high side, allow the remainder to enter
the low side in small increments while
operating the unit.
12.Restart the unit several times after allowing
pressures to stabilize. Pinch off the process
tubes, cut and solder the ends. Remove the
pinch off tool, and leak check the process
tube ends.
SPECIAL PROCEDURES IN THE CASE OF
COMPRESSOR MOTOR BURN-OUT
1. Recover all refrigerant and oil from the
system.
2. Remove the compressor, capillary tube and
filter drier from the system.
3. Flush the evaporator, condenser and all
connecting tubing with dry nitrogen, or
equivalent, to remove all contamination from
the system. Inspect the suction and
discharge lines for carbon deposits.
Remove and clean if necessary.
4. Reassemble the system, including a new
drier-strainer and capillary tube.
5. Proceed with processing as outlined under
hermetic component replacement.
HERMETIC COMPONENT REPLACEMENT
The following procedure applies when replacing
components in the sealed refrigeration circuit or
repairing refrigerant leaks. (Compressor,
condenser, evaporator, capillary tube,
refrigerant leaks, etc.)
1. Recover the refrigerant from the system at
the process tube located on the high side of
the system by installing a line tap on the
process tube. Apply the gauge from the
process tube to EPA approved gauges from
the process tube to the EPA approved
recovery system. Recover the CFC’s in the
system to at least 5%.
2. Cut the process tube below the pinch off in
the suction side of the compressor.
3. Connect the line from the nitrogen tank to
the suction process tube.
4. Drift dry nitrogen through the system and
unsolder the more distant connection first.
(Filter drier, high side process tube, etc.)
5. Replace the inoperative component, and
always install a new filter drier. Drift dry
nitrogen through the system when making
these connections.
6. Pressurize the system to 30 PSIG with
proper refrigerant and boost the refrigerant
pressure to 150 PSIG with dry nitrogen.
7. Leak test the complete system with the
electric halogen leak detector, correcting
any leaks found.
8. Reduce the system to zero gauge pressure.
9. Connect the vacuum pump to the high side
and low side of the system with deep
vacuum hoses, or copper tubing. (Do not
use regular hoses.)
Summary of Contents for 2001 Hazardgard SH14J30A-1
Page 14: ...14 WIRING DIAGRAM FOR SH14J30A SH20J30A...
Page 15: ...15 Hazardgard Cabinet Parts...
Page 16: ...16 Hazardgard Chassis Parts...